如何正确隔离暴露的地板系统?
你好,。我有一个这aproxima添加在我的房子tely 11×14 on piers and 5 ft off the ground over sandy soil and exposed on all sides.It has a 2×8 ,16″ on center floor system framed lengthwise over 2 , triple 2×10 beams, one for each set of piers.The subfloor is 3/4 tongue and groove plywood and i will be installing prefinished 3/4 x 2-1/4 tongue and groove strip oak flooring. I insulated the floor a couple years ago and used 2 layers of owens corning unfaced R-13 in the joist bays and then a layer of 3/4inch polyshield by cellofoam with/metalized poly facer facing towards the interior , fastened to the bottom of the joists and then a layer of 1/2 osb over that to keep rodents out.When i pulled the existing carpet up to redo the floor i made a couple access hole to inspect the cavity and found signs of frost and condensation on the foam insulation but only certain areas, closer to where the addition is attached to the house.My questions are how do i avoid this?…The oak flooring manufacturer recommends 15lb. felt under their floor and im concerned i might make the situation worse because of possibly trapping the moisture in and slowing or stopping the drying to either side and causing structural damage and mold.Should i remove the foam and reinstall the osb alone to cover the unfaced fiberglass,then use the 15lb.felt under the oak as a vapor retarder and allow any moisture to dry to the outside ?Or should u add more foam to the existing foam on the bottom to isolate the floor system more from the cold?Or should i pull all the fiberglass down and foam and osb and install/friction fit 2 inches of some type of rigid insulation to the bottom of the subfloor and sill area where the addition attaches to the house and use that as the vapor retarder and then the 2 layers of unfaced fiberglass and cover that with the osb??…Also the existing poly foam on the bottom of the joists runs between the triple 2×10 support beams i previously mentioned and was wondering if that might be contributing to the condensation allowing air to seep into the floor cavity and if the top of the beams should be covered with foam , overlaping onto the existing foamboard,…any advice and info would be greatly appreciated,..thank you
GBA Detail Library
由气候和房屋部件组织的一千个建筑细节的集合
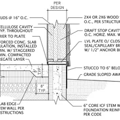
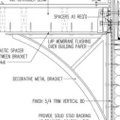
Replies
这个位于哪里?
我在纽约市中心..我忘了包括这一点
I'm going to guess the your foam isn't thick enough (it should either be omitted or made much thicker), and/or that there are air leakage issues from the interior. Do you have forced air heat, and is it possibly pressurizing the house slightly? Are the signs of moisture around the perimeter?
Mike,
大卫的建议是有道理的。这是空中密封问题,或者家庭正在加压。无论如何,凝结可能是季节性现象,并且随着天气变化,水分会无害地干燥。(地板系统由于室外温度波动而产生一些空气交换。)
更多信息在这里:如何绝缘寒冷的地板。
i dont have forced air, i have hot water baseboard,..i think i have air leakage on the sill/rim joist from where the addition is attached to the house where the warm air from the basement is/can enter the floor system,... the moisture does seem to be more in that area and i was considering installing rigid foam against it on the addition side.You mentioned adding more foam, i have 3/4 on there now.. would 2 inch be enough and if so what would u recommend?If i ad more foam should i also put the foam over the top of the support beams bridging the 2 foamed areas to have no breaks in the foam layer??i included a picture of the beam...Also if i do go with the extra foam can i still use the 15-30lb felt under the new oak flooring im going to install or will that trap any vapor in the floor system??..the other option u mentioned was to remove the foam which i also thought about but do i just leave the 2 layers of unfaced R13 insulation in the cavity and reinstall the osb underneath then use the 15-30lb vapor barrier under the strip oak flooring and let the floor breath outward,..or should i use the 2 inch rigid foam against the bottom of the subfloor with the unfaced fiberglass under that and then the osb to seal out rodents etc?..and if the 2 inch is used under the subfloor would that eliminate the need for the tarpaper for the oak flooring?,...very frustrated ,..lol
刚看到最后的回复,谢谢大卫和马丁的回应...我不确定空气密封问题的意思。你的意思是寒冷还是温暖的地板?我确实用Caulkover将周边密封了屁股屁股到周边然后钉了1x1,但我没有密封光束区域并怀疑冷空气泄漏?也许我应该用泡沫漂浮在梁之间的现有泡沫上面?
