Air Barrier for Existing Porous Attic Ceiling

I’m redoing the insulation in the attic of our 110 year old house in the pacific northwest (Vancouver, BC), putting down two right angle layers of r20 after removing ancient dense white loose insulation (testing determined it to be cellulose with no asbestos) over some crumbling yellowed building paper.
The finished side is 18″ x 33″ douglas fir paneling with 1.5″ strips on the seams all stained and polyurethaned for a strange yet cool look I’m planning on keeping.
Under the tar paper is old ship lapped 1×8 fir that’s mostly not very snugged together so there’s a lot of ways for conditioned air to sneak into the attic through the panel and ship lap seams.
Though I have a great stuff pro setup with a gun, there’s far too many shiplap cracks for that so my plan is to line the joist bays as before but in a more effective way that won’t break down for a very long time.
My three ideas for that are:
A) U shaped lengths of cardboard stapled to the joists and sealed with red tuck tape
B) tyvek house wrap stapled to the joists and sealed with red tuck tape
C) #30 felt paper (so it takes longer to break down) stapled to the joists (don’t know of a tape that’ll stick to this)
Plastics seem to become brittle over time as does tar paper but cardboard seems to be pretty durable not to mention being the most cost effective and eco friendly so am leaning that way.
Wondering if others could let me know their thoughts?
Dave
GBA Detail Library
A collection of one thousand construction details organized by climate and house part
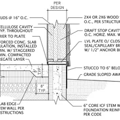
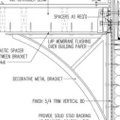
Replies
Cardboard, at least regular cardboard, doesn't have any kind of fire rating and is probably not going to be approved for use on a project like this.
I'm not sure how well your options B and C will hold up over time for air sealing purposes either. My first thought is to either use luan or polyiso ripped to fit the rafter bays and seal those in with canned foam. This is a variation on the cut and cobble technique. If you use blown cellulose over that, that will help too since cellulose is better about limiting air movement compared to fiberglass. I would seriously consider using blown cellulose here and not fiberglass batts. Blown insulation is easier to install, and insulates better too!
Note that "canned foam", the "gun foam" you refer to, is not "spray foam" of the type you may be thinking of. Spray foam of the kind described sometimes as having problems curing, smelling, etc, is two-part spray foam which is a very different material from the one-part canned foam. The issues you sometimes hear about with two-part spray foam don't apply to one-part canned foam.
Bill
Hi Bill, appreciate the quick response and good point about fire rating which is something I actually hadn't considered as substituting cardboard for paper didn't seem that much different but will mull that over.
To paint a little more detail, my office where I'll be unexpectedly working this winter is on the top floor and our gabled roof is about 45 degrees. Fairly tall uninsulated paneled knee walls (also over shiplap) with 1x3 studs transition to a 30" 45 degree section whose 2x4 rafter bay is currently stuffed with ancient rockwool holding up the last remnants of the old white loose cellulose from the upper attic.
I'm planning on making custom baffles out of rigid foam for that sloped section (cut and cobbled with cleats to offset it from the roof deck) to allow air to flow between the two attic cavities so I've got quite a bit of foam fussing ahead there and am keen for a quick win on the joist bays above so I can move on to the kneewalls where I'm planning on thickening the walls to 2x6 width and then using r14 rockwoool covered by 1" shiplap r5 taped rigid foam (as an insulating air barrier) with 3/8 plywood as a fire barrier.
As for loose vs batts, I actually already have all the r20 batts which I got 30% off awhile back and like the idea of being able to easily shift the top layer out of my way to lay a plank down on the 2x6 joists when the need arises to crawl around the attic for accessing the vents, inspecting the cedar roof from underneath etc. (one can see the bottom of the shingles that are nailed directly to the battens)
Contrast that to our similarly aged cabin where I need to dig around in cellulose to find the oddly spaced joists to kneel on, stirring up a big mess as I go!
PS
Have corrected my original post to not refer to spray foam, thanks for the clarification there.
It’s hard to argue against deeply discounted insulating materials :-)
You mention R5 rigid foam, which makes me think you’re planning on using XPS. Please reconsider and use polyiso instead. This is a green building forum after all, and polyiso is a greener material. You also gain more R per inch (1” polyiso is R6), and the foil faced type of polyiso that is most common in the box stores is also the easiest to get a good taped air seal with. Polyiso is fairly stiff too so it’s good for making things like vent baffles.
You can build a cat walk across buried joists by placing support boards on edge perpendicular to the floor joists and then running planks over the tops. This way you minimize thermal bridging since there is only a few 1.5” squares where the wood members overlap that aren’t surrounded by insulation. The other option is to build a frame of 2x4s inside trusses or sticking up from the floor joists and supporting a catwalk that way. You just want to avoid large amounts of wood going all the way through the insulation acting as a thermal bridge.
Bill
Thanks for the info on the XPS which I already bought but not on sale so no skin off my nose to return. I googled around a bit but and the GWP of the blowing agents looks nasty as no one has apparently switched over to HFO yet.
