Is my slab at risk left unheated through the winter?

I had grand plans for getting my garage closed in, and the rough mechanicals installed before winter. Life (uh… work, actually…) intervened.
I live in MN zone 6, and am building on alluvial sand from the Mississippi River. I built a block stem well on poured footings four feet deep (below frost line), 12 inches of compacted sand was placed on top of undisturbed sandy soil.
那时我迫使当地建筑规范聚氨酯t down 4″ of 3/4″ river rock – known colloquially around here as “radon rock” – followed by 6 mil polyethylene for radon gas mitigation. I then placed 2″ rigid foam panels to which I stapled PEX for in-floor radiant heat. (I know… the foam should be first, THEN the poly… sadly, despite protracted arguing and supporting literature from Joe L. inspector said “No, you will put poly UNDER your foam if you are stapling PEX”) Rebar 24″ OC was laid over the PEX, followed by poured slab 5″ thick.
I have my garage framed, roofed and shingled, but that’s as far as I’ve gotten. It is closed in with windows and door, but no rough plumbing, electrical or insulation is in. Well, except for 1.5″ rigid foam on exterior, and WRB wrap. It’s now November, and I fear I will not be able to get these things in and the boiler running before things freeze around here.
Should I worry if my slab is left unheated through the winter?
Any advice, or experience of others, appreciated. Thanks!
GBA Detail Library
A collection of one thousand construction details organized by climate and house part
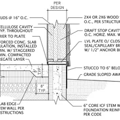
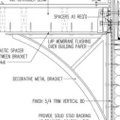
Replies
Kent,
The majority of garages are unheated. There is no need for you to worry.
Frost heaves propogate in the direction of heat loss, and in unheated buildings in zone 6 that's from the ground up- a real issue in some instances. But to have any frost for the heave requires substantial moisture, and with sandy soil it drains pretty well. In an insulated garage with at least some solar gains and well drained subsoil the odds of sustaining a frost heave of sufficient force to crack the slab are very small, but not necessarily vanishingly small.
Putting a slab-blanket over a slab inside an enclosed building with R10 polystyrene under the slab will not appreciably change the frost heave risk. Burying 4' of rigid R10 of "wing insulation" around the exterior perimeter would provide a dramamatic reduction in risk by better earth-coupling the slab edge region to the deep subsoil temps.
With the slab heated (even modestly) the risk drops to essentially zero, since the direction of the drive changes with the direction of the heat loss. As long as the air temp in the garage stays above the temp of the subsoil the risk is exactly zero, but even keeping at 10-15F above the outdoor air temp (even if that 's below freezing) the risk is very near zero.
While this doesn't address your question, it's unfortunate your rebar is sitting at the bottom of your 5" slab. It's value down there is next to nothing.
My rental store sells concrete insulation blankets. Use if desired, and sell later.
I didn't read this Q right... with foam already in place and all the fill, you should be fine. Dana has a great post.
Dana- thanks for the insightful and educational response. Science and opinion meld nicely in your response. My build has 4' of insulation lining the interior of the block stem wall, bottom edge sitting atop the footing, for something akin to "wing insulation". (I interpret "wing insulation" as a more nearly horizontal panel, flanking the stem wall.) I hope this provides at least a small measure of protection.
Mike- appreciate your observation. Rebar was set on one inch chairs, raising it off the PEX, and concrete fellas would occasionally reach into concrete to pull the rebar up into the mix. Yet, I would have been happier if two inch chairs would have been used. Good lesson for me when I pour next slab for house in a year our two.
Good to know, Kent. Enjoy the garage.
Kent, more ideas for the future pour. I Buy flat panels of wire mesh, place on top of rebar, and attach PEX to it. Then plastic on top of foam works too.