Mold from hell, now need to insulate properly

We had a black mold encounter in our gas fireplace bump out which lead to removing bricks to get to the soaked plywood and rotted osb. It has been removed and fixed and we currently have a empty hole in the wall to insulate before the direct vent gas fireplace goes back in. My question is how and what to use to insulate? we want to make sure everything is sealed for both air and moisture as the mold company feels the mold was caused from both the bump out roof having missing mortar and the builder not installing proper insulation / vapour barrier. To mention we live in Toronto and the winters are deadly cold. Any advice on insulating this properly would be appreciated , i would never want to have to go through this again. $$ and the pics below are the before and after of the mold we had, and the exterior side of that osb was completely shot.
GBA Detail Library
A collection of one thousand construction details organized by climate and house part
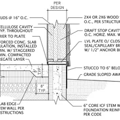
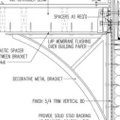
Replies
James, the best strategy here might be to take this opportunity to eliminate the bumpