How many BTUs of energy do I lose per cfm leakage to outside in my ducts?

I would like to calculate how much energy/money I am losing from duct leakage outside my building envelope. Is there a way to quantify how many BTUs I am losing per cfm of leakage in heating and cooling?
GBA Detail Library
A collection of one thousand construction details organized by climate and house part
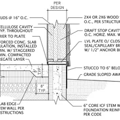
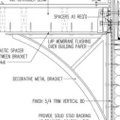
Replies
Chaz,
The calculation is complicated; in order to make it, you will have to make certain assumptions.
First of all, if you have a supply duct that is leaking air to the exterior, all of that leaking air will need to be replaced by outdoor air infiltrating through cracks into your home. The number of BTUs needed to heat that outdoor air to room temperature will depend on the outdoor temperature.
Air has a specific heat of 0.0182 Btu/cf/°F. If (for example) the outdoor air is at 0°F, each cubic foot of outdoor air would requires 70 x 0.0182 = 1.274 BTU to warm from 0°F to 70°F.
You can use the same formula to calculate the BTUs required to heat the air distributed by your furnace; in that case, the air needs to be heated from the return-air temperature to the supply-air temperature. (You can measure those temperatures with thermometers inserted in your furnace plenums.)
Finally, it's worth pointing out that the relationship between air leakage from ducts located outside of the thermal envelope and the infiltration of outdoor air into a house are dynamic, interactive, and complicated. Any assumptions you make will be based on an oversimplified model of what's really going on.
It is indeed complicated, and cannot be modeled directly since there are too many unknowns.
Using the specific heat of the air volume to calculate the heat loss is good for setting an upper bound, but it an unrealistically high estimate due to the "heat exchanger effect" along the infiltration & infiltration paths. Using the specific heat assumes the leakage paths are highly insulated tubes, where the exiting air is fully leaving the thermal envelope at the conditioned space air temp, and the incoming air arrives fully indoors at the outdoor air temp.
但这几乎是从来没有的the case. As the conditions space air moves through a crack or fiber insulation etc it begins cooling off as it transfers it's heat to the proximate materials along the patch, which in-turn lowers the rate at which heat it conducted out along that path. Similarly, as air moves in from the outdoors it warms up, cooling the outer layers of material on its path, reducing the rate at which conducted heat is leaving the exterior near that path.
The BTU losses are sometimes measurable as differences in heating fuel use when a ducted-air heating solution is swapped for a hydronic heating solution. For "typical" houses of average house & duct tightness the fuel use penalty for ducted air is usually in low double-digit percentages but with large 1-sigma error bars due to the difficulty of getting sufficient precision on all of the variables. On very tight houses with very tight ducts it's pretty much "in the noise" of the measurement accuracy. It's a lot easier to measure the duct & house leakage under active and high pressurization with blower doors or duct blasters, far easier than measuring the volume of "natural" or air-handler driven air infiltration, let alone the heat exchanger effect aspects of the actual leakage points.
So here is what prompted the question. I have a customer that heard about this product called aeroseal. I have heard of the product before and have heard good things about it. The only bad thing that I have heard about it is the price. I have seen quotes between $1500 and $3000 dollars. So the ever present question is "is it worth the cost. Without modeling the cfm drop and measuring the total leakage and leakage to outside, before and after, there is not a good way to answer this question. What do you think?
I have heard that aeroseal. has a relatively short life of somewhere around 10 years. Aeroseal is fogged in to the ducts and builds up at the leaks plugging the leaks. It will not fill the larger leaks. Air leaking in the envelope has less of a penalty than air leakage to the outside. Although there is benefit to sealing leaks inside the benefit is sealing the leaks to the exterior,
The problem I see with aeroseal is the ability to seal larger leaks and to seal leaks around the outside of the ducts. The outside of the plenum where it enters the attic and duct boots that penetrate the ceiling are examples. If the ducts are accessible in the attic it would be cheaper to seal with mastic, tape, etc.
I think for the cost a person could manually seal the ducts, do general air sealing in the attic and top off with more insulation. This would provide a larger benefit and better comfort.
Just curious- where's the data on service life of the Aeroseal approach?
I'd be surprised it if leaked any worse than duct mastic after 25 years- can't imagine that it's losing much at 10, but if there's data on that I'd like to see it. It's an expensive approach to duct sealing, but has the benefit of reliably sealing in places that are inaccessible for manual duct sealing retrofits (closed up duct chases, ducts run between joists, etc.)
An additional benefit to sealing ducts in fairly leaky is that the system runs a lot quieter which may be "worth it" on that basis alone. Like most efficiency upgrades, it isn't always going to be purely a Net-Present-Value-of-Future-Energy-Cost-Savings sort of deal. Just as triple pane windows don't always pay off in energy use savings they surely pay off in coldest-temperature comfort. Similarly, adding rigid foam over the roof deck can have a fairly low return on energy savings dollar, but can be huge on preventing ice dams, increasing the resilience of the building. Cutting down on duct leakage & infiltration has similar non-strictly-energy -dollars benefits that can matter, even if the payoff on just energy is pretty tepid.
