What is the best way to treat the main level floor on a coastal home elevated on pilings?

我有一个客户有一个湾前家里eastern shore of Virginia that is built on pilings that put the bottom of the main level framing about 10′ off the ground. The majority of this space has been enclosed for parking and storage and houses the base of an elevator shaft. There are codes dictating the construction of these in-fill spaces limiting their connectivity to the structural elements of the elevated house. The concept is that storm surge or shore erosion damage would be isolated to this space. The ceiling in the enclosed portion of the space is a dropped panel ceiling with batt insulation between the I-joists. The main mechanicals are in this area as well so there is duct work as well as plumbing pipes above the dropped ceiling. A portion of the area under the main level is a carport and a covered patio area. Above the carport is the kitchen where my client has been having trouble with tiles coming loose after repeated tries to re-secure. We opened up the ceiling of the carport to hopefully shed light on what was going on . The ceiling had vinyl soffit over taped and primed drywall. When we started removing the drywall we were immediately greeted with the musty smell of mold. There was a bulkhead extending out from the garage area that enclosed a steel beam and a duct trunk line for the heat pump. When the insulation was removed over this bulkhead at the end opposite the garage we found that the bottom of the sub-floor was black and wet. Upon removing more insulation we found more mildew though not consistent and nothing as bad as the initial find. With the insulation down we also noticed that the Advantech sheathing was tight at the long seams instead of having the prescribed 1/8″ gap. I figured that the elevated moisture content was causing enough push at these joints to cause the tile failure. The mold and moisture appear to be caused by duct leakage focused on that area where I assume that there was a gap in the batt insulation creating a cold spot for outside air getting into the ceiling to condense on. I felt that the drywall approach to air seal the ceiling wasn’t a bad one but the fact that it does not run continuously through the garage and the fact that the slab has settled several inches in places and taken the infill walls down with it have created to many places for outside air to get into the cavity. My thought for a repair, though far from a perfect one, would be to encase the duct trunk and the supply ducts that are exposed above the carport with foam to insulate and seal them hopefully eliminating the problem in this area. Ideally we would remove all the ceilings inside the garage and out to foam but this is not in the budget. Does this sound like it will work? If so what type of foam would be best? I would opt for closed cell but should I be concerned about the fact that it is the kitchen and there are a lot of plumbing lines in this area so if a leak were to occur above, the foam would trap the water in the wood structure instead of showing up in the drywall ceiling below?
GBA Detail Library
A collection of one thousand construction details organized by climate and house part
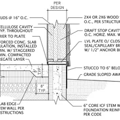
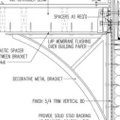
Replies
Hi Mike,
I think you want to follow a cold-floor strategy (http://www.finehomebuilding.com/2012/03/08/how-to-insulate-a-cold-floor). I would also make sure the ducts are sealed and try to air seal as much of the structure as possible while it is exposed.
A decoupling membrane (like Schluter) would probably resolve the tile cracking problem.
Mike,
This problem is due more to the leaky ceiling above the carport than it is to duct problems. That said, it's clearly important to ensure that all duct seams are sealed with mastic or high-quality tape, and that all ducts are adequately insulated -- so if the ducts have defects, they should be fixed.
The source of the moisture is exterior air. This humid air is entering the floor cavity during the summer and accumulating in the cold subfloor. The subfloor is cold because the house is air conditioned.
Tracking down all the air leaks into this floor assembly is tricky. If there are any transitions between ceiling areas -- for examples, interruptions by carrying beams -- these transitions introduce opportunities for air leaks. Air leaks at the perimeter of the ceiling (the rim joist area) must all be tracked down and sealed -- probably with spray foam.
This type of air sealing work requires fastidious attention to detail. When you are close to sealing all the cracks and leaks, you might consider installing a continuous layer of rigid foam on the underside of the existing ceiling, followed by new drywall. That would be an excellent floor assembly.