Wall Design Questions

I am planning on building a new house inland a bit from midcoast Maine (Zone 6) and have been pondering issues related to exterior wall design, taking into account what I have read here and elsewhere. I want a relatively high-R wall (~mid R-30’s) and have been thinking about the following designs.
Design 1: 2×6 wall with ½” drywall, R-23 Roxul, OSB/plywood, 2-3” Roxul Comfortboard, rainscreen (e.g., 1×3 strapping), siding.
Design 2: 2×6 wall with ½” drywall, 2” Roxul Comfortboard (inside the studs), R-23 Roxul (between studs), OSB/plywood, rainscreen, siding.
Design 3: 2×8 wall (overall) consisting of (2) 2×4 walls offset from one another, ½” drywall, R-15 Roxul between studs of inner 2×4 wall, 1” Roxul Comfortboard “between” the 2×4 walls, R-15 Roxul between studs of outer 2×4 wall, OSB/plywood, rainscreen, siding. I ‘cheated’ a little here, assuming ~8” of mineral wool can be compressed into the 7-1/2” cavity.
In terms of R-values, the designs provide (based on R-4 per inch of mineral wool): R-31-35 (depending upon how much exterior comfortboard is applied), R-31, and R-34 (if compressing mineral wool a bit doesn’t significantly compromise R-value).
设计1会有点短的OSB/plywood protection for Zone 6 if only 2” of Comfortboard was used but I wonder if this would be “OK” insofar as the mineral wool should allow the sheathing to dry more readily than rigid foam. If this is ‘risky’ even with the better drainage capability of the wool then 3” would be applied. It seems to me that use of mineral wool on the exterior might be a better way to go from an R-value as well, given recent discussions about cold-weather performance of rigid foams (esp. polyiso).
Design 2 brings the protection from thermal bridging inside the house (reducing interior square footage a bit) but alleviates the need for exterior insulation (including the need to add enough insulation to keep the sheathing dry). The R value suffers a bit relative to the other designs, although this could be worked a bit by substituting rigid foam (R-5+) for the Comfortboard.
Design 3 incorporates protection against thermal bridging into the interior of the wall and has a higher R-value than design 2. It encroaches upon the interior square footage to the same degree as the second design and also alleviates the need for exterior insulation (including the need to add enough insulation to keep the sheathing dry). Although the first 2 designs are probably similar in terms of cost, this option would be more expensive (although I don’t know by how much).
Input on the merits (or lack thereof) of the three designs would be greatly appreciated. Is there a “best” design of the three?
GBA Detail Library
A collection of one thousand construction details organized by climate and house part
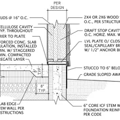
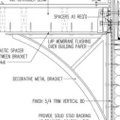
Replies
Rob,
我住在区域3,SC北部。我们建立了exactly the same wall you describe in design #2. My reasons for using Comfortboard exterior to the siding was to reduce thermal bridging, but I also like it's resistance to fire and insects specifically carpenter ants, termites. We live in a very "buggy" area of the country.
We used Roxul Rockboard 80 because I could get it so much easier than special ordering it from the large home improvement stores. That may not be the case for you in Maine.
I don't know which one is the most efficient to build, most cost effective or risky in terms of moisture in the sheathing. I'm sure you will hear from the builders and engineers on this site about those issues. But I can tell you it is a pain to wrap your house in mineral wool. I call it a "cozy mineral wool sweater" and I would do it again, but there are a lot of issues that most builders (in the South anyway) are not familiar with when you do that. We worked through the issues, but it was very time-consuming.
It's still the method I would choose again, but really think through the details first before you do so. Also, calculate how much each method would cost. After looking into sheathing issues, I would always choose plywood since it is able to absorb and release moisture so much better than OSB.
Here's a link to my blog on that exterior mineral wool.http://greenvillegreen.blogspot.com/2013/10/cozy-mineral-wool-sweater-on-house.html
And I have included a different photo on our mineral wool sweater. We decided to use 2" foam around the windows so we could tape to them easier and make sure it is airtight.
One GBA reader blogs at "A Green Hearth" has a good post on flashing around windows with exterior mineral woolhttp://agreenhearth.com/our-lessons-in-window-flashing/
Lucy, your post is informative. Very useful to those of us who have not used Rockboard yet but may some day.
Lucy,
Thanks for the information. It appears your design is most like my first design, given that my second design places the wool on the interior side of the house (that may not have been clear in my original post). The pictures and discussion about how best to 'trim' out windows (i.e., foam vs wool) are good to have.
None of your wall stackups break R30 whole-wall after the thermal bridging is factored in.
#1: 2x6 24" o.c. R23 cavity fill wall with 3" of exterior ComfortBoard comes in at about R29. (With only 2" of rigid it's runs R25-ish. With 16" o.c. spacing it's less.)
#2: Putting the rigid insulation on the interior side is even worse, since it doesn't thermally break the band joists & subfloor.
#3 Is also in the low-R20s whole-wall due to the thermal bridging and lack of break at the subfloor.
As a crude way to add it up use these rough-figures:
The siding + sheathing + gypsum combined add up to about R1.
