Marine Zone 4C exterior foam choice

I am planning to install 1 inch of rigid foam over the Tyvek DrainWrap of my 2×6 framed home in Marine Zone 4c.
After reading hundreds of articles here over the last few months I am still slightly confused about the minimum thickness of foam allowed in my area. Seems like a still debated topic and that is OK.
如果我go with 1 inch EPS its pretty cheap and I am right at the lower limit of what the table suggests is the minimum for my area. Table says r-3.75 and I’ve read here that EPS is R-3.6 per inch.
Second option would be to use 1 inch XPS and get well over what the table suggests. Problem here is the lower perm rating, extra cost, and bad environmental impact of the product itself.
So what is the better choice when taking all the factors into account? I am really only after a thermal break as my climate is really quite mild.
I have asked versions of this same question here before. Thanks for revisiting it again with me.
thanks
GBA Detail Library
A collection of one thousand construction details organized by climate and house part
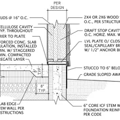
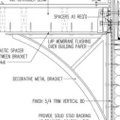
Replies
Hi Joe,
I suspect that the table you are referring to is R702.7.1 in the International Residential Code (IRC). Keep in mind that that table isn't about minimizing thermal bridging, or even energy efficiency, it's about vapor control (it's in the section of the code on vapor retarders).
The chart says that if you hit a particular R-value with your continuous exterior insulation, you can use a class III vapor retarder inside (painted drywall). The idea is that you have enough R-value outside of the sheathing to keep it warm and prevent condensation from occuring in the wall. However, because the thicker insulation may prevent outward drying (depending on the type and thickness) the more vapor open interior wall covering will maximize inward drying potential, should the wall get wet.
Said another way, you don't have to hit that minimum, but if you choose not to, you are required to have a class II or class III vapor retarder on the inside of your wall (at least as far as the IRC is concerned).
Here are a few key things to remember:
Minimums are minimums: Most high-performance homes are insulated well beyond IRC minimums both for vapor control and for thermal control.
Walls get wet in a few different ways. To keep rain and snow melt out, your water-resistive barrier, window and door flashing, and other water management strategies are super important. Pay close attention to the details when installing them.
To keep water vapor out, air sealing is key. Experts will tell you that much more water vapor gets into walls through air leaks than diffusion. Make sure your wall cavities are air-tight on all six sides.
>"I’ve read here that EPS is R-3.6 per inch."
Where did you read that?
Even cheap 1lb per cubic foot Type-I EPS available at box stores is R3.9/inch (and thus exceeds the absolute code prescripive minimum, but not by much.) Type VIII EPS (1.25 lbs density) is about R4.15/inch, and Type-II (1.5lbs) is R4.2/inch.
When it's on the exterior of sheathing it's legitimate to use the ASTM C518 performance at 40F rather than the nominal 75F performance required for labeling. Most manufacturers publish the peformance a both 40F and 75F, many will also include the performance at 25F, but that would not be legit for dew point control purposes in a 4C climate.
eg: Type I R-tech(sold in box stores) is
R3.85/inch @ 75F (mean temp through the foam layer)
R4.17/inch @ 40F
R4.35/inch @ 25F
https://www.insulfoam.com/wp-content/uploads/2014/04/12015-R-Tech-Wall-TDS_WEB_REV8-16.pdf
>"Second option would be to use 1 inch XPS and get well over what the table suggests."
Don't get too far ahead of yourself here. The additional labeled performance of XPS over Type-II EPS is temporary, a characteristic of it's climate-damaging HFC blowing agents. While it's labeled R5/inch, the manufacturers only warrantee R4.5/inch, and at full depletion of the HFCs (after several decades) doing it's environmental damage it settles in at R4.2/inch. From a dew point contol design point of view it's only legitimate to use the warranteed value, but to be conservative it makes sense to use the fully depleted value. Mind you, at 40F mean temp through the foam Type-II EPS is usually R4.5/inch, the same as the warranteed performance at 75F.
还要注意,irc prescriptives 2 x6墙re predicated on R20 as the cavity fill. If installing dense-packed fiberglass or R23 rock wool instead of R20 the prescriptive needs to be bumped proportionally.. For R23 that would be R3.75 x R23/R20= R4.3.
T0 max out the performance of an inch of foam with less environmental damage, use foil faced polyisocyanurate, and give a bit of air gap between the siding and the shiny foil. Both EPS and polyiso are blown with hydrocarbons at about 1/200 the impact of the stuff used for XPS. The R-value of the polyiso itself is about R6, but a bright foil facing an air gap will add another R1 to the average performance. Even 3/4" foil faced polyiso would usually be labeled R5 (without the gap) and about R6 with the foil and air gap factored in, which offers some margin over EPS/XPS with no gap. Foil facers are also comparatively easy to air seal using a temperature rated foil HVAC tape (Nashua 324A or similar, not cheap unrated decorator foil tape.)
谢谢你的回复,
Dana- I am still am unclear about when to be concerned about vapor permeance. Foil face offers none.......this is OK?