Smell from first floor after finishing basement
Hello All,
Hope to get an assist with my smell situation.
I’m in Toronto, Canada and I have a bungalow from the 1950s. Last autumn we finished the basement, including exterior waterproofing, rubberized and damp proofing membranes, and spray foaming the interior wood 2×4 walls with closed cell insulation. The foundation wall is concrete block, with a (I think) double brick veneer above ground.
今年春季/夏季,我们有一个NE房间的地板/墙壁潮湿/潮湿/旧砖闻。我没有在一楼的其他任何地方都有气味。当温度在内部和外部温度之间发生巨大变化时,它似乎最强,即最近几天的天气更凉爽,尽管我没有将特定的触发触发到气味,但它不太明显。
The basement area under the room is the laundry facility and there is no odour there. I have checked for leaky dryer vent, moisture/leaky water line and no such success. Been in the attic looking for water penetration, also had the water proofer excavate down to the footing to check for water in the block that can’t evaporate and both cases no water. Opened up a piece of wall in the basement corner and scraped out the spray foam and no water, that said the brick and foam were moist to touch.
Based on a previous post and answer by Dana in this thread:
//m.etiketa4.com/question/musty-smell
I’m starting to suspect the odour is caused by not have a vapour barrier in the section where the floor/rim joists are ie between spray foam in basement and tarpaper barrier in first floor walls. I am now thinking of spray foaming this area to see if it will resolve the odour. I’ve attached a diagram of the current situation.
Has anyone ever run into a situation like this or have any opinions?
I would appreciate any feedback, I have my original contractor and others out to investigate and no particular help.
Thanks,
亨利
PS Updated the diagram to have the veneer on the block!
GBA Detail Library
A collection of one thousand construction details organized by climate and house part
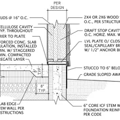
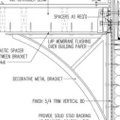
Replies
I wouldn’t be surprised if your smell is coming from the damp block by way of the air leakage path you show in your drawing. By sealing the block on the inside, it’s likely staying wetter longer. I’m surprised the gap shown in your drawing wasn’t already sealed, but I suppose it could have been missed.
What you don’t want to do is seal things with spray foam in a way that keeps your rim joist wet with no possibility to dry out. Make sure you have a good capillary break on top of the masonry part of the wall.
Bill
Could you explain a bit more on the capillary break? I'm looking to do CCF on my 1940's basement foundation wall/rim joints- do you think there is a capillary break between the sill place and foundation back then? The first floor walls are blown in insulation with a mix of drywall and original plaster walls.
Kevin
I doubt you had a capillary break intentionally installed back then. A capillary break is basically just a piece of water impermeable material placed between the top of a masonry wall and the wood structure of a house. The purpose is to keep moisture from wicking up the masonry wall and wetting the wood.
I’ve used pieces of HDPE (high density polyethylene) sheet for this purpose, mainly because it’s cheap and fairly stiff so it’s easy to slide into small gaps when doing a retrofit. Dana has often recommended EPDM, roofing membrane material. EPDM is more flexible, so a bit harder to stuff into small gaps, but it’s more commonly available at building supply places. Both materials will work well as capillary breaks.
Bill
最好的猜测:像浇注的混凝土(也许更多)一样,CMU块具有强大的毛细管抽签。如果底层和墙壁之间没有毛细管断裂,则闭孔聚氨酯将干燥朝向地下室,那么水分的唯一途径就是上升。由于足够未涂漆的级别外部暴露(至少一英尺,两英尺更好),它可能会朝外部干燥。
砖贴面中的雨/露水水分也可能在该位置提高高水分水平。如果在砖块的底部底部附近没有每三块砖每三块砖,并且在顶部每三个砖的底部都没有哭泣,以创建一个对流的干燥驱动器,从而添加它们可能会减轻问题。
Thanks for the feedback Bill & Dana. There is a couple of feet of exposed block above grade, however being the NE side as well as the cedars that are planted which are obstructing sunlight, I'm not sure how much drying action it's getting.
As far as weeps go inside the brick. There are no weep holes in veneer. I doubt/haven't seen any kind of weep plate/sill or whatnot. Any concerns with putting weeping holes in the brick veneer around letting rain/snow in?
Thanks,
亨利
>"Any concerns with putting weeping holes in the brick veneer around letting rain/snow in?"
Weeps & vents are standard construction in plenty of rainy-snowy areas. The greater concern it keeping the insects out, which can be achieved with purpose-made inserts.
