Stick build vs modular addition

So I have been reading that factory built homes have come a long way in terms of building science and they have become very efficient. Supposedly money saving. I’m sure this is case specific, and opinionated but when attaching to the side of an old home is it a bad idea. Is stick building the same cost or cheaper. I know this is a site of builders so I don’t know if factory building is hurting the industry or jobs I’m not in this field to know. So any merit to prefab, my thought is quick, easy for logistics, less complicated for home owner. Seems more turn key and predictable than remodeling, opinions are welcome.
GBA Detail Library
A collection of one thousand construction details organized by climate and house part
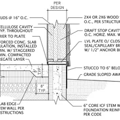
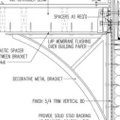
Replies
I can see how modular would be fast and ease on a new flat and square foundation bolting to other nice square modules.
In my opinion making a new flat square foundation abutting an old wall that is not likely to be straight or plum will be no small feat. Now you set your module down what are the chances it buts up against the old wall perfectly all the way down the wall. With stick built your carpenter and fudge each board you will never notice is not square or plum.
Walta
There are a lot of bad 'rules of thumb' when it comes to why prefab is good or bad, here is mine after pricing out a couple. Note - I have never actually gone to contract on one because I could never make the numbers work (primarily because the projects were one offs and had particular custom features not suitable for prefab).
My rule of thumb: stick building will be cheaper than prefab for anything with 'custom' attributes beyond vinyl siding color, etc. The modules we ended up getting priced were missing a ton of finish work because it couldn't be shipped due to damage/weight considerations. We also couldn't meet any purchasing or design economies of scale, and nothing the clients wanted were in the typical buying package the factory used (this is east coast with a couple 'market rate' prefab companies, not high-end stuff).
I've had better luck with prefab panels and, of course, prefab trusses are industry standard at this point. Prefab can reduce cycle time and reduce weather impacts, but I haven't found a huge cost advantage.