Venting, Air Sealing, and Insulating Attic in 1904 Victorian

I’m remodeling our attic space (which was already finished poorly) and am stuck on the details for air sealing, venting and insulating this space. With all the methods and products it’s confusing to come up with one design approach to Make this space efficient, but also to do it in a manner that I don’t create other problems (ie trapping moisture etc), and to do it on a limited budget.
the roof is in fairly good shape, so I’m not planning to do anything with the surface. So all work has to be done underside. It’s currently gutted and I’ve removed the existing unfaced insulation and the Fire blocking from atop the short wall sections on either side, to allow air to move from the soffit up through the rafter bays and out through the ridge. The roof does have a ridge vent – which was useless by the way – because of the fireblocking.
I was planning to cut in soffit vents the entire length on both sides – later probably in the spring – as I won’t have time to get to it this winter
至于绝缘,我希望创建一个channel for the air below the roof deck, possibly by constructing the channel with 1” ridgid insulation, and then faced batt insulation over that. I could also use the panels for venting made for this purpose, but with the rafters bays being Inconsistent sizes at 16, 17, and 18”, I thought making my own might be a better solution? Strapping and then drywall. I’m not sure of the code for R-value in my location, but I think it’s R49?
Ive seen so many posts about the possible health problems with spray foam that I’m leaning away from that method.
to provide more air circulation in the summer months (unbearably hot without window ACs), I was thinking of creating a channel at the peak and installing vent fans at both ends controlled by thermostat.
the space is part master bedroom (with a small bathroom) and part a work/office area for the family.
the only heat currently (Besides that which flows up from the first floor radiators) is an old electric baseboard in the bedroom, and an old wall mounted heater with fan in the work/office area.
I’m planning to update both heaters with new baseboard electric heat controlled by thermostats.
We’re doing this in 2 parts: the back half of the attic is currently under remodel, and the front half (master BR and bath) will be done at another time.
Any help in coming up with a prescription for air sealing, insulating and venting is most needed and would be greatly appreciated.
Thanks! Please Help!
GBA Detail Library
A collection of one thousand construction details organized by climate and house part
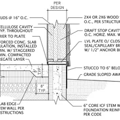
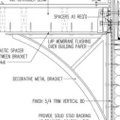
Replies
When I think Victorian house I think multiple gables, turrets, etc. Complicated roof shapes are difficult to vent appropriately. If roof geometry is simple, keep it vented. If you haven't read the Bible on this topic, you should://m.etiketa4.com/article/how-to-build-an-insulated-cathedral-ceiling
Some other thoughts:
R49是前scriptive code for cz5 ceilings. You can also comply with code through the alternative U factor which is 0.026 (~R38 "whole roof"). This will be somewhat easier to meet, but isn't an energy hog. Since you're planning on strapping the ceiling anyway, use 2x on the flat (or on edge, if you'll still be able to stand up) and insulate the strapping cavity. The thermal break will go a long way towards U factor compliance and is more economical than a layer of rigid foam under the rafters.
Gable vent fans will probably make things worse by accelerating air leakage.
//m.etiketa4.com/article/the-top-two-reasons-powered-attic-ventilators-are-a-waste-of-money
You can finish the other half of the space whenever you like, but the entire space needs to be insulated and have a continuous air barrier installed as an assembly. Insulating and air sealing in stages will be more expensive and make thermal/air barrier continuity more difficult. Don't just trust your workmanship: test the airtightness of the assembly.
Rather than upgrading baseboard units, consider a ductless mini split.
Hi Bryan thanks much for your comments and knowledge. I’ve read through the Cathedral Ceiling Bible. A lot of info there for sure.
Questions:
——cz5是什么?
- “You can also comply with code through the alternative U factor which is 0.026 (~R38 "whole roof"). This will be somewhat easier to meet, but isn't an energy hog.
Have no idea what you’re referring to in this statement. In addition, “Easier to meet but isnt an energy hog” is confusing. If you could clarify I’d appreciate it.
- “ The thermal break will go a long way towards U factor compliance and is more economical than a layer of rigid foam under the rafters”.
Again, not sure what you mean? Isn’t any insulation - whether it’s in the actual rafter bay or in the space created by strapping - considered a thermal break?
- my roof/rafters are a 10/12 pitch, and they’re 2x6’s. Not much space to insulate To get to R49. I can increase their depth to minimum 7” (2x on flat), to probably a maximum of 9” (2x4 on edge). But I still need 1 to 1 1/2” for the vent baffle.
- the only insulation I’m planning for the floor is to cover the entire deck (which currently is 3/4 barnboard with 1/2” ply over) with 1/2” Acoustic Insulation Sound Board, and then 3/4 ply or advantec over that.
- if it’s recommended to just rip out the existing 2 layered floor, insulate the floor and THEN put down 1/2 Acoustic Board, then 3/4 sub flooring - I’m willing to hear about this approach!
- RE: mini split- we’re going to do just that. We’d taken off the list but have put it back into the budget. It seems like the best way to go.
RE: vent fans - I hear what you’re saying and I think I’m going to air seal and vent - hopefully properly - and don’t expect to use the fans.
Thanks for opinions -
Brian
CZ5 is climate zone 5.
R49 is the prescriptive code ceiling insulation requirement. If you had a vented, unconditioned attic, you would pile R49 (or more) of cellulose (or whatever) on the attic floor. In your assembly, if you were following the prescriptive code, you would pad out the roof framing until you had enough space to install R49 insulation. In a retrofit, this is probably impractical.
An alternative compliance method is the U factor alternative, which includes not only the R value of the insulation, but also the other materials in the assembly, including the framing. This doesn't help as much as you might think--those 2x6 rafters have an R-value of ~6 or 7 and might represent 15% of the roof. For instance, 85% of the roof has R49 and 15% has R6, the "whole roof" is only about R24--this is why full cavity depth closed cell spray foam is a poor use of insulation dollars.
If you choose to follow the U factor alternative, you can use this online calculator, or you can use it to illustrate the principle:https://www.ekotrope.com/r-value-calculator
Thermal break is shorthand for getting continuous insulation over framing. This is important all of the time, but especially in cathedral ceilings. Cross strapping the rafters and filling the strapping with insulation boosts the R value of the assembly considerably. Continuing the example above, just an 1.5" of cellulose raises the assembly R-value to ~R33. On edge 2x strapping will make an even bigger difference.
Others can comment on the efficacy of various sound dampening strategies. I do not know enough to offer any advice.
Thanks again Bryan for your input.