R15 Roxul between 2x4s at a 20% framing fraction (24" o.c.) is about R9.6 after thermal bridging. For 16" o.c. spacing it's a ~25% framing fraction, and about R8.9.
R23 Roxul between 2x6 comes in at R13.9 at a 25% framing fraction (16" o.c. spacing), and R15.0 at a 20% framing fraction (24" o.c spacing.)
Design #1 is both the easiest to build, and has highest whole-wall R, and as long as you have 3" of exterior insulation you can skip the interior vapor retarders. (R1 siding/sheathing/gypsum + R15 2x6 wall + R12 rigid continuous insulation = R28.)
A higher-R variation of #3 would be to use 2x4 16" o.c. for the structural wall, and finger-jointed 2x3s 24" o.c. on the interior side wall, with 2" of rigid (either ComfortBoard or EPS, which is cheaper) in the gap between the studwalls. That doesn't solve the thermal bridging at the bottom plate, but you end up with R1 (siding/sheathing/gypsum) + R8.9 (2x4 wall), +R8 (rigid) + R6.8 (2x3 24" o.c. with compressed split R23s as cavity fill) for about R25 whole-wall. That's a whole lot of extra cutting trimming and fitting of both lumber an insulation to get right than Design #`1 (that outperforms it by 12%, using less material.)
Dana,
Thanks for the input. My R-values were (obviously) not stated in terms of whole wall values. Restating them in terms of whole wall values highlights a weakness of "interior insulation", the lack of thermal bridging/break at the subfloor. I was thinking about designs 2 and 3 as a way to get a high R wall while minimizing the thickness of the wall from the OSB/plywood out. Performance and ease of construction suggests I should get over that and use the first design.
Rob,
I have also been considering your design 3 option for my build. I live in Ottawa which often sees -20c through the winter. My wall section would consist of:
siding
house wrap (breathable drainage plane)
3/8 plywood
2x4 stud wall 16 oc with roxul batt. Framed to underside of floor decking.
1"-1-1/2" extruded styro with ship lap joints taped. Again to underside of floor decking. This will be my vapour barrier and thermal break.
2x4 stud wall 24" oc less joist height to support floor and run electrical. Will also insulate with fibreglass batt.
drywall and paint.
Note that I realize that the rule of thumb is 2/3 of the insulation should be to the cold side of the vapour barrier, and this design is close. I could easily achieve it by opting for 2x6 exterior, increased styro, or decreased batt to the inside. however I'm not to concerned as the design allows for drying to the warm side if or when condensation occurs.
My reasons for considering this design are:
-I will have quite a bit of exterior detail and I don't want the hassle of working over top and around insulation.
-I don't like the idea of a vapour barrier on the cold side of my wall for obvious moisture issues.
-I know that a continuous vapour barrier to the inside of a wall is virtually impossible after all the mechanical and fastening penetrations
-I like the fact that this design can dry to both the inside and outside.
With all the benefits that I see with this design I wonder why I can't find more about it. Is there something that I'm missing??? I realize that framing a second wall is more work but after factoring in the fact that you would have to strap over the entire outside of the house for something to fasten siding to (unless you plan to brick or stuco) I don't see that a second wall to the interior as such a big deal. In my opinion as a framer building walls is the fun part! If you have ever strapped and sided over styro you know that it's a pain in the a...
Maybe it's the r value that people are hung up on? But I would suggest that r means nothing if your walls leak... and something that I have encountered with these super tight wall systems is that the less leaks you have the greater concern they become. You can end up with a really high concentration of condensation where you have a small leak and most of these designs don't allow for the wall to dry in or out.
Does anyone have first hand knowledge of this design? or see an obvious flaw in my reasoning that I could be missing?
Rob,
I would like to point out that you have outlined two very different walls.
Walls 1 & 2 are 2" x 6" structural walls with mineral wool inside them. One has some more mineral wool on the outside, the other has it on the inside. They both have pros/cons, which I think you understand.
The main difference is that the exterior mineral wool requires non-standard detailing for windows/doors, but provides a real thermal break, potentially covering your rim joist area & above grade foundation walls too.
Wall 3 is a double stud wall. With this comes a new set of details you must "get right".
1)两堵墙的结构,和this fact must be clear to your inspector. Presumably, it will be your exterior wall, but this must be explicit in your designs. Load paths cannot be ambiguous.
2) Where before you might have been able to use extension jambs for your windows & doors, you are now into window bucks. To be fair, you will likely need window bucks with 3" exterior mineral wool, too.
3) You proposed 2 - 2" x 4" walls with a 1/2" gap. This totals 3.5" + 3.5" + 1/2" = 7.5". If you can, consider increasing the gap, up to +3" so you can fit another R14 batt between the walls. Or at least, bump it up more than 1/2".
This gap and it's ability to be customized is one of the main virtues of a double stud wall system. You're already dealing with window bucks, for example, so making them 7.5" or 10.5" deep is a negligible difference.
Hope this helps make your choices and what is involved clearer.
Cheers.
Kevin,
It sounds like your wall will work. To many builders, your approach will probably seem more complicated than installing exterior rigid foam. But it's your house, so you should build the wall you feel comfortable with.