Between the noise, the reduced pollen/mold dispersion, and the reduction of air-transported moisture it's just plain better to have very tight ducts. But whether it's necessary to use an expensive approach such as Aeroseal is a bit of a judgment call, based on accessibility and measured leakage of the ducts.
How much of an energy penalty is there for air that leaks within the envelope? Not much.
I dont have the info on a service life, I didnt save the link. Consider how aeroseal is installed. It is fogged in the system. It is not meant to coat the inside if the ducts. It is meant to accumulate in the leaks and plug the leak. Once the leak is plugged there is no more buildup. How thick and durable is the layer. Larger leaks will not be sealed.
Will the aeroseal installer climb into the attic and look for larger leaks? What about boots. If you have ever taken off ceiling registers you will know how big of gaps can be around the duct boot.
What if there is a loose joint in the duct or a missing or broken zip tie. A physical inspection would be the only way to find.
I think we are enamored with the high tech approach but fail to weigh the pros and cons. I think if the ducts are not accessible aeroseal may be the best solution, Other times duct mastic and tape maybe better option.
First an upfront disclaimer. I am involved with Aeroseal dealers and have researched this technology thoroughly. With that said, I’d like to respond to some guesswork and hearsay comments with facts and third-party research results. I’ve included links to reports so that you can review the details yourself. Sometimes new technologies and approaches to old problems seem too good to be true. In this instance, I’ve yet to find anyone actually familiar with aeroseal technology, who believes the results do not live up to its claims
As others have stated here, calculating the exact ROI for aeroseal is dependent upon a number of factors, but studies by the DOE (http://1.usa.gov/1qJ0gDq) and others find that aerosealing a home can save homeowners on average $600 - $850 per year depending upon HVAC use, amount of leakage, location of ducts, etc. That is a payback of about 3 years. Compare that to upgrading windows (70 years -http://1.usa.gov/1mBi4w5) or insulating walls (90 years -http://bit.ly/1gbf9d8). It really is one of the best investments a homeowner can make.
As far as the life span of aeroseal, the company currently offers a ten-year warranty – but it has proven in virtually all cases to last much longer. Accelerated testing conducted at Lawrence Berkeley National Laboratory over a four-year period resulted in the technology showing no sign of deterioration in the aeroseal seals – and it continued to seal much past the life span of tape and mastic. It has been durability tested to over 40 years. It exceeds all UL standard tests for durability. So the guarantee – the strongest warranty in the industry - covers the contractor for 10 years for parts and labor for any failure in the aeroseal seal…but the seal itself has proven to last for decades – probably the life of the duct system.
And lastly, to the point of its limited use to small leaks and a direct comparison to manual sealing, aeroseal works on holes that are up to 5/8” in size. That covers 95% of leaks. Anything bigger would usually indicate the need for significant repair or replacement. Fact is, studies show (http://bit.ly/1cMMOBE) that sealing ductwork with this aerosol sealant is typically 50%-60% more effective and 30% less expensive than using tape and/or mastic. Most importantly, it can reach all the ductwork, not just the small portion that is easily accessible.
这个突破性技术减轻吗all duct issues – of course not. But it clearly provides a much more efficient, more cost effective means of reducing duct leakage. If there are issues beyond what the technology can solve, it becomes immediately apparent during the sealing process. At the end of the process, a computer-generated report provides the homeowner with detailed information regarding leakage before aeroseal and after aeroseal. It translates that information into a percentage of reduction as well as a calculation of what that leakage represents in a single hole size. The results are in black and white – as are the improvements in comfort, IAQ and eventually in energy savings. After speaking with dozens of aeroseal dealers and dozens more homeowners and commercial property owners, I’ve concluded that this really is a significant breakthrough technology and well worth consideration for anyone looking to reduce energy use and increase HVAC performance.
Brad,
Your reported savings are statistically impossible. In 2009, the average U.S. household spent $593 for space heating and $227 for air conditioning -- a total of $820 for space conditioning. (Source:
http://www.eia.gov/consumption/residential/data/2009/index.cfm?view=consumption#end-use)
Needless to say, you're not going to get $600 to $850 of annual savings from duct sealing, if your total costs for space conditioning are only $820.
.
Those in New England burning $4 oil in a ducted hot air furnaces paying $3000-5000/year in heating could conceivably see savings on the order of $600-850 (even more in worst-case scenarios.)
The same folks would probably get a better ROI out of ductless air source heat pumps though. Assuming a typical ~15% duct losses, for correcting that to add up to $600 savings implies an annual space conditioning cost of $600/0.015= $4000.
Such houses exist, but they're not the average. That's more than the total non-transportation energy costs for an average home in Massachusetts, according to EIA data:
http://www.eia.gov/consumption/residential/reports/2009/state_briefs/pdf/ma.pdf
Of the ~$3600 in total household energy costs in MA only about 60% of that is for space conditioning (almost all of which is heating), so the total space-conditioning costs are about 0.60 x $3600= $2160. A savings of $600 there by duct sealing would imply 28% of the heat load is related to leaking ducts. An $850 savings would imply fully 39% of the heat load is related to leaking ducts.
While that type of leakage isn't unheard of those probably the 2-sigma outliers, not the median or "...on average..." savings to expect from duct sealing in anything but high fuel-cost situations.