Understood and I've had a conversation around weeps and vents, the only catch is if they are installed during construction my understanding is that there should be a weep sill or something to allow any moisture/water to run out behind the brick. In the current brick, there is no weep holes so I'm pretty confident no weep sill. As part of a retrofit, would one need to be installed?
我关心的是不要打破现有的“雨屏”。
这是一个合理的问题,还是我想这件事?
亨利
This is a good example of why more vapor permeable foam (eg, unfaced EPS) that allows more inward drying and results in drier block is better.
So you can dump moisture directly into the basement in perpetuity? No thanks. The block doesn't care if it's damp.
Run the numbers - it's insignificant. The block doesn't care, but the owner sure does.
Jon, I've been in plenty of damp basements, and find that owners prefer them to be dry. ;-)
>"Jon, I've been in plenty of damp basements, and find that owners prefer them to be dry. ;-)"
即使是II型EPS的1英寸,水分通过墙壁出现的速率与标准内部乳胶涂料(=“ Ainn't Doce”)相当。
乔恩·r是正确的 - 在地下室的室内RH发生的事情方面,它微不足道,但与木材的水分含量与与该墙壁的顶部接触时产生了真正的不同。即使是从楼上的干燥空气进行干燥的空气的少量通风也可以控制地下室湿度,如果通过泡沫扩散是水分的主要来源。在夏季,高露点室外空气的“ -a”气候泄漏通常会比整个粉底墙通过1英寸II型EPS提供数量级或更多的水分。
添加内角的照片
Dana and Jon, I'm not a mechanical engineer so I'm learning these calculations on my own. In the interest of education, how does this math look to you:
Saturated block at 55°F = 0.45 in•Hg vapor pressure
Interior air 65°F, 45% RH = 0.27 in•Hg
Difference 0.18 in•Hg
1” EPS = 3.5 perms = 3.5 grains/hr per sf per in•Hg
在0.18英寸•Hg时,每平方英尺为0.63粒/小时。
Assuming 500 sf of wall area, that’s 315 grains/hr.
Assuming 5000 cf of volume in the basement at 0.08 lbs/cf, that’s 400 lbs of air. So the air is gaining a little less than 1 grain per cubic foot per hour.
每立方英尺的1粒水大约对应于室温下RH的1%。因此,只要地下室每小时的空气变化超过1/小时,就没有问题。但是,如果空气每小时变化少一次,RH会继续攀升吗?
所以一个trivial 1 pint per day that may or may not need to be removed. Compare that to the 8 pints/day that isattributedto an occupant. And to the value of reducing the chances of mold growing on the block and some of the odor making it into the interior.
Adding exterior photos
HGCANUCK,希望您现在已经解决了问题。我在1955年在北弗吉尼亚州的1955年砖/街区中处理了类似的问题。你的故事听起来像我的。可怕的气味,我的地下室成品部分也有潮湿的发霉墙。长话短说,我相信您可能是由于温暖的空气逃脱了灰泥和砖之间的3/4英寸缝隙而导致的水分/凝结泄漏到开放式(可能)干燥的街区的顶部……慢慢地闻到了这个地方。我住在两个像这样建造的旧房子里,最后以相同的方式解决了问题。
Another source....if those are plastic or flexible metal vents in your eaves, I would check for rodents in the attic. Norway rats...they really cause a stink and can/will go down your walls into your basement block. I had this problem throughout....fixed this problem by removing those flex vents for rigid plastic soffit trim and vents. They climbed the exterior wall along the A/C lines, then squeezed into the soffit. Been there..done that...it's ugly.
I solved my moisture issue (and the rat issue) by crawling back in the attic eaves and foaming the top of the gap into the attic and then foaming the gap at the bottom of the wall (top of the block in the basement) where the warm air leaks up into the wall. Sealing the gap at the top of the basement wall made it significantly more comfortable. It also took care of most of the smell. Additionally, I had a waterproofing company seal the exterior of the basement wall with a mortar parge, apply a liquid waterproofing membrane over that, then installed a drainage board to a footer drain. That alone reduced RH in my basement by over 20%.
I just installed a two head Mitsubishi Hyper Heat Mini-Split which will help somewhat with any additional humidity.
Hope this helps. Some of this might not pass the 'smell' test of GBA, but it solved my problem and I've seen no ill-effects so far. I'll finish portions of the basement with 1/2" XPS glued to the block with rock wool in 2x4 walls.