Siding and insulating a 1920’s house

We’ve been developing a best practices approach to the insulation and residing of our 1928 house. It’s a balloon frame, 1,500 sqf, 2 story, uninsulated kit house. What we have so far is based onthis exchangein a prior Q&A and learnings along the way. There is no broad access to the stud cavities. We have a few more questions before we can get started planning the work – looking forward to hearing your thoughts. Thanks to @DanaDorsett and @Akos for their responses to the last post. Here is the schedule and rational to date.
1)Seal everything that has penetrated the plaster and/or the sill in the basement, or the top plate in the attic and into the exterior wall cavities including anchors, electrical boxes, conduit, pipes via the walls, the baseboards. Hit the shoe molding and the picture hanging molding with calk.
2)Since our house has replacement windows we have to check to ensure that the window frame pockets that once held the counterbalances inside the original window frames are also filled and sealed.
3)At some point in their history our plaster walls have had alkyd paint applied, so we already have an interior vapor barrier and will check that off our list.
4)From the outside, cut holes in the tongue and groove sheathing and blow in dense-pack cellulose at 3 – 4lbs per cubic foot; need to determine if our walls can handle this pressure. Loose-fill is not an alternative because our house is balloon framed and any moisture would eventually force the insulation to settle leaving half of each continuous cavity uninsulated.
5)With dense-pack, the moisture will spread more uniformly across the cellulose and not accumulate at the bottom. This allows the system to dry out more quickly than any other insulation alternatives including fiberglass, rock wool, and foam.
6)Fill and seal the holes in the sheathing.
7)Install a new weather-resistant barrier.
8)Install prefab window casings/lintel/sills from Trim Solutions.
9)Install insulated clapboard vinyl siding. Nail only into studs so we don’t have to worry about puncturing the new WRB.
So far, so good, but we still have a questions…
1)What is the best way to ascertain if our walls can handle the 3-4 pounds of pressure from the dense pack?
2)Though we’ll do everything we can to prevent moisture from entering – when it does, how will it escape?
3)We plan on using close cell to insulate the sill plate, will that inhibit evaporation of any moisture that works it’s way down into the base of the walls?
4)We plan on bringing the attic into the conditioned space using closed-cell foam on the roof deck and down to the top plate and blocking the soffit. I assume that the top of a balloon frame house will have a significant hot air build up into the top of the stud cavities. Right now I’m sure that the house dissipates that heat rather freely. Will sealing at the top plate inhibit that hot air from escaping?
5)It seems that the choice of WRB is a very important component of this retrofit. Is there a proven, breathable Gore-Tex type available?
Thanks in advance for your views. – Jim.
GBA Detail Library
A collection of one thousand construction details organized by climate and house part
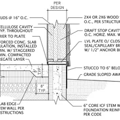
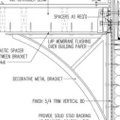
Replies
Add "test/improve with blower door" to the list. I'd use a fully adhered WRB membrane (eg, VP100). Vapor permeability will allow some drying.
thank you Jon. we do have a baseline so looking forward to seeing how we do against that. I read some more on GBA, looks like a spray applied WRB might make sense for us.
Would be interesting to see some data on adhered membranes vs spray on. Especially with the more challenging tongue and groove sheathing.
thanks Jon. yeah, what you say makes sense. I don't think we can afford to caulk and smooth out WRB across 3k square feet of t&g sheathing! If an adhered membrane will do the trick that sounds like the plan. I'm looking at Henry Blueskin VP100. Thank you!
Hi Jim,
I would suggest that you talk to a local professional installer about whether your walls can handle the dense pack cellulose. Make sure that they are willing to make any repairs if there were a blowout.
As far as drying, choose a vapor open WRB and your walls will have some drying potential in both directions. Better yet, choose a spray applied or fully-adhered WRB to reduce the chances of your walls getting wet in the first place and do a better job of air sealing.
I don't think you will have a problem with the spray foam in either location. The goal is to prevent convection from moving heat through the walls in the first place which you are working on by air sealing and insulating the walls. Spray foam at both plates will help with that.
勤于水资源管理outside and air sealing inside and out and your plan should go a long way in improving the comfort and efficiency of your home.
谢谢,布莱恩!希望通过热量上升the cavity and accumulating at the top plate will not create any unintended consequences. Other than that, it feels like we may be closing in on a solution that will work and that we can afford.
大多数石膏&板条墙从1920年代可以easily handle 3.5lb cellulose dense packing pressures, but any competent insulator would inspect first and make that call if it's marginal. Even where some sections of wall might be a bit marginal, they can often still be dense-packed with the aid of a 250 lb assistant leaning up against that wall with stud bay width sheet of plywood to support it while actively blowing.
Far more critical than insulating the sash weight pockets is air sealing them, and attending to any missing window flashing details.
+1 on Jon R's recommendation for a vapor permeable fully adhered membrane approach to the WRB, but be sure to lap it correctly with the window flashing since there will be ZERO drain space between the WRB & sheathing.
The drying rate through insulated vinyl clapboards is a tiny fraction of what it is with standard vinyl siding. The average R-value of insulated vinyl is going to be WELL under what would be called out for dew point control at the sheathing. It's' not clear that the slight increase in thermal performance will be worth the slight increase in moisture hazard that comes with the lower drying rate toward the exterior. A 1/4" mesh type rainscreen (eg Obdyke Rainslicker) would preserve drying toward the exterior and is enough of a capillary break to mitigate that moisturr risk without undercutting the thermal performance of the EPS loaded vinyl siding too mcuh, but I'm not sure if that would violate the siding manufacturer's installation instructions. Simple non-insulated vinyl siding and no mesh would be at least as good from a moisture point of view (and cheaper), albeit at the cost of slightly higher heating energy use.
Thanks Dana! We'll probably go with vinyl and Henry Blueskin VP100 for the WRB. If we end up being able to afford Cedar (doubtful) then we'll add the Obdyke Rainslicker, which looks like the perfect rainscreen. I can't thank you all enough for the info, exchange, and insights you brought to these questions. There are so many houses like ours that need help. Plaster lath on one side and t&g sheathing on the other. Hopefully, this exchange will help them too.