Alternatives to Exterior Foam

I am building a new house in Vancouver, BC. From what I have been able to determine, exterior foam or rockwool would require an envelope consultant to satisfy inspectors, with numerous costly inspections to the tune of about $3-5K. With fairly significant glazing am I better served to go to triple glazed windows (u=.17) for north facing windows, possibly furr 2×6 walls in with 1.5 ” foam/1/2″ wood to reduce thermal bridging and increase cavity insulation with dense packed cellulose insulation?
I know this is approaching double stud construction but I don’t want to have 12″ thick walls. It would be nice to omit interior wood strips over the foam thermal break but mesh installation and drywall insulation would become problematic.
GBA Detail Library
A collection of one thousand construction details organized by climate and house part
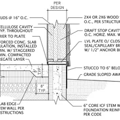
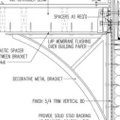
Replies
Paul,
Your question is unclear.
Once you have met code, it's up to you to decide whether you want to spend more for better thermal performance. High-quality triple-glazed windows obviously perform better than double-glazed windows, and high-R-value walls perform better than low-R-value walls.
If you want to analyze the payback of different upgrade measures, we can't do those calculations for you over the internet. Your designer, architect, or energy consultant can help you with those calculations if you don't know how to do them yourself.
我可以看到一层连续的好处sulation on the exterior, I guess it is just a balancing act with the added costs of envelope consultants and construction. Adding foam to the studs and plates internally would help with thermal bridging. How would a 2x6 wall furred in with 1.5" XPS and 1/2" wood strips for a total of 7.5" of dense pack cellulose compare to a 2x6 wall with dense pack cellulose with 2" exterior XPS/EPS?
Paul,
You can add up the R-values yourself.
Dense-packed cellulose is rated at about R-3.7 per inch.
XPS is about R-5 per inch.
EPS varies from about R-3.5 per inch to R-4 per inch.
Your first assembly description is unclear: "a 2x6 wall furred in with 1.5" XPS and 1/2" wood strips for a total of 7.5" of dense pack cellulose" -- but if you are talking about 7.5 inches of cellulose, that's about R-27.5, and if that wall is sheathed with 1.5 inch of XPS, you would get an additional R-7.5, for a total of about R-28.
Your second assembly -- "a 2x6 wall with dense pack cellulose with 2 inches exterior XPS/EPS" -- would have an R-value of about R-27 or R-30, depending on the specs of the foam.
Thanks for quick responses Martin! Let me clarify:
My first assembly is "standard" 2x6 wall, no exterior foam, with strips of 1.5" foam and .5" wood on the inside to give the 7.5" of cellulose and attempt to mitigate thermal bridging.
The second would be continuous 2" exterior foam over 2x6 wall, densepack cellulose .
Paul: I'm thinking of all those strips of 1 1/2" foam and 1/2" wood, and getting tired already. That option sounds like way too much work. Why not just go w/ a double-stud wall w/ a space between the walls (3" ?) just big enough to get the cellulose hose in? Thermal bridging is gone, and cellulose is pretty Earth friendly. In my area, a 2x6 costs more than two 2x4's, and foam is not free. Yes, the windows and doors will not be as simple with a double-stud wall, but there is plenty of info available on how to handle that. BTW: Martin wrote a blog on how to decide how thick your exterior foam should be. In your area, 2" may be a tad light. Just thoughts.