Basement insulation question

Hello:
I’m building a house in Zone 5 (southern CT). The house will have a full basement with spray on waterproofing. There is no sub-slab foam. The builder budgeted for 2″ of XPS (with dimpled moisture facing) on the sub-grade exterior of the foundation walls, but NOT the above grade portions. There will be a footing drain running to daylight and a shed water system to catch storm water running off of our house (2 foot overhangs; no gutters). The soil is sandy loam and drains well.
The basement will likely contain a heat pump water heater and propane furnace backing up our air source heat pump.
基于我的阅读,由于预算的缺点trains, can I forego the exterior foundation foam, with an eye toward insulating the basement via the interior side (floor and walls) with rigid foam at some later date? As I understand it, if I were to install the foam below, but not above grade, there is not much value in the insulation due to the exposed portion of the foundation wall. We do not have the funds to spring for exterior foam under the slab and above grade (and related finishing costs). I could use the savings from the foam elsewhere. Anyway, please let me know your thoughts. Thanks.
GBA Detail Library
A collection of one thousand construction details organized by climate and house part
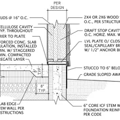
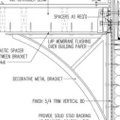
Replies
Insulating it later is fine. R10 foundation insulation doesn't meet IRC 2012 or newer code minimums for zone 5, which is now R15 continuous insulation. That would be pretty awkward to retrofit above the existing exterior XPS.
在新英格兰南部有超过一个瞌睡n foam reclaimers selling used-once foam in good condition, at 1/4-1/3 the cost of virgin stock goods. Even 2" roofing polyiso on the interior extending down to an inch off the slab is pretty good, and can be trapped to the wall with a studwall insulated with unfaced batts to meet/exceed code minimum performance. Two of the larger reclaimers that always have something suitable in stock are Green Insulation Group, in Worcester, MA, and Nationwide Foam in Framingham, MA, but you can also just search the local craigslist until you find something more local. Many of the smaller reclaimers advertise that way, as to one-off deals that come up.
http://hartford.craigslist.org/search/sss?query=rigid+insulation
http://www.nationwidefoam.com/
http://www.greeninsulationgroup.com/
You can't just stop a few feet below grade with the interior foam, due to the extreme thermal bridging of the concrete. Polyiso can't rest on the slab without some risk of moisture wicking into it, but EPS and XPS can. If you take a foam + insulated studwall approach you need at least an inch of polyiso or 1.5" of EPS/XPS to limit the wintertime moisture accumulation in the above-grade fiber, and you want an inch or so of EPS or XPS under the bottom plate of the studwall to keep the wood above the summertime outdoor dew point averages, and not wick moisture into the wood. Since it's not structural, you don't need to double-up on the top plates the way you would on a structural 2x4 wall.
As Dana says, reclaimed foam is widely available and cheap. You'll never get another chance to insulate under the slab. Will you ever finish the basement? If you insulate the slab, you won't regret it. Take the money from somewhere not so permanent.
Thanks, Dana. So if there is NO insulation on the foundation walls for a period of one year or two years, will that be a problem with respect to the building code? Note that my permit is under the prior code (2009), as it was approved prior to adoption of the 2012 code.
Adam,
Whether or not you can get an occupancy permit for a house with a code violation depends on your local building department. The way I see it, if the above-grade portions of your basement walls are uninsulated, then your basement walls are uninsulated.
But my interpretation doesn't matter. The only interpretation that matters will come from your local building official.
Thanks, Martin. I did a bit more digging. Our builder is also insulating between the 1st floor and basement, so there should be no issue with respect to the code. That said, I'm still looking into continuous exterior foundation wall insulation as a possibility, using Pro-Guard, FP Ultralight or foam+Groundbreaker on the above-grade portions.
If the propane furnace is in the basement, below the ceiling insulation, it's putting it outside the thermal boundary of the conditioned space, which increases the net load. The duct losses to the basement become truly lost rather than accruing to the heat load of the house by keeping it all inside the thermal envelope.
Bringing the entire floor up to the IRC 2009 prescriptive R30 is a lot of fluff- it's not free. And air-sealing the basement from the first floor adequately is damned near impossible unless there are only very few penetrations of the sub-floor, and access to the basement is only from the outdoors.
Rather than spending money on the floor insulation, apply that to insulating the interior sides of the foundation wall to the IRC 2009's mandated R10 with 1.5" of fire-rated polyiso, or 2-3" of reclalimed roofing polyiso sprayed with intumescent paint, if you really can't just slap up a studwall & wallboard now, to be finished later. You'll need at least an inch of polyiso or 1.5" of EPS for dew point control on a batt-insulated wall, but the stuff is dirt-cheap through foam reclaimers & factory-seconds folks. It's easier to properly detail & finish an interior insulation approach than an above-grade exterior.
At the very least put a couple inches of reclaimed polystyrene (EPS or XPS) foam under the slab, and 2" of polystyrene on the edges of the slab to thermally isolate the slab from the foundation wall & footing. That keeps the slab warmer, and any future flooring or partition wall materials in contact with it dryer, pretty much eliminating the smelly dank basement problem. It's not required by code, but it's "worth it", especially a the 10-20 cents per square foot 2" thick reclaimed goods would cost. It means either excavating 2" deeper or raising the slab by 2" to accommodate the foam, but it's a cheap and effective upgrade, assuming the concrete isn't already poured.
BTW: The propane biz in most of southern New England is run as micro-monopolies, where the propane dealer owns & maintains the tank, and is the only company allowed to fill that tank. Replacing the tank with another dealer's tank usually comes with a hefty removal/replacement fee. For small and medium volume users this often becomes an abusive situation, being held hostage to elevated pricing by the grand or two it would take to go with another vendor. Even at this year's lower propane pricing and CT average electricity pricing ductless heat pumps are substantially cheaper to operate, and offer high efficiency air conditioning to boot. The up-front cost of a right-sized ductless approach isn't always higher than a propane furnace + AC condenser & coil either.
A bit over a year ago I was involved in a project for a 3200" house on Martha's Vineyard MA where a proposed propane furnace w/ AC coil & condenser (all oversized) came in at ~ $25 K, all-in. The 6-zone 4 ton ductless solution that was eventually installed (also oversized) came in at ~$15K (and qualified for some MA rebate subsidy, bringing the out of pocket even lower.) The operating cost is also substantially less- about HALF that of a propane burner at "island pricing", even at the higher electricity rates on MV compared to the mainland. This was no super-insulated jewel either- half the house was 2x4/R13 from the 1970s, and the brand-new half was 2x6 / R20 code min above grade, with only R10 exterior insulation on the foundation (below-grade only, just like yours.)
Before pulling the trigger on the floor insulation and propane fired heating system, run the room-by-room load numbers with a Manual-J while there is still time to tweak & optimize things. Insulating the basement walls above grade to R10 and skipping the floor insulation to bring the mechanicals all inside the thermal boundary of the house will cut the heat load numbers by more than 10,000 BTU/hr for most homes.
Thanks, Dana, Stephen and Martin. Footings are expected in the next few days, foundation walls next week and the slab may not go in until spring so I expect to have some time to suss this out. The local building dept suggested that foil faced polyiso on the interior basement walls may be acceptable without intumescent paint (presumably, until we use the basement space).
We still may still end up with air source heat pumps but are budgeted for the propane unit. We are hiring an energy consultant to help with the Manual J calculations.