I found one article that says that polyiso loses its effectiveness when cold (sub 10 C) which isn't a good thing with our chilly winters. Is that the general consensus?
https://www.ecohome.net/guides/2254/polyisocyanurate-foam-is-a-hot-new-building-product-learn-where-and-where-not-to-use-it/
The one inch isn't a major r factor over all in this wall assembly so taking a hit there wouldn't be a big deal.
SOME polyiso (not all) has that issue with reduced R values in very cold temperatures, but it’s not always as severe as you see in the articles (especially the one everyone seems to link to). Dana, another frequent contributor here who appears to have taken a hopefully brief leave, had once referred to that as “worlds crummiest polyiso” when he was pointing some things out to me just as I am to you now.
Basically polyiso is a net benefit over most of the year, and the shoulder seasons, and while it might underperform it’s rating in the coldest times of winter, even when derated it still performs about the same as R5 XPS. XPS, BTW, has its own set of issues with its R value gradually diminishing over time as the blowing agents diffuse out. XPS years down the road ends up performing similarly to R4.2 per inch or so just like EPS. Polyiso is much easier to tape than either XPS or EPS too.
BTW, some time ago I was pretty thoroughly converted and have used almost exclusively polyiso, usually reclaimed or manufacturers seconds, as I gradually beef up my own home’s insulation. I am gradually putting in 3” of polyiso over the entire exterior as I do other upgrades. It makes a very noticeable improvement in all seasons over the R11 fiberglass batt walls that were there before (those get upgraded to R15 mineral wool too).
Bill
Looks like I can find 1" or 1.5" polyiso dual foil faced locally at about half the $/R/sqft of XPS so am definitely going to go that way for cost and green-ness :)
反复思考后几天,有德cided to address my original question with Bill's suggestion of cut + cobble + great stuff pro (fire rated foam) between ceiling joists using 1.5" polyiso. The last thing I want to deal with is an insurance company saying that I shouldn't have put something in there with a low ignition point like cardboard. Cutting, fitting and foaming it probably won't take much longer than cutting and taping something non rigid anyway, plus an extra R9.3 will be way better.
I'll continue the concept down the rafter bays on the interior surface of the sloped voids and then on down the outside of the kneewall assembly for its 2nd last layer; all at 1.5" since that's 25% cheaper than 1" R6.2 for $/R/sqft. As a bonus, the foil face of the baffles will act as a radiant barrier too during the summer!
I'm planning on taping all the seams with some aluminum foil HVAC tape I have on hand which I assume should be fine?
Assuming that's the right way to go there, the only question is the thickness for the second layer of rigid polysio that I'll be using for the baffle within the sloped wall assembly.
The rafters are only 2x4 so I could probably squeeze in another layer of 1.5" since the shingle nails only poke down a little over 1/4" through the battens but that'd only leave a 1/2" gap under the ceiling for air to flow between the lower and upper cavities. Is that adequate or should I use 1.5" + 1" instead to leave a larger 1" gap at the expense of insulation?
很乐意听到别人思考the insulation/air flow tradeoff in the sloped wall section between A) 3" of polyiso at R18.6 w/ a 0.5" air flow layer and B) 2.5" of polyiso @ R15.5 w/ a 1" air flow layer.
Not sure how things operated prior to someone plugging the sloped wall sections with insulation years ago, but currently the whole roof deck breathes very nicely and there's no signs of moisture / mold despite the two cavities being partitioned so I'm tempted to err on the side of insulation and go with a smaller gap.
Good deal on the cheap polyiso! I love getting deals on materials like that.
I see no issue with the foil duct tape, aside from liking a wider tape myself (makes alignment less critical). Nashua makes an excellent tape of that type that the orange store stocks. Note that the foil face won’t help you as a radiant barrier if you bury it with batts. Don’t be tempted to leave it exposed though since the batts will gain you more insulating performance than the radiant barrier would.
1”发泄差距最小的代码。有些人再保险commend more than that. It becomes more critical as the pitch of the roof decreases (low slope gets less air movement in the same size vent gap). I would tend to stick with at least 1” for the vent gap and more if possible up to 2” or so if it doesn’t compromise your insulation. In your case I’d probably just stay with the 1” gap and use the rest of the space for insulation.
Bill
1" gap it is then and I'll be burying the horizontal stuff in at least R40 of batts so won't get any radiant barrier protection there but will on the 45 degree sloped vent gaps. A moving layer of air will probably help in the summer anyway.
Speaking of air flow, is there a volume based rule of thumb in how much venting one should have to let the air out of the upper section?
There's a couple of vents on the roof but it doesn't seem much compared to what I see on new houses.
Our top (third) floor has a 45 degree gables roof up 40' so adding access from above is not realistic but adding flush mount wood gables is feasible since I can cut the holes from the inside for a pitch style ones, push them out through the hole and then fasten them from the inside.