Mike,
当您在热封的寒冷区域进行冬季冷凝时,水分源通常是内部空气,而不是外部空气。(外部空气干燥;内部空气潮湿。)
它不太可能,但有可能有一条暖,潮湿,内部空气到达冷刚性泡沫。然而,堆叠效果通常会阻止这种漏气。
在你打开地板之前,甚至可能没有冷凝。一旦你打开地板,内部空气就可以进入冷泡沫(第一次)。
你可能会过度思考这个。我会放松一下。在您的新橡木地板下,请将松香纸或沥青放入。(有些人更喜欢松香纸到沥青,因为它们担心沥青气味。但是,只要您在地板系统中没有卫生管,我就会使用任何一个而不担心。)
马丁,......我确实在角落里有一些管道。你的意思是透水地板加热系统或管道喂养底板?。我在地板的一个角落里重新排出了大约1/2铜,但它的墙壁在底层,大约4英尺的总数,我把它包裹在那个黑色的聚苯乙烯泡沫塑料管包裹底板上,......以前在地板上发现了水分,。我想到了你的概念在暖空气中达到了概念泡沫一旦敞开地板,但我不这么认为就是这样,因为我一旦打开它,我就达到了泡沫和毛霜......地板制造商建议毛毡,......我总是使用松香......如果我用觉得我应该从下面取下泡沫,然后我仍然可以选择2英寸刚性泡沫(没有箔面积)在下面的玻璃纤维下,因为我之前提到的玻璃纤维或者我可能是风险腐烂3 /4底底泡沫夹在泡沫和毛毡之间,感觉到......和是的,我已经过度思考它,......哈哈,你告诉?
Mike,
沥青毛毡没有水分问题 - 如果它过热,才能享受(潜在的)气味问题。
Don't worry.
I would leave the rigid foam in place and stop worrying. It wouldn't hurt to install more rigid foam from below, as David suggested.
ok, so i think ill use felt,..the floor warranty requires it,..and leave the foam on the bottom and add to it,..would u recommend over the beams and against the sill also ???..the top of the beam felt moist/damp .....and if i decide to take everything out and go with the 2 inch foam up under the subfloor ,friction fit and the fiberglass under that with just the osb closing that in will that be ok if i have the tarpaper under the oak??..will the tar paper be safe to use with both options,.and if you had to choose, which would you advise as the better option???...........again thank your very much for your advice/expertise and time and patience
是的,不,..也许?。哈哈
迈克,不亲自检查,很难提供详细的建议。作为一般规则,您需要定位并密封任何空气泄漏部位,其中潮湿的空气(可能是从内部)泄漏到绝缘地板中并找到冷,冷凝表面。你需要使用足够厚的泡沫,使内表面不会变冷,足以冷凝。无论您身在何处,您都应该连续地保持绝缘,而不是用框架中断它。这是一般的图片,细节取决于把手放在工作中并弄清楚问题。
The felt under the flooring is a non-issue. Assuming no radiant tubing in the floor, or other source of heat that will bake it, install the felt. I put felt under my wood floors and have done it on many jobs for others over the years.
david,..thanks again,..ill use the felt under the oak,...and eliminate any warm air entering the floor and add more foam underneath or apply the other concept of foam under the subfloor ,unfaced fiberglass below that and the osb,..........again thanks for all your help and advise
迈克先生,我不确定是否有人建议它,但是你可能有一个冰冷的三重2x10,没有帮助问题。它的方式不仅仅是一个热桥,就是它的两个大表面区域一英寸左右的温暖托腔。。我不能告诉你的照片,如果冷凝在这个girder的区域。我确定梁周围的漏洞也非常慷慨。
I would have to believe that the triple should be wrapped in foam very well
丹尼斯,…嗨,. .是的梁/ gir顶部的中心der in the pic felt damp and smells musty and i can see some tiny black spots,..maybe mold starting??.. i asked about possibly covering them from the inside and overlaping onto the existing foam with some 2 inch foam.....but I wouldnt be able to do anything to the area where the joists rest on the beam .. unless i wrap the beam as you suggested..which would look like hell unless i cover that with some pine or something but might be the best solution,..............i suspect that that area might still have air leakage/condensation issues even after i do my best to stop them by adding foam at the interior sill area, over the beams and whole bottom surface,.......thats why i brought up possibly putting the foam up under the subfloor ,an unbroken run down the whole joist bay,and then the unfaced batt insulation, then the osb with the hopes of any possible condensation having the ability to dry outward through the osb................
嘿mr.mike,当你在线程中描述了这个想法时,我错过了。它的声音很好。我用兴趣阅读你的问题,因为它是一个常见的成绩来构建像你一样的房间或有一个门廊标题生活空间下面。我想知道马丁的建议是从能源效率的角度来从划痕建立它。
迈克,这是一个有趣的写作,这提到了在你的情况下绝缘地板。
http://www.buildingscience.com/documents/insights/bsi-064-bobby-darin-thermal-performance?searchterm=insulation + interloor.
丹尼斯,......你的意思是泡沫下的泡沫的概念,就像它一样好起来?.....我没有框架,但如果我能拥有,我可能会以不同的方式诬陷地板,也许是2x10或2x12'坐在轴承墙壁下的梁宽度明智地在地板系统中覆盖它们,使得我也可以覆盖整个底面,而无需解决暴露的光束......我不知道那是马丁是否会做什么......但谢谢你今晚的链接检查出来
Mike,
我同意你的观点。有两种类型的光束。您的光束从下面支撑托梁,托梁的底部搁置在光束的顶部。
A flush beam, on the other hand, supports the joists with joist hangers. If you had installed a flush beam, it would have been easier to install a continuous layer of rigid foam on the underside of your floor system.
丹尼斯,
我很高兴你带来了那篇建筑科学文章。我要问那个,但我担心它已经关闭了主题。
I do not understand the concept of including an airspace above the cavity insulation. Everywhere we hear to not leave an airspace around the insulation and here Dr. Lstibirek says in this situation to leave an airspace on underneath the subfloor and the floor will be warmer?
I don't really understand the mechanism for that. The house we will be building soon will be built on piers and I really intend for it to be energy efficient, so if someone could explain this to me I would appreciate it.
露西,
如果您想使用LSTIBUREK的方法,有三个要点
1. The reason that his approach works is that the layer of warm air keeps the tops of the joists warmer and therefore reduces thermal bridging somewhat and reduces the "cold stripe" phenomenon.
2.随着LSTIBUREK在他的文章中指出,“空域可以为一个暖地板填满。完全填充空间[用绝缘材料]减少热流并节省能量,但不会使地板温暖。”因此,在两种不同的目标节省能量和保持地板温暖之间存在稍微紧张。
3. Lstiburek的方法 - 留在绝缘层顶部和底层之间的空间 - 如果您是具有平均技能的建筑商,则是危险的,因为地板组件中的空气泄漏常规允许冷外部空气渗透托卧系。一旦发生这种情况,这种细节就是一场灾难。如果Builder具有无可挑剔的空气密封技能,则该细节仅适用。这很罕见,但可能。
这是底线:在该组件中做大部分工作的绝缘是托梁下方的连续刚性泡沫层。如果您想要一个较温暖的楼层,请牛肉上升刚性泡沫的厚度 - 并在地板组件(边缘托梁区域)的周边处进行空气密封的无可挑剔的工作。那么这几乎不如你在地板托梁之间放的蓬松的东西。你可以用一点(lstiburek方法)或很多(我的方式)。
Finally, that makes sense. Thank you, Martin.
马丁,乔说:“我们从老家人那里学到了这一点”。他的观点似乎是这种绝缘地板的方式是加拿大的传统方式,他来自哪里,并且总是很好地努力预先预期Framers携带罐头罐和泡沫,并且可能泡沫板也可以打赌空气密封真的有助于,但即使在过去的过去,它也可能不是灾难。