Retrofitting a portion of new roof with SIPs?

I am a homeowner in Austin, Texas. My roof needs to be replaced. My home is one and a half stories. The front portion of the first story was remodeled 30 years ago and a section of the interior ceiling was vaulted. This part of the house is an energy sinkhole – 6″ airspace and who knows what for insulation. I want to resolve this major problem when I re-roof. So far, SIPS roof panels seem to be my best option. As I understand, they could be laid on top of the existing roof decking which is shiplap boards.
Questions:
Are SIPS roof panels a decent/viable retrofit option?
What are the best recommendations for sealing joints between panels?
Since the SIPS are expensive, I want to use them only over conditioned living space. The section of roof I am looking at intersects with a gabled roof over my front porch creating two valleys. Is it possible to successfully connect the SIPs to traditional roof decking at these valleys?
Any and all advice will be greatly appreciated.
GBA Detail Library
A collection of one thousand construction details organized by climate and house part
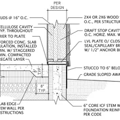
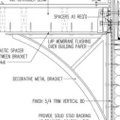
Replies
Blowing fiberglass or cellulose fill the voids, drilling the blowing holes through the roof deck, then installing nailbase panels (not full SIPs) is probably the cheaper/better way forward, especially for a complex angled roof, where the design of full-custom SIPS could be difficult or awkward. The nailbase panels have to be through-screwed to the rafters (the manufacturers have fastener specs and instructions), but they come in 4' x 8' sheets and can be easily field-fitted. They come in both vented and unvented versions.
A 3.5" unvented polyiso nailbase panel adds about R18-R20 to the stackup. If you have at least 6" of blown or compressed batt fiber in the rafter bays you won't need to go any thicker than 3-3.5" with polyiso nailbase panels to meet or exceed the R38 current IRC code-min performance for US climate zone 2 . If you use EPS nailbase panels you may need to bump to 4" or 4.5".
http://www.hpanels.com/images/stories/pdfs/lit_prod_color/english/H-Shield-NB.pdf
http://atlaseps.com/wordpressfiles/wp-content/uploads/2014/07/LIT-1003-Nailbase-PIS.pdf
http://insulfoam.com/wp-content/uploads/2014/04/11014-InsulRoof-InsulLam-TDS_10-24-14.pdf
Sarah,
Dana gave you good advice.
If you prefer to use SIPs, you can -- and if you want to pursue the SIP idea, it would be a good idea to contact a SIP manufacturer to discuss your plan. The SIP manufacturer can answer your questions and provide advice.
Sarah,
The achilles heel of SIPS, which have caused numerous failures, are their joints. From what I understand, to reduce the risk of failure, these need to be sealed from both below and above. That might not be possible if they re installed over an existing roof deck.
Thanks for all the great info. I am feeling much more confident about moving ahead with this project. I have been looking at SIPS from Ray-Core, largely because of the easy access to a seemingly knowledgeable sales staff used to working with homeowners and small contractors. I am going to check out the nailbase as well.
Malcolm, I just wanted to check, if SIPs are installed over an existing roof deck, would a vapor barrier between the decking and the SIPs work to protect/seal the joints?
Suppose it will come down to a combination of cost/efficiency and what the contractor feels most confident installing . . .
Thanks again,
Sarah
Sarah,
Other posters will hopefully weight in to give you a more balanced perspective. My own feeling is that SIPS require their joints to be sealed in a manner that is unrealistic to expect builders to consistently perform, and that the consequences of a poor seal are often widespread failure of the panels.
The contractor is dependant on the manufacturer for their preferred method of installation. It's a leap of faith that as either an owner or builder I wouldn't be comfortable taking.
Macholm,
I agree with your opinion of sandwich panel SIPS. With that said, not all panels are created equal. Ray Core SIPs do not experience those issues. Ray Core panels use closed cell polyurethane foam with a vapor barrier. Sealing joints is easily done with a bead of construction adhesive placed between the panels and foil tapping the joints on the top surface. In 30 years of producing hundreds of projects a year we have never had a roof panel failure. The issues you addressed do not exist with our panel system.
Robert, what blowing agent is used to make your polyurethane foam? Most has high global warming potential (GWP) and doesn't belong in a green building project, but Lapolla now has a "4G" foam that uses a low GWP blowing agent.