Should wall sheathing connect to mud sill?

How important is it to have your wall sheathing overlap your rim joist/board and connect to mud sill?
I will be building in northern New England. (Little in the way of seismic/ hurricanes)
Thank you!
GBA Detail Library
A collection of one thousand construction details organized by climate and house part
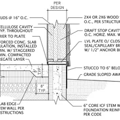
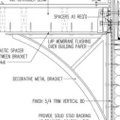
Replies
瑞克,
每一个房子我曾经陷害过墙剪切hing that connected to the mud sill.
My first question is: Why can't you do it the normal way?
If for some reason you can't fasten your wall sheathing to the mud sill, the best person to answer your question would be an engineer. (You may be able to solve your problem with diagonal steel strapping -- but you'd need to have your solution checked by an engineer.)
Here is a link to an article that may provide you with relevant information:Four Options for Shear Bracing Foam-Sheathed Walls.
瑞克,
For a few years around the 1990s builders were urged not to connect the wall sheathing with the rim joist and mud sill, the idea being that shrinkage of the joist and plates meant that the sheathing could end up taking the vertical loads. Instead a separate piece of sheathing was applied that just lapped the rim joist and sill. Framers liked it because it made sheathing and standing walls on the floor deck easier. Some production builders went a step further and eliminated the sheathing at the floor level altogether, setting the walls in so the sheathing was flush with the floor framing.
The practice has fallen out of favour, but outside of high wind or seismic zones I can't see any problem with using a separate piece of sheathing to lap the floor framing and sills.
Malcolm,
Good point about walls that are raised with the sheathing on them -- I knew about that technique, even though I never used it. I guess that in most regions of North America, there isn't any structural reason for wall sheathing to extend down to the mudsill.
Thank you Martin, Malcolm;
I'v seen a handful of homes here in NH where the sheathing doesn't meet the mud sill. The wall sheathing is simply flush with the rim board.
It doesn't seem that simply toe-nailing the studs to the subfloor/ rim board would be sufficient for shear strength. Yet, I haven't noticed any houses sliding off their foundation either.
I was just curious how much strength I would actually be losing if I buried the rim joist under rigid foam
Thanks again
瑞克, The question is how much strength do you need? I think Martin's advise in post 3 is bad Remember it was free. In post #1 it was good. Malcom is right on. Hire an engineer or a local contractor. Here is how it should be donehttps://www.apawood.org/wall-bracing
Thank you Tim!
Your proposed detail would fail to pass inspection in California. Sheathing should absolutely be connected mechanically to the plate for both shear and uplift. It is the plate after all that is bolted to the foundation, and if you rely on nailed studs to hold the house down, you risk it not being held down during extreme weather events. No earthquakes or hurricanes? How about tornados and straight-line winds? Perhaps revisit the reasons that drive resilient building practices.
I urge you to pay a fee to an engineer if you want to diverge from standard building practices that are structural. Otherwise, you are making assumptions.
My mud sill and rim joist do not meet squarely. My mud sill has about. 5" that sticks out beyond the band joist all around the home. My contractor asked if I wanted to just nail the ZIP sheathing to the band joist and leave the mud plate covered behind the upcoming vinyl siding. I feel that leaves it less protected from water and insects.
I am going to propose he uses .25 or .5" plywood to furr out the 2x8 band joist so that it meets the mud sill more accurately. Has anyone done this?
Jacob,
Won't furring out y0ur rim-joist put them out of alignment with the walls above? If you haven't framed the walls above, and the change in dimensions won't affect anything (trusses, etc.), then go ahead and sheath the rim as you propose. Otherwise tell your contractor to get out his reciprocating saw and trim down the sill-plates. The problem should have been corrected before the floor was put on.