Sealing and insulating an old stucco house

I live in DOE Zone 3B in the East Bay area just past the first row of hills in California’s coastal range. My house was built in 1960 and, if I wanted to get it up to the standards of most of the houses I read about here, the first step would be to bulldoze it and start over. But I’d like to do what I can do (and what I can afford to do) with what I have.
At present, most of my exterior walls from outside to inside consist of the following layers:
– Paint
– Tinted stucco (pink)
– Base stucco with poultry netting
-牛皮纸?(肯定不是沉重的felt and looks like just plain paper and it’s in lousy shape with a fair amount missing.)
– 2×4 framing (totally uninsulated and pretty drafty)
– Wallboard (5/8″ I think, but I can’t recall ever measuring)
– Paint
If I lived in Minnesota, I might want to knock it down, but my climate is fairly mild. I can keep this house cool for all but a few days a year just by opening some screened windows at night during the summer. I do, however, pay pretty much for heating this drafty, uninsulated space and I also get a fair amount of street noise inside.
What I want to try is ripping out the drywall in one bedroom and installing rock wool to provide heat and noise insulation. If it worked, I’d do it in other rooms too. I could also use spray foam to seal the wall and provide insulation, but am concerned about the cost and whether I’d feel comfortable doing that as a DIY project.
I’m concerned about how to seal the wall well enough for the insulation to be effective for heat or noise in a house with nothing approaching house wrap or even any sheathing between the stucco and the studs.
I was considering painting the back of stucco with a fluid-applied water resistive barrier (WRB) to keep water out of the wall, seal small holes and gaps, and allow vapor to pass through for some drying. Then I would add the rock wool and (depending if I was advised that it was a terrible or great idea) possibly a vapor barrier, then drywall.
My concerns with that are:
1. Any water that leaked out of the bottom of the WRB would be inside the wall unless I’m able to jam some flashing between the stucco and the bottom plate of the framing (I’m optimistic based on what I’ve seen inside other walls, but I won’t really know until I open each wall).
2. I’d be misusing the product. The fluid-applied WRB is designed to be painted on the exterior of dryish cement, cement blocks, sheathing, or something similar, with the dampness on the outside. It is not designed with adherence to the back of damp stucco in mind, so it may just blister and leak. This would probably be the biggest problem, but I don’t know that my stucco really gets very damp.
3. If I used a vapor barrier on the inside, I wouldn’t be confident of good drying in either direction.
4. There would be no WRB between the stucco and the studs, which might increase the water soaking into the studs just when I was decreasing the drying of those studs. At present, I don’t have a water problem in these walls, except under one poorly flashed window in another room that is a whole different project.
So, is this a terrible idea? What’s a less bad way to insulate this wall, reduce draftiness, and reduce sound transmission? I have a bit of an irrational dislike of blown-in insulation because my house needed a lot of wiring upgrades (adding grounded connectors, removing 14-gauge Romex from 20A circuits, etc.) and I’ve grown to despise the blown-in cellulose insulation in my attic.
Should I just stop whining about the cost and use at least a thin layer a spray-on foam? That sounds more sensible/normal, but I think it only addresses my concern 2, above and might be even worse with regard to 3 and 4, although maybe an inch of open-cell foam allows more drying than I realize.
I know ripping off the stucco and rebuilding the wall from the studs out would be better, but the cost is too high and at that point, I feel like I might as well bulldoze the house, as I still won’t have 2×6 framing, thick insulation, or an airtight house, no matter what I do outside of the current framing.
Any general suggestions on ideas I might want to look into that aren’t as dumb as what I’ve come up with?
Sorry for rewriting War and Peace here.
GBA Detail Library
A collection of one thousand construction details organized by climate and house part
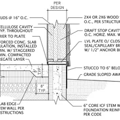
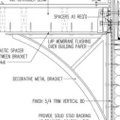
Replies
Domenico,
You're in luck: GBA has an article that addresses your situation. Here is the link:Insulating Walls in an Old House With No Sheathing.
Q for Martin:
Since the exterior is stucco and the OP is located in Calif would it be cheaper to tear it off and insulate from the oustside in?
I only ask because the OP omitted exterior sheathing when he gave a description of his existing stack up.
John,
I don't know what approach will be cheaper -- an interior approach or an exterior approach. The answer to that question depends on circumstances that we can't easily evaluate.
I'm well aware that the house has no sheathing, which is why I recommended the article titledInsulating Walls in an Old House With No Sheathing.
Thanks, Martin. I had poked around on your site for a while and not found that article. I'll go read it and post any questions I have there. I don't honestly know what replacing Stucco costs. I'm sure that approach would be better, but I can't see how it could fail to cost a lot more, particularly given that I can do internal work myself and wouldn't dream of trying to do stucco. The internal approach also lends itself better to a room-by-room approach in an occupied house. Without those concerns, I'd of course prefer to do something with stucco, a gap for water, an external envelope around the whole house, some external foam, sheathing, insulation in the bays, etc. With all of that and some steps to increase solar heat gain in Winter, I could probably almost eliminate heating. With 7 people in the house, we produce a fair amount of heat without even trying.
In the earthquakes of the 1990's old stucco was found to fail under earthquake forces. To protect your investment against destruction in a normal expected earthquake. Tear off the stucco and put up shear panel and R15 fiberglass insulation in the 2x4 stud bays. Get an engineer to design where you need to do this. Then have a insulation contractor drill holes and dense pack cellulose into the empty stud bays where you don't replace the stucco.
Martin,
Having read the article, that is incredibly helpful I hadn't thought of using rigid insulation and spacing it to create an air gap between the stucco and the impermeable layer. That's so clever that it seems obvious now that someone who actually knows what they're doing has taken the time to explain it. Thank you so much for the information you share here.
Domenico,
I'm glad the article was helpful. Good luck with your project.