Insulation and heating for small office space – Wisconsin (6B)

Hi. We are converting a small detached garage into an office space. The space is 12×20. It has a new metal roof over ice/water shield over old wood decking and new siding over housewrap over old wood siding. All walls and roof rafters are 2×4. The roof is unvented.
模具:前面的屋顶在漏水所以一些of the roof decking was wet. While the new roof we resolved the leaking issues, we did have some mold start to grow on those boards – south facing roof – after the new roof was put on and winter was setting in. We have cleaned up the mold and our plan for that is to leave it open for a bit – install the insulation on the north side of the roof and all the walls and then get the heat running – and make sure it doesn’t return. Once the heat is on we will paint that whole side with mold-inhibiting paint prior to putting up the insultation.
Heat – we are looking at putting in cove radiant heaters.
Insulation –
Floor – concrete. we are planning to use Dricore insulated subfloor with plywood on top
Walls – we were thinking of 2 inch rigid inbetween the studs and then an uninterrupted layer of 1 inch rigid on top of the studs – tongue and groove. Then shiplap finished walls.
Ceilings – I am stumped. We want to leave this open (vaulted) but the rafters are only 2×4. I have read through many questions/answers and posts but can’t figure out if we should leave space between the old roof boards and the new insulation or make it tight? Considering putting furring strips between each rafter to leave space and then rigid and then mineral wool – adding to each rafter to get enough R value – or do we put the rigid right up to the roof boards and seal the edges with foam? Or spray foam the roof? Do I need to be concerned about the mold coming back if we take the precautions mentioned above? And if so, better to have air space or not?
I know that’s a lot of information – my main question is around the insulation – specifically in the roof – but I welcome any advice or experience on the other items as well. I would like to do this correctly and as green as possible.
Thank you in advance for your help and advice.
GBA Detail Library
A collection of one thousand construction details organized by climate and house part
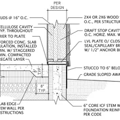
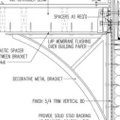
Replies
Wisconsin isn't in zone 6B. Southern WI is 6A, northern WI is 7A. Got a ZIP code?
Had this been thought out ahead of time it would have been pretty cheap and easy to install a few inches of reclaimed roofing foam on the exterior of your roof deck, under the new metal roofing to make up for the skimpy rafter depth. The last thing you want to do is a cut'n'cobbled foam approach tight to the roof deck, since over time any edge sealing you do is guaranteed to fail.
Those look like full dimension rough sawn 2x4s (?), with a full 4" , not 3.5" like a milled 2x4. With soffit to ridge venting (you'll have to create those holes) it's fine to use cut'n' cobbled foam board. Bear in mind that any fiber insulation on the conditioned space side of the foam has to be lower R than the foam. In zone 6A the interior side insulation can be just shy of 50% of the total R, but in 7A it should be no more than 40%.
So for an example, say those really are full dimension 2x4s. Installing 3" of reclaimed 2lb roofing polyiso would be about R17. Installing milled 2x4s perpendicular to the rafters would be enough depth for R15 fiberglass or rockwool batts, and it would provide an R15 thermal break over most of the rafter edge area. R17/(R15 + R17)= 53% of the total R, which means it would be just fine in a zone 6A location, but would be a bit marginal for a 7A location. But using R13s would yield R17/ (R17 + R13) = 57% of the total R being the exterior side foam, which is almost enough for all of zone 7, and close enough that simply using vapor barrier paint on the ceiling gypsum or 2-mil nylon (Certainteed MemBrain) behind the gypsum would limit the moisture uptake in the fiber layers to tolerable levels and still provide a drying path.
A thermally-broken R30-R32 isn't terrible, even though it's not quite up to the current IRC code minimum performance.
This outfit in Reedsburg seems to have a bunch of factory-blem 1lb polyiso for less than half retail, and might trade in reclaimed goods too:
https://racine.craigslist.org/mad/d/reedsburg-factory-seconds-of-poly-iso/7013387064.html
The scrap rate on cut'n'cobbles is pretty high, so it's easy to work around broken corners or major dings (and just ignore the minor dings.)
Running this search on your local craigslist might turn up a local reclaimer nearer to you:
https://madison.craigslist.org/search/sss?query=rigid+insulation