Moisture Control for New Storage Shed

I’m going to build a storage shed, 12×20, for a mower and storage of building materials and tools. It will likely have a rollup door on one end, probably a 6×7 or 7×7, which is not the greatest for insulating or air sealing. 2×4 stick-built, likely with OSB sheathing, or I may use this as a install test bed for Zip sheathing (there’s a garage/shop on the horizon, and the house needs some exterior work too). I need to do the math on the costs of pandemic-era sheet goods.
Climate Zone 3.
Probably building on a slab because there’s zero reservations about a heavy mower, and I wouldn’t want to mess with exposed insulation on the underside between floor joists (if insulated).
I am primarily concerned with condensation control for rust issues, but am not planning on doing any HVAC-based climate control. I will likely use it as a shop for a while (until the garage is eventually built), but don’t want to divert a lot of time and money into insulation details if not necessary. This is supposed to be a lower cost stopgap to building the much larger attached garage until material prices stabilize.
What things should I be shooting for in order to keep condensation under control? For example, if the only good answer is to insulate it, and rigid foam would be on the roof deck, I would want to plan to install before putting a roof on.
这是添加dehu那么简单,同时付款ing attention to the easier air sealing details, or would insulation be required?
I’m expecting the answer to be “If you don’t have a leaky envelope, you don’t have to worry about condensation”, but my building science intuition falls short because of the lack of climate control.
GBA Detail Library
A collection of one thousand construction details organized by climate and house part
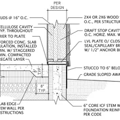
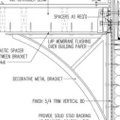
Replies
If you aren't going to condition the space, than you have no control over moisture or condensation. Condensation will occur any time the temperature of any particular thing drops below the dew point of the surrounding air. If you have something with a lot of thermal mass (big chunk of steel, for example), that will tend to stay cool for a while as the air warms up. Depending on conditions, you may get condensation forming on the chunk of steel at times.
If you want to keep condensation under control, you need to insulate, and you need to heat the space. You don't need to heat things very much, even a few degrees above ambient is usually enough. This is commonly done in large outdoor electrical switchgear to keep condensation from forming on energized components inside the cabinet. The typical heater is around 200-250 watts or so for a cabinet about 3 x 3 x 8 feet high. It doesn't take much. Those cabinets aren't insulated at all, either.
In your case, I would put a vapor barrier under the slab, I would insulate the shed with rigid foam (easiest way), and I'd put in a small permanently installed electric heater (assuming a small shed), and set it pretty low. I think this will suck a fair bit of energy, and your rollup door is probably going to leak so much it will cancel out much of your insulating efforts. That's a way of saying "yes, you can do this (condensation control), but it comes with tradeoffs so know what you're getting into".
Bill
Well, I have a well built and unconditioned shed (CZ 2). Blower door tested to 2.2 ACH (hey, they were on site and I worked hard on that thing :) We don't have a slab, it's raised on beams.
We installed a vapor port, seehttps://www.buildingscience.com/documents/insights/bsi-088-venting-vaporand I've monitored the humidity and temp in the shed constantly with a data logger.
The dewpoint inside the shed is always way lower than outside and water from bikes etc evaporates very quickly. My read is that this is acting as a solar powered dehumidifier (as discussed in the article above).
So I'm not saying don't plan for some dehumidification and/or heating, especially if you have big equipment being put away cold. But definitely include a vapor port in the ridge :)
I’m planning my own “well built unconditioned shed” and am curious about your air-sealing strategy, especially the floor. Mine will be on raised beams also. What assembly did you use?
Pretty much thehttps://foursevenfive.com/2x-framing/"smart enclosure" with rainscreen gap but no external insulation. 2x lumber, shed roof with no eaves, taped membrane (zero perm proclima green stuff) all six sides, with high perm membrane over the sheathing cut for the vapor ridge port. Rainscreen using 1x4s and wood siding, metal roof over 2x4 criss-crossed on the flat (creating 18" overhangs) with Cor-a-vent.
Floor was indeed the hardest bit. I laid a 2' wide strip of membrane on top of the beams, then the joists went over that (cantilevered). I installed rockwool batts before adding the taped membrane. I then taped the floor sheathing above that so that rain didn't get in there during the rest of construction. But I left the underside membrane off until the roof was on, just in case. The bottom of the floor joists were high enough that I could crawl under, staple the membrane under the joists and tape to the flaps that I had put on the beams later. The joist to beam connections were toe-nailed with a few hurricane clips (which were obviously a pain to tape as they came through the membrane).
If I did it again I'd use Zip sheathing (much more widely available now) rather than the membranes and I'd look very hard at the approach of using hand crank equipment lifts to raise the floor up for air-sealing the underside. I think this is the article:https://www.finehomebuilding.com/project-guides/insulation/air-sealed-and-on-piers
Of course the windows and door are the weakest links because it's hard to spend real money on a shed and cheap windows and doors are unavoidably terrible.
Thanks for the details, James. Did you finish out the interior with insulation, Intello, and wall finishes? Looks great!
How did you approach the interior? Did you use a vapor retarder and drywall?
James, that's a pretty awesome roof detail. I'm planning a shed roof (lacking an easy place for a vapor vent), but I'm sure there are some details that could be added at the high edge of the shed roof, like Densglass blocking behind ventilated soffit trim or something like that, or substitute for sheathing at the top edge with a furring step (or metal roofing attached to strapping).
