Architect’s question: Plank house insulation

My client is renovating a “plank house” in Zone 6 (west central NH). The house is timber framed with 2″ thick vertical wood planks outside of the frame for exterior walls. There is 1″ (actual) thick wood sheathing on the exterior of the planks (so a total of 3 inches of solid wood). Interior lath & plaster or wood paneling has been removed.
The owner wants to frame 2×4 walls with spray polyurethane foam on the inside of the planks and put 1″ rigid insulation board (not sure which variety) on the exterior.
I have expressed my concern to him that 1″ is inadequate in our climate zone, and that with vapor impermeable insulation on each side of the wood structure he may be creating condensation issues. However, my exposure in the field and at Better Buildings by Design conferences has been with standard framing, not plank construction. I do not have energy modeling software to analyze this wall system. Any input would be appreciated. Thank you.
GBA Detail Library
A collection of one thousand construction details organized by climate and house part
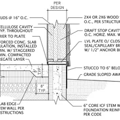
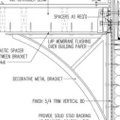
Replies
Pam,
Ideally, the exterior rigid foam will be somewhat vapor-permeable -- EPS would be a good choice. You probably don't want to use rigid foam with foil facing.
也就是说,水分问题的风险low, because the resulting wall assembly is likely to be airtight.
If you have any input, closed-cell spray foam would be safer than open-cell spray foam, because closed-cell spray foam would minimize the diffusion of interior moisture toward the planks during the winter.
Martin. Thank you very much for you prompt and insightful reply. It gives me specifics to take to the owner, w/o is GCing his own project.
A flash-inch of closed cell polyurethane is about 1 perm, or a bit lower, is sufficiently low perm to protect the 3" of wood. It's also forms the first condensing surface for 2.5" of fiber insulation.
High density fiberglass or rock wool runs about R10 @ 2", and the 1" closed cell foam is good for at least R6, which is about 38% of the cavity R and PLENTY of dew point margin even before adding in the R3.5 for the wood, and the R4-R6 for the exterior foam. At temperatures that matter 1" EPS would run about R4.5, but from a code point of view you'd still have to call it the labeled R4.2.
Assuming R15-R16 cavity fill the framed section has a whole-wall performance of about R10...
... allowing a generous R8 for the combined exterior foam + 3" wood...
.... and another R2 for interior gypsum plus exterior siding plus air films...
... you're looking at a "whole wall R" of about R20, or a U-factor of U0.05, not lower.
IRC code max for climate zone 6 is U0.45 (= R22 "whole wall"), so to get there with just 1" of exterior foam you would have to use foil faced polyiso, which is a true vapor barrier.
If you want to keep it somewhat vapor permeable and can afford another half-inch, going with 1.5" EPS (R6.3) would get you there too. At 1.5" unfaced Type-II EPS (1.5lbs per cubic foot nominal, 1.3lbs min) runs about 1.5 perms, which is enough.
With any exterior foam it will be very important to get the flashing details and bulk-water management details of the wall right.
Pam,
Dana is right: "With any exterior foam it will be very important to get the flashing details and bulk-water management details of the wall right."
One way to lower the water-entry risk is to include a rainscreen gap between the siding and the WRB (or the rigid foam).