47 Years of Fiberglass Against Basement Interior Wall

1973 – Zone 5B ranch with a conditioned finished basement. Standard 2×4 wall against foundation walls with R-11 fiberglass. Attached pictures.
T1-11 and wallpapered 1/2″ drywall. Which the second owner covered with glued up maps.
Removed a few sections of T1-11 to check for moisture/mold. As standard BS practice says this wall is a bad idea and ripe for moisture problems.
To my surprise (might change once all the walls are open) it seems like all these years it has stayed dry enough that there doesn’t seem to be any major moisture issues. Mice seem to have been more of a problem than moisture. As I found an old little nest.
More background –
3′-6″ overhangs which helps to keep rain/snow away from foundation. Along with good sloping grade around most of the perimeter. Humidity levels of basement stay pretty consistent with main level.
My guess is the overhangs and grade are keeping the exterior foundation dry and helping to keep exterior moisture drive to a min.
Question
Plans were to rip everything out, install rigid foam on walls and floor, then build out.
* * *在我继续. .我承认我知道this is against the building science gospel.. and would not do this on a new install
The lazy part of me started thinking… if these walls have been like this for 47 years without moisture issues, what if I just removed gyp/T1-11 and then installed EPS foam to studs, furring for electric, and new drywall. Avoiding moving the walls out.
Easier and cheaper way of getting to the goal of R20 when combined with the R-11 fiberglass already there. Air sealed from new foam on floor > wall > rim joist.
Should I slap the laziness out of me and just tear it all down.. and install studs inside the foam…or since this has a track record of being okay for 47 years…. does it lower the risk and make it acceptable for this home?
Final note.. if you did this and sandwiched the existing fiberglass wall.. would you want more perms / drying from interior side or less?
我可以告诉覆盖概率是1/2”round 10 perms and not sure on the gypsum with the wallpaper and glued maps. But if higher perms is needed would R-10 EPS insulfoam be enough?
GBA Detail Library
A collection of one thousand construction details organized by climate and house part
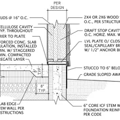
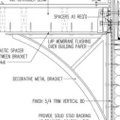
Replies
Interior side EPS will significantly reduce inward drying, increasing risk. More fiberglass between extended studs would be much less of a change, only making the concrete side a little colder.
It would benefit a lot of people if it could be reliably determined when/where no-foam basement walls work. A similar but even more extreme "air and vapor permeable" design is exposed Ecocell. In the one case I saw, it was working well, despite the "interior air will get to the concrete and condense" theory.
+1!!
The last thing you want to do is to make the interior vapor retardency lower, and the studs colder.
Sometimes it's possible to twist the existing studs sideways and have enough room to slide in some 1.5' or 2' foam board (requires full removing 2 studs). With 2" of polyiso (R12-R13) and a trimmed & compressed R7 batts in the (now 1.5" deep) stud bays gets you to the current code-minimum performance, with a center-cavity R of about R18, but with far less thermal bridging than the IRC prescriptive R19 (which is really only R18 at center cavity when installed at 5.5" depth in a 2x6 stud bay.)
Cool little trick twisting the studs! Thanks for sharing.
My old fiberglass was dirty from 40 years of acting as a filter for the air infiltration. Surprised how clean it is.
T111 is not very attractive, why not put foam outside and have the wall right side out?
There are a lot of dangers from moisture in basements, although you seem to have dodged them so far. One of the dangers is that the basement wall is colder than the dew point of the interior air, and there is a way for interior air to reach the wall, and when that happens moisture condenses. In many places the summer temperature below ground is cooler than the dew point of the outside air. You can also get situations where the winter temperature of the basement wall is below the dew point of the interior air, although that's rarer.
For most basements, year-round the dirt behind the wall is cooler than the interior temperature. If that's the case, adding more insulation to the wall will make the interior surface of the wall colder, year-round. While you've had no trouble to date, the risk of adding more insulation is that the marginal change in the temperature of the wall will be enough to push you over the border from non-condensing to condensing, and you'll start having moisture problems where you never had one before.
Unfortunately, there really isn't an analytic way to say whether that's going to happen, there are just too many variables. The safest thing to do is to put foam board against the wall, which will serve as an air barrier to keep warm humid air away from the wall, and if condensation occurs won't absorb it.
Thanks for the replies.
After reading your responses and thinking about it more.... it seems to make the most sense to move the walls out and add foam.