Actually I also did a shed roof, just put the sheathing cut at the high side, with high perm wrap over the gap (about 12" of high perm taped onto my low perm membrane). The gap in the sheathing is only 2" so I can't see that it affects racking strength with the rest of the roof entirely sheathed.
I then ventilated above the membranes with criss-crossed 2x4 on the flat creating 18" eaves (and metal roofing above that).
Hey, I found some pics, one from above, one from below (inside). And a few of the rest of the build.
Oh, and don't put it up so high because then you have to also build a deck and a ramp to get things in and out. Ask me how I know :) So that's why if I were ever to do this again I'd just beams in the floor (not cantilevered) and air-seal the floor from below up on equipment lifts, then lower it back down, as shown here:https://www.finehomebuilding.com/project-guides/insulation/air-sealed-and-on-piers
This solution interests me greatly- I have a garage/workspace that was built out before I became homeowner. It is an insulated / sheetrocked space with a cathedral ceiling. For some reason the builders left about 24" to either side of the ridge beam open and un-insulated. There is R-38 fiberglass batting the rest of the way down. Outside there are soffit vents but they did not use vent baffles in the cavities- so no airflow! The space is heated /cooled with a heat pump. Needless to say the ridge interior became a moldy mess. I have addressed the mold issue but now am at a loss as to how to fix this without tearing out all the sheetrock and insulation in the roof and venting it properly with a ridge vent and baffles etc. This vapor port solution looks like the ideal fix- I could repack the insulation I removed, resheet rock the area I removed that was damaged, close the soffit vents and construct a vapor port at the ridge. I'm in CZ3. Does that make sense? It seems like a good solution. There is a catch. The roof is done with open sheathing- 1x8 boards with maybe 1/2" gaps - would the vapor port method still work? I'm not looking for perfection- It's a shop/ studio space I keep as minimally heated cooled as I can.
In warm weather (when things rust faster), air sealing plus dehumidification will work well. Make the walls and floor lowish perms (say around 1 perm).
+ 1最大化太阳能得热。我已经成功with VCI (volatile corrosion inhibitor) to stop rust on small tools. Much nicer than oiling.
You are CZ3A, correct? If so, I agree with Bill that you will struggle to control rust, mildew, and mold in an unconditioned shed. So I'd avoid storing leather or natural fabrics in that space and try to limit rust on hand tools by keeping them oiled.
Thanks for the replies.
So far we have:
The best (but most expensive) option, which is insulation plus some type of conditioning.
The middle option, which is to do humidity control and cross fingers.
The easy and cheap option, which is to not keep expensive things that can rust in the shed.
I'm leaning toward the easy option, because the best/insulated option will divert money from the future conditioned garage, which will be the more permanent home for many things. Doesn't really address some of my short-term storage needs though.
I'm sure I'll have more questions after pondering this a bit.
Note that if you take the option to keep it dry by providing heat, you are better off providing that heat with a dehumidifier. You get more heat out per kWh in, and you get the dehumidification as a bonus. I suspect that with good air sealing and modest insulation this could be an effective strategy at pretty low energy cost, assuming you let the humidity go higher when it's very cold and rust and mildew are less of a concern. If that's not good enough, dessicant dehumidifiers can work down to low temperatures. They are less efficient than conventional compression cycle dehumidifiers at high temperatures, but if the concept is that it's tightly sealed, the dehumidification load it has to meet could be very low.
Solar gain could also help, as could rust inhibitors.
In theory, you could have a smart active ventilation system that would bring in fresh air when the outdoor dew point was lower than indoors, perhaps through an HRV system. But I think you'd need to design your own controls, and I'm not sure you'd end up with lower energy use than sealing it up well and dehumidifying, and there might be times of year when it's hard to find dry enough outdoor air.
The ultimate low-energy option would, be a solar desiccant dehumidifier, but I don't think there's one available at the scale you'd need.
Maybe Climate zone 3 is alot different than where I am in Climate zone 6, but... I think you're over thinking this. I have about 20 years experience of having workshops in unconditioned detached garages (lol big accomplishment). There are only a couple days a year that the temperature swing is bad enough to get noteceable condensation. This is usually a rapid warming event in the winter - something like from normal 20 deg F winter weather to 50 degree and raining overnight. I have only really had significant condensation in uninsulated garages. In my current insulated but unconditioned garage (it has a wood stove for when I need it) I have not had noticed any condensation. I believe the insulation tempers the temperature swings and it's relative airtightness tempers the humidity.
Let's say you just go uninsulated, vented shed. Still, in my experience, the only things you really need to worry about are cast iron machine tops (table saws), steel welding tables, tool steel planer knifes, machinist squares, etc. These things you can keep rust free just by applying wax or oil to them every now and then. If you have a big condensation event, just wipe the water off the items. If they do rust, it's nothing some scotchbrite can't fix.
I'm intrigued by the idea that almost all the rust/mildew might occur during rare condensing conditions. So maybe limited dehumidification with poor air sealing or electrical heating with little insulation wouldn't actually cost much. Might have to try it in combination with some data logging.
I do use a fan - which clearly speeds drying of anything that is wet.
I know my advise will sound strange but I say don’t insulate don’t air seal in fact I think you should ventilate.
Insulating and air sealing are our big tools and sometimes we need to consider other options.
Think about the millions of unheated sheds, cabins, crawl spaces and attics. Most are well vented and no mold or rot until someone closes the vents.
Yes if you fill the shed with hundreds of pound of cast iron machines in the spring a few days the air will warm up so quickly your iron will still be cool enough to fall below the dew point and sweat like a can of beer on a hot day. I understand they make covers that will help if not eliminate the problem
Walta