Insulation for an unvented cathedral ceiling in Zone 4

We are building a a “pretty good” house in southern Virginia. We are using local contractors and trying to keep things within their comfort zone. For this reason, we avoided exterior foam insulation and laid out the house so as to make the details of the air barrier simple.
The house has a 32 X 48 footprint with a cathedral ceiling running the whole length. The roof will built with parallel-chord trusses ($7k worth!), as shown in the last page of the dwgs attached.
Our insulation contractor suggests insulation with open-cell foam – about 10″. This would work as our air barrier, but according to Martin Holladay’s article on cathedral ceilings it would not achieve a vapor seal. Our contractor, on the other hand, argues that it is wise to let the roof decking drain to the inside so that you detect a roof leak before it ruins the decking.
Our questions are:
1) Should we insist on a layer of closed-cell foam against the roof decking as a humidity barrier?
2)如果我们确保我们有足够的泡沫under the decking (i.e., 31% of the total R-value of the roof, per another Martin article), would it be wise to fill the rest of the truss with fluffy insulation? (It seems a shame to waste the big void; we could have, say, 8″ of closed and open foam plus 16″ of fluffy insulation below it.)
3) Would choosing Zip roof decking (instead of OSB) help to achieve a better air barrier or humidity barrier?
4) As always, suggestions are welcome – please do answer the questions we should have asked but didn’t think of.
GBA Detail Library
A collection of one thousand construction details organized by climate and house part
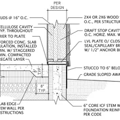
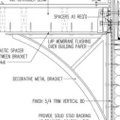
Replies
>...insulation contractor suggests insulation with open-cell foam – about 10″
At 10" most half pound open cell foam is less than 5 perms (middle of Class-III vapor retardency) and about R35-R38. IRC code minimum in zone 4A is R49, which would take about 13-14" of open cell foam, or 7-8" of closed cell.
At 14" most open cell foam, and would be less than 3 perms. That may be enough to protect the roof deck from excessive wintertime moisture accumulation, but could be prone to daily cycling of moisture in/out of the foam as the roof temperature changes in summer, causing high peak humidity events in the attic.
With R15 of closed cell against the roof deck you'd have sufficient dew point control for up to R35 of fluff or open cell foam without wintertime moisture accumulation at the boundary between the two insulation types. If you go deeper with the fiber or open cell foam R, you have to go proportionally deeper with the closed cell.
At 8" of HFO blown closed cell you'd already be above code minimum, and the marginal improvement of filling the rest with blown fiber or open cell foam would be hard to measure, and probably not financially rational. An R45 "whole roof" (thermal bridging factored in, not center cavity R) is about the limit of financial rationality, and with 8" of expensive closed cell foam on a trussed roof you're already over that. Just 7" of HFO blown closed cell would run north of $10 per square foot in my neighborhood. Using 8" of climate damaging HFC blown closed cell would run $8 per square foot, and would have to be installed in four lifts with a curing time between them. (HFO blown foam can be installed at R49 in a single pass from some vendors, but not HFC blown foam.)
To get the full 24" deep cavity fill at lowest cost/least damage with reasonable dew point control you'd need 5" of HFO blown closed cell foam (R33-R34-ish) and 19" of 1 lb density blown fiberglass ( R70) and you'd be above R100. Maybe bragging rights are worth something to you, but from an energy use or comfort point of view an R100+ "compact roof" is a bit ridiculous. I'm sure you can hit PassiveHouse levels of energy use with less roof R than that.
Price it out, but I suspect 3" of closed cell (any type) + 9-10" of half pound open cell is cheaper than 8" of closed cell foam, and beats code min with margin. In my area every inch of HFC blown (climate damaging) closed cell costs 3x that of open cell, and every inch of HFO blown closed cell costs about 4x as much. And no matter what the blowing agent is, every inch of closed cell uses 4x as much polymer, but is less than 2x the R.
Taking it a step further, with the lower thermal bridging of trusses when the top chords are completely encapsulated in foam you can still hit code minimum performance on a U-factor basis with just 2" of HFO blown closed cell (~R14) plus 8" of half pound open cell foam (~R29-R30) for R43-R44-ish at center cavity, even though it's a few-R shy of code min R49 at center cavity. That's still a decent performing roof in zone 4A. In my area 2" of HFO blown closed cell costs $2.50-3.00 per square foot, and the additional 8" of open cell would add another $2.25-2.75 or so- you'd be under $6 per square foot. That's still quite a bit more expensive than the contractors' recommended 10" of open cell (and still a bit higher performance), but a lot cheaper than most of the other options, and there is minimal risk of summertime humidity cycling in the attic.
There doesn't appear to be any real basis to the roof leak detection issue with closed cell vs. open cell foam. If roof leaks are a concern that would keep you up at night, a full layer of Grace Ice & Water Shield above the roof deck creates a fully adhered, self-healing membrane that re-seals around any fastener penetration. The shingles could blow away in a hurricane an the roof (if it was still there) wouldn't leak. With only 2" of closed cell and 8" of open cell the roof deck can still dry seasonally toward the interior through the ~0.5 perm vapor permeance of the stackup.
谢谢你,达娜。深入分析,包括成本data. ;-)
We're trying to keep it simple, so I like your proposal to do 2" of closed cell, then add open cell until we get the R-value we want.