Adding exterior foam

I’m re-siding a large addition (built in 1988 by previous owner) to my 1890s home just north of Toronto, Canada (Climate zone 5A?) and plan to add some rigid foam on the exterior in the process.
The wall assembly consists of 2×6 walls filled with fibreglass batts with an interior poly barrier under the drywall. On the exterior it seems there is no structural sheathing or house wrap, just 1″ of XPS tacked to the studs. The seams in the XPS are not taped (!!!). Needless to say my home did not perform well on the blower door test I had done last spring.
I’m planning to remove the existing siding, tape the seams of the existing XPS, add a Tyvek WRB, then a 1.5″ layer of faced EPS over that and tape the seams, strap it, and side it. I think I’m in the right fluffy to rigid ratio to eliminate the condensing surface inside the foam sheathing, if that’s an issue.
I’m wondering about any concerns you folks might have with this approach. Should I add sheathing? With the interior poly barrier and the now taped XPS, wrap, and EPS am I creating a mould sandwich? How does my plan look?
I’m an avid reader and subscriber of the site and would appreciate any feedback.
Thanks!
GBA Detail Library
A collection of one thousand construction details organized by climate and house part
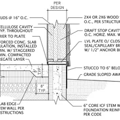
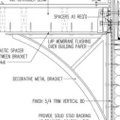
Replies
At 2.5" of 1.25lbs or denser polystyrene you'd have ~R11.5 performance or better at temperatures that matter from a dew point control perspective, even assuming the XPS is fully depleted of its blowing agents.
Without structural sheathing to protect and a condensing surface that is above the average indoor air's wintertime dew point there isn't much risk. With 1.5" unfaced EPS and 1" of XPS there is still more than 0.5 perms between the fiber in the cavities and the exterior. A 5mm or deeper air gap between the siding and EPS would be a sufficient capillary break between wet siding & foam keeping the foam mostly-dry even during wind-driven rain, and would create a drying path for any of the moisture that blows by the siding.
The most important thing to get right is the bulk moisture handling- the window flashing details are critical. The additional 1.5" of EPS is cutting the drying capacity by a third or more, so make sure to lap it all correctly to move the moisture out rather than in, with no gaps. (The taped seams helps.)
Note that Dana said "unfaced EPS". Faced EPS and poly leaves basically no ability to dry in either direction.
That is indeed a critical distinction between the " ...a 1.5″ layer of faced EPS..." described and what's recommended.
If the whole thing is dry when it comes together and all the details are PERFECT (now and forever) it'll be fine. But if using foil or 4mil polyethylene faced EPS there is no reasonable drying path, and there's no such thing as "perfect" when it comes to construction (and time.)
穿孔收入或半薄permeable polyolefin facers could work, if the facers are sufficiently permeable. A generic spec of " < 1 perm" isn't enough to go on.