Farmhouse heating options

Hello All,
Was hoping to get some input on our dilemma in western MA (climate zone 5). Earlier this year, we bought a 100-year old farmhouse with an ancient oil-fired steam boiler. The boiler failed its combustion safety test during our Mass Save audit, so we really need to remove it.
I would love to avoid as much as possible heating with oil.
We have had a few HVAC contractors come out, and one did a heat load calculation at 93,000 Btu/hr. I hired a HERS rater to do an independent Manual J calculation, and the result was 83,000 Btu/hr. After planned envelope/insulation measures, their “after” calculation was 64,000.
Although I know we need to do work on our envelope, the boiler is just too old and we can’t wait any longer to make this heating decision, we need to replace the heating system now and do weatherization and insulation later. We have a 99,000 Btu wood stove and 4 cords ready to go as backup.
We have been looking at 2 options:
1) Minisplit三菱气候寒冷的热泵系统tem, 2 quotes for 48,000 Btu/hr system.
2) 68,000 Btu/hr Pellet hot water boiler, with bulk pellet delivery (including 5-ton hopper in basement). I love this idea, and MA incentivizes it. However, this would also require retrofitting the entire distribution system from steam to hot water, at an additional cost of $10-12k.
There is a 7-year, 0% heat loan in MA. However, distribution upgrades are not eligible for the heat loan, thus we would need to pay $10-12k out of pocket in the pellet boiler scenario.
We like the idea of the heat pumps, but are concerned that they will not have enough capacity, especially during cold nights. Thus, we have been discussing a new option:
3) 48,000 Btu heat pump system PLUS new oil-fired steam boiler.
This hybrid scenario would cost slightly more than the pellet boiler, but I believe it would all be eligible for the heat loan, with no out-of-pocket costs. We would have a backup source on cold nights, but still would have an incentive to run the heat pumps as much as possible as a primary source. Plus, as an added bonus, the heat pumps would be installed in 2 parts of the house that don’t have steam radiators currently (and where we would need to spend additional out-of-pocket funds for radiators to be installed).
Is option 3 just total overkill? Considering we have the wood stove, should that just be our heat pump back-up?
One final thought: some folks have suggested electric resistance baseboards, as a back-up to the heat pumps during periods of very cold temperatures.
Looking forward to any thoughts on any of the above, or other possible scenarios. Thank you in advance!
GBA Detail Library
A collection of one thousand construction details organized by climate and house part
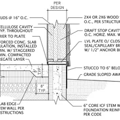
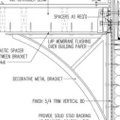
Replies
User-6901443,
First of all, can you tell us your name?
Second, it's always a bad idea to be rushed into a big financial decision because of worries about impending winter weather. If possible, trust your wood stove to keep you warm until Christmas as you make this decision rationally.
An old farm house with a design heating load of 83,000 BTU/h has a lot of problems. It is either very big, or very poorly insulated, or both. Implementing air sealing measures and insulation measures should be a top priority. Get your contractors scheduled for this work now -- or finalize your paperwork with Mass Save as quickly as possible. Weatherization work is your top priority.
It's always possible to design a ductless minisplit solution, or a ducted minisplit solution. If a contractor is proposing 48,000 BTU/h of heat pumps, install another minisplit to bump the heating output a little higher if you want more BTU/h.
My guess is that 48,000 BTU/h of heat pumps, plus a wood stove, is going to get you through the winter just fine. Try out the system for one winter and evaluate its comfort before you worry too much. (You can always plug in one or two cheap electric-resistance heaters in a cold spell if you need to, or just operate the wood stove.)
And schedule that air-sealing work ASAP!
IIRC the 0%/7 year loan for the heating system requires that the system need to be able to meet the design heat load. Relying on the wood stove will not meet their standard (even though it'll meet yours), since it isn't a thermostatically operated system.
Most cold-climate 48KBTU/hr ductless systems have more capacity than 48K at the ~0F outside design temperatures typical of the Connecicut river valley & west, but probably not the full 64K. But it probably won't take more than one or two additional ductless heads to get there.
Are the "...planned envelope/insulation measures..." limited to measures incentivized by MassSave, or are you taking it a bit further?
As I understand it MassSave will rebate air sealing & insulation of the foundation sills & band joists, but not the foundation itself. Whether field-stone or quarried stone it's highly likely that insulating the foundation (even at less than code-minimum R) would bring the whole-house heat load within the capacity of a 4 ton ductless solution (assuming it isn't already there), almost certainly for quite a bit less money than a replacement steam boiler. Since it isn't being rebated, it's out-of-pocket cash, but there are ways to DIY most of it at fairly low cost.
If the concern is only being able to stay warm during Polar Vortex events when the outdoor temperatures dwell well below the 99% outside design temp for days, depending on oversize factor of the individual heads you may be able to shift the available compressor capacity to the rooms that you need fully heated by turning down the set points on the less important zones. And, you always have the wood stove to take the load off the main zone, freeing up compressor capacity for serving the remote zones.
Many people unfamiliar with ductless heat pumps initially experience capacity anxiety, anxiety that leads them to oversizing &/or investing in backup systems that never get used. Most people are pleasantly surprised with just how much capacity these things still have when its in negative double-digits outside.
Martin and Dana,
谢谢你的反应,他们的意图lly help a lot.
The planned improvements include but are above and beyond what Mass Save incentivizes. They probably are worth a post of their own soon! And I am now reading Martin’s June 29 2012 article on insulating basement walls.
Dana, your point about moving capacity from one unit to others where it is needed more is interesting. I will think about that, and might ask the contractors if it even might make sense to re-allocate the capacity a little bit among the interior heads (i.e. re-jigger the ratings a bit) with that in mind.
But you have provided what we need most for now, a little confidence that we are not making a huge mistake if we go with the 48,000 Btu/hr system, provided that we work quickly/in parallel to improve the building envelope.
Thanks again!
p.s. sorry about the name - don't why it didn't pick it up when I first posted, but seems to be fixed now.