A very low addition…

We’ve been contracted by a repeat client to build a small dining room addition (11′ x 12′) attached to a contemporary ranch in Maine. Due to very difficult access issues, the addition has to be supported on sonotubes. Bottom of joists (2×10 with fg batts) will only be 2-3 inches over grade.
I’m concerned about moisture migration from ground into joist bays as well as air circulation under the addition. We’re planning to use PT 1/2″ ply with caulked seams on bottom of joists wrapped in hardware cloth. There will be good overhangs on the two eaves walls and none on the gable end. It’s a flat site with mature gardens all around, so pitching the grade isn’t a possibility. Oh, and the homeowner won’t let us use gutters. I’ve shared my concerns about these decisions, but it is what it is. They are good people and I want to do this right for them.
What do you think? Teno barrier applied to bottom of ply to limit moisture upwards? Sealed 3/4″ T&G subfloor to limit moisture migration downwards? Other approaches and/or concerns?
Thanks,
Ron Letourneau
Renaissance Construction
GBA Detail Library
A collection of one thousand construction details organized by climate and house part
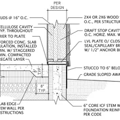
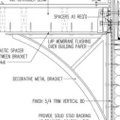
Replies
Ron,
Any reason why you can't put the addition on a slab on grade?
Hi Martin,
Thanks for the quick response!
The location is surrounded by extensive, mature gardens barely providing room for a wheelbarrow. The gardens are planted in the spaces between exposed and just buried ledge. The ledge doesn't provide room for much if any sub-slab foam. Plus, the homeowners want to do this on the cheap.
Thanks again,
Ron
Ron,
I wouldn't build a house (or addition) on piers with the joists only 2 or 3 inches above grade.
The fact that your customers have plantings that they like doesn't invalidate basic construction rules. If they want an addition at that location, you will either need to include a short staircase with three or four risers so that the addition is at the proper height, or you are going to have to move or destroy some of their plantings so that you can make preparations to pour a slab.
Two of your sentences are enormous red flags:
"They are good people and I want to do this right for them" and
"The homeowners want to do this on the cheap."
You're the expert. Explain the facts to them, and then either do it right or walk away from this job.
If there is room for 2-3" under 2x10 joists, why isn't there room for 2-3" of foam and a 4" slab?
No matter how you slice it, a wood-frame floor package with NO future access to the underside is questionable. I don't see how you can keep that from eventually rotting out, unless you build it entirely out of PT, which is dubious from a health standpoint.
I have a different view.
Use ground contact rated pressure treated lumber for the floor joists and rims and any wood construction material close to the ground (including plywood). Use stainless steel fasteners (not galvanized). Lay a bullet proof water and vapor barrier (black so it can't be seen) on the ground. Allow air circulation to and through the underneath. Insulate the dining room floor to appropriate local R value with cellulose, rigid foam or spay foam. Provide critter control and protection of the layed-on-ground vapor/water barrier using a vinyl or PT wood (can be painted) perimeter lattice or something pleasing, backed by 1/4" hardware cloth, installed on the vertical (can be set back underneath if necessary).
If you put a vapor barrier underlay on the interior flooring you will not have a problem with the joists' pressure treatment off-gassing entering the room. Most underlay is a vapor barrier these days. I really like db4flooring as it is modified mass vinyl that also deadens sound transmission (which can be a problem with a raised floor on piers). The new version of PT lumber is considered safe and is actually used in playgrounds.
http://www.dbsoundcontrol.com/
Use hidden gutters:
http://forums.jlconline.com/forums/showthread.php?38181-Hidden-rain-gutter
Flitch
Am I misunderstanding something here Ron? If bottom of joist is only 2-3" above grade how do you propose Installing the plywood to close the underside of the framing?
My assumption is that he would frame the floor, install PT plywood on the top, then flip it over. Not sure what else you could do.
Pressure treated wood offgassing? Dubious? Show me one person affected by pressure treated floor joists. I have installed thousands of feet of PT.
Gravel, plastic, piers, install PT joists right to the ground, gutters. It's a compromise and the cost is low.
Thanks guys. I know that those of you who offered the most cautious approaches are correct. However, as we all know, there are compromises inherent to every project. I should have been more clear about the demands imposed on the project:
1) The site sits far from the road and driveway, surrounded by extensive and mature landscaping and on top of a steep ledge. No mechanical excavation is possible and any slab work would require an expensive pump truck.
2) The existing house sits very close to grade and this gable end, where the addition will connect, sits on a rise in the grade. Short of extensive blasting or building a set of interior steps from the kitchen to the new dining room, there is no way to raise the new floor framing.
3) Because of my decades-long professional relationship with this customer, I am trying hard to honor their budget constraints and feelings regarding construction methods. I have conveyed my concerns about this process, building longevity and energy efficiency.
So, with lots of worry, I think I'm moving forward. Scraping all of the limited topsoil from the footprint; Pinning piers to bedrock; Framing floor with PT (the joist box will be framed upside-down with PT ply and hardware cloth then flipped); Maybe closed cell in joist bays; Airtight drywall. Wish me luck.
Thanks again everyone. It helps a lot to bounce these ideas around with people I respect.
Good luck, Ron. Kudos for thinking it through, and doing the best you can for a client you value.
Ron before you leap into CC Foam in your area contact Terry Curtis so she can educate you on some of the issues she is experiencing in your area. I hope she is able to help you since this is one of your close clients your looking out for. Best Regards
Terry Pierson Curtis, Chemical / Environmental Engineer
TP Environmental Consulting & Contracting
PO Box 3845
Brewer, ME 04412
207-991-0171
http://www.gotbadair.com