Relative strength of glulams, I joists, and trusses

I’m designing a flat roofed barn with a thin profile and need to span 40′. Which of the above options will give me the most strength and thinnest profile? Also, how closely spaced can these members be placed?
GBA Detail Library
A collection of one thousand construction details organized by climate and house part
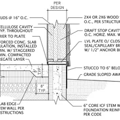
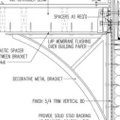
Replies
Consider a pole barn or steel building kit where the structural design work has been done for you.
Cali,
你的一个选择,胶合,不是真的椽s, they are used as beams. All three require engineering provided by the supplier. A call to your lumberyard and a truss manufacturer will quickly give you an accurate answer, but as a rule of thumb, open-web trusses will be one inch of height for each foot of span, and I don't think truss-joists can span forty feet - so realistically you may only have one option.
That's a good idea Jon. I will look into it
My question remains, however, even if only to satisfy my intellectual curiosity
My guess for the most compact is steel.
Thank you Malcolm
Cali, the primary factors that affect rafter (or other beam) span are material stiffness in bending, the shape and the size, with height (or depth) generally being a lot more important than width. Additional considerations include whether the load is uniform vs. point loads, and the shear strength at the ends to prevent crushing or cracking under load.
For comparison, there needs to be a constant, rather than all variables. In your case, I would evaluate based on which products reach the SAME strength with the thinnest profile. When it comes to beams and rafters, "strength" is measured by how far does the member deflect (bend) under the design load, and is the shear strength at the ends (or point loads) adequate for the design load. I would also want to know which is the best use of resources--the most "efficient".
As long as the load is relatively uniform, the most efficient shape (efficient in terms of how much material is needed) looks like a capital "H" laying on its side.
Because each of the products you mention use different materials, it's hard to say which is really the most efficient, but I would rule out a glulam (or related materials such as LVL or PSL) because a rectangle is not an efficient cross-section.
Either I-joists or custom-made trusses would work for you. I-joists need to be reinforced at the ends to prevent shear failure, and they have limited dimensions, but they are easy to get and to work with. Custom trusses are more likely to handle the same load and span in a shallower profile.
If efficiency of materials is not important to you, and you really want the thinnest assembly you can get, you would use solid LVLs or other engineered wood, with the highest modulus of elasticity (MOE) you can find, usually 2,000,000 psi but sometimes available in 2,200,000 psi. It's not an efficient use of resources but it will be the thinnest assembly.
Typical roof sheathing is 1/2" or 5/8" plywood or osb, typically spanning 16" or 24". If you want wider rafter spacing, you can use thicker sheathing, including solid 2x lumber which in some assemblies can span 6'.
If you can provide more specifics about what you want to achieve, it will be easier to recommend the best assembly for you.
Thank you for that detailed response Michael
Sounds like I joists or custom trusses are the way to go
The load will be uniform- mild california climate with solar array on roof being only load
I asked about spacing because my idea is that more members (I joists or custom trusses) spaced more closely together (maybe even 12" oc) will allow me to create a thinner assembly
A solar array may potentially cause a lot of uplift force from wind load. That’s something to consider.
Another thing to think about is that you said you want the thinnest profile. There are two ways to make a really long beam: make it beefy, with big flanges, to limit deflection, or use extra bracing. Bracing ties one beam to adjacent beams in a grid, like blocking between joists. If you can tolerate more braces between beams, you can usually use a thinner profile.
If you want a 40 foot clear span, I’d look into open steel trusses. Steel is going to give you much more ability to make that span with a lightweight structure than wood, even engineered wood. You can use the steel trusses to support conventional wood structural elements if you want so that you’re only using the steel to handle the really long spans, or you can just go all steel.
If all you really want is a barn with a big open interior, I’d call up one of the steel building manufactures and see if they have a preengineered building that will meet your needs. These go up quick, are fully document with all the engineering to make permitting easy, and they’ll probably be you’re cheapest option too.
Bill
Thank you Zephyr7. I'll look into steel framing
Do you have any experience with the hundreds of different companies out there?
不是,我的工作通常是设计facility going into the building, especially in regards to the power and cooling systems since I'm usually designing telecommunications facilities. I tell the architect guys how many square feet I need and the clear ceiling height and they make the shell part happen.
I’m a little bit familiar with the general Steel people, but I haven’t ever really worked directly with them myself. You might try call up so local general contractors that do commercial work and ask them.
I do have a commercial project, in a steel building, I have to visit in the next few hours and if the GC is onsite today (I'm hoping he is since I have project scheduling questions for him), I’ll ask if he is familiar with any of he prefab steel building companies. I think the steel building shell is the only part of this particular project that has been on schedule.
Bill
Cali, while I agree that steel will give you the smallest profiles and may be the most cost-effective, steel comes with a large carbon footprint--about one pound of CO2 released for every pound of steel used. Wood is a low-carbon material. So if you care about climate change, at least consider wood-based framing.
Note that most steel in the US is produced by reusing old steel, steel has been recycled forever in industry. I suspect that makes quite a difference compared to processing the raw ore.
Bill
Bill, yes the majority of steel used today is recycled or mostly recycled material. But the furnaces that melt the raw steel use incredible amounts of energy. If the steel is produced in the US, it's usually by using an electric arc furnace, which uses much less energy than the basic oxygen furnaces used in much of the rest of the world. But it's still a heavy emitter.
That said, most wood and wood-based materials are not zero carbon either, and as you know steel has a much higher strength to weight ratio than wood--comparing beams of equal size and shape, the steel one will be 20 times stiffer than framing lumber and 15 times stiffer than LVL. So if climate impact matters to you, you need to design a system and calculate the carbon footprint. But as a rule of thumb, if it CAN be done with wood, it will almost always have a smaller climate impact than doing it with steel.
Thank you both again
What is the required snow loading (or roof loading) rating in your location?
Why do you need a thin profile?
Are you willing to pay considerably more for a lower height difference between ceiling and roof?
Do you absolutely require a free-span, even if it costs you more? A 20ft free span is a much easier ask than a 40ft.
Generally, glulam beams and steel I-beams are considered too expensive to be used as rafters, and are instead used to support secondary rafters of some type (typically you see these described as "beams").
Wood I-joists can be quite useful if you don't have large holes in them for utilities, but 40ft is pushing their capabilities - if you go this route you'll need them as large as they're made for commercial applications, 24" depth, and you may even need to drop the spacing a bit (which is always the more expensive way to reduce deflection), going from eg 24" OC to 16" or 12".
A better option is going to be deeper trusses, whether wood, steel, or a hybrid. Somewhere in the 24" to 48" range at a guess.
What is the required snow loading (or roof loading) rating in your location?- Mild California coastal zone
Why do you need a thin profile?- Design choice. The roof will have 48” overhangs. I thought the beams would extend over the walls and into the overhangs. I talked to my architect this afternoon and he is talking about using appropriately sized trusses for the 40’ span and then adding traditional framing for the overhangs to maintain a thin roof profile. I didn’t know that could be done
Are you willing to pay considerably more for a lower height difference between ceiling and roof?- More, yes. Depends on what considerable is
Do you absolutely require a free-span, even if it costs you more? A 20ft free span is a much easier ask than a 40ft. Yes. Tractor barn
Generally, glulam beams and steel I-beams are considered too expensive to be used as rafters, and are instead used to support secondary rafters of some type (typically you see these described as "beams"). Thank you for clarification
Wood I-joists can be quite useful if you don't have large holes in them for utilities, but 40ft is pushing their capabilities - if you go this route you'll need them as large as they're made for commercial applications, 24" depth, and you may even need to drop the spacing a bit (which is always the more expensive way to reduce deflection), going from eg 24" OC to 16" or 12".- Hope it doesn’t come to 24” depth
A better option is going to be deeper trusses, whether wood, steel, or a hybrid. Somewhere in the 24" to 48" range at a guess.- Hope it doesn’t come to 48” depth!
删除d