Vapor Retarder for Converted Shed

Hello everyone,
I’m converting a simple Amish built shed into a conditioned office/workshop and really need help with how to best finish the walls. Building is 12×24 on skids with a slanted shed roof 2/12 pitch and lots of windows (50% are operable with screens). Floor is double layer of plywood with 3” spray foam insulation underneath the structure. Ceiling is 2×8” joists 16” OC fitted with smart baffles creating a 2” air gap and covered with 5.5” HempWool bat insulation. The roof is standing seam metal with an underlayment and then OSB or plywood sheathing. I’m also installing a 4” round soffit vent on each end of each bay (36 of them). There will be a minisplit HVAC unit installed and a sink, but that is it. No cooking or bathroom or full time living in the studio.
墙壁是2×4、16 LP Smartsi OC 3/8覆盖着ding (inside appearance is OSB material, this is not the SmartSide 76 product, it is one that has installation instructions indicating the need for a barrier unfortunately.) No barrier was installed prior to delivery. I have already installed HempWool bat insulation, (but can remove and re-install if needed) into each bay. Do I need to retrofit a vapor membrane or foil into the bays prior to installing the insulation? Should I paint if with some sort of sealer and call it a day? The rest of the wall will just be T&G painted white pine boards and ceiling similar but stained.
We are located in the southern tier of NY, so zone 5 or 6 I believe. Summers are hot and humid and winters are cold. After so much research, I’m really struggling with what to do about the lack of a barrier between the siding and the insulation, and also want to know the best approach to finishing the inside prior to placing the T&G.
There are no codes I need to comply with due to this being listed as a hobby shed, so I really just want to do what will make the building breathe and function best. Also trying to keep the structure as low VOC/toxin as possible.
Many many thanks in advance for your suggestions!
Regards,
Laura
GBA Detail Library
A collection of one thousand construction details organized by climate and house part
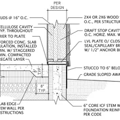
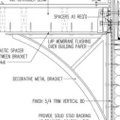
Replies
Hi Laura,
I’m giving your question a bump. It sounds like a great project. I wonder if asmart membranemight be the way to go. I look forward to hearing what builders suggest.
Thank you so much Kiley! I found some info last night about the LP smartside panels that were installed. Mine are vertical 4x8 panels with board and batten on the seams. Supposedly this is good thing for moisture and all that? The space is pretty tight and even with only just the walls currently insulated, I can heat the place with a very small heater. My contractor friend who is going to help me install the mini split just said that the HempWool is dense and handles moisture differently than fiberglass or mineral wool, so should be ok without a barrier on either side. The space will be used as a letterpress printing shop and likely just myself working inside at any given time. Just wanted to mention this in case these details can help with the reasoning process. Thanks all! : )
The first thing I would do is jack the skids up out of the dirt and get the building up on concrete deck blocks.
Is there something under the building covering the spray foam to keep the critters out?
The walls are a bit of a problem in that the siding is generally regarded as a rain screen and not as your only water resistant barrier. Removing the siding installing a water barrier is the way it should have happened, going back now would be a bitter pill. If you built a vented channel in board of the siding things would have some chance of drying out before mold and rot could get started.
Your wall will also need an interior air/vapor barrier behind the T&G pine.
I like to see a layer of drywall as a fire break without it this place could burn to the ground in 5 minutes. It is also a smart idea to have a 15 foot separation between the shed and any other building as a fire break.
Be sure to check many locations “sheds” are not allowed to have electricity or water and still be a shed.
Note the electrical national code applies to all building “shed” or not. If you want more than one circuit in this building it must have its own panel and grounding .
What is your plan for dealing with the waste water?
Will you vent the drain thru the roof?
How will you stop the supply and drain pipes from freezing under the building?
The last time I was in a around a letter press in 1977 it seemed like you could cut the VOC out of the air with a knife. I am sure the inks are different today.
Walta
Thank you so much for your detailed response and thoughtful questions. Unfortunately, I am unable to remove the siding and install a barrier, and all other things you have asked about have been dealt with already. The building is on a concrete slab and drainage has been dealt with. The building is in the middle of a field, nowhere near another building.
Do you have any ideas for a solution for a water resistant barrier to install in the bays prior to the insulation? That would be my only way to mitigate the situation at this point. Many thanks for your help!