Do I need to insulate our slab?

Building a house with a full basement which will have a walk out on one end. Its being built in Johnson City, TN (east TN) — North Central Region. I have been told that because we are not in an area considered ‘cold’ or ‘extreme’ that it is not necessary to insulate the slab with rigid foam. We will be putting a poly vapor barrier under the slab but wanted your opinion on whether we need to also put down a layer of foam.
GBA Detail Library
A collection of one thousand construction details organized by climate and house part
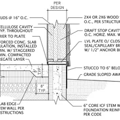
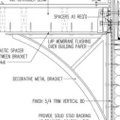
Replies
Don,
At a bare minimum, you should install vertical rigid foam at the perimeter of your slab. The most vulnerable area of your slab is near the door threshold of your walk-out side. With this type of basement slab, it is essential that you have at least 2 or 3 feet of vertical rigid foam to protect your foundation on the walk-out side. On the other three sides, the strips of vertical foam should be at least as wide as the thickness of your slab.
Make that rigid foam at least 2 inches thick.
When it comes to horizontal foam under your slab, you probably don't need it in your climate zone from a heat-loss perspective. However, if you include at least 1 inch of horizontal rigid foam under your slab -- 2 inches is even better -- you will reduce the chance that your slab will be cold enough to encourage condensation. This will mean that your basement stays dry and mold-free, and that you will be able to install carpeting on your slab if you ever want to.
他所说的关于泡沫水平。在你r summertime dew points and regional subsoil temperatures even an inch of EPS (R4) under the slab alone with IRC 2012 code-min or better basement wall insulation for your climate (US zone 4A) goes a long way toward eliminating the "musty basement" smell. If you're going to put down a finish floor with rugs (or stack cardboard boxes on the slab) this is huge. Consider R4 a minimum, not an optimal, but it may be close to optimal if you have very dry soil and your heating energy fuels are cheap.
On a long-term or full lifecycle energy use basis it may still be rational to put down as much as 2" (~R8), but that depends a lot on what your current heating fuel costs are, and what future energy price inflation/deflation ends up being. Splitting the difference at R6 would be a pretty cheap hedge.
The labor cost of installing 1.5- 2" foam is pretty much the same as with 1"- no cost adder there. The additional material cost of going with 1.5-2" instead of just 1" would be another ~20-40 cents per square foot.
The vertical slab-edge foam needs to be R10 minimum, which would be 2.5" if EPS, 2" if XPS. Since the R-value of XPS falls over a handful of decades to that of EPS of equal thickness & density, if you intend the house to be around 50+ years you might as well go with EPS (which is cheaper per R anyway, and uses much more benign blowing agents.)
Code for basement wall-R in zone 4 is also R10 continuous insulation, or R13 between studs. Installing studs up against concrete that can wick ground moisture is a universally bad practice. But trapping 1" EPS against the foundation with a studwall (seams taped, edges sealed with can-foam), and using cheap "contractor roll" kraft-faced (never foil faced) R11s or R13s in the cavities will get you slightly better than code performance cheaply. If you install the wall foam before pouring the slab, making the sub-slab foam continuous with the wall foam thermally breaks the slab edge from the cool soil temps of the sub-grade part of the basement.
For code-R reference:
http://publicecodes.cyberregs.com/icod/irc/2012/icod_irc_2012_11_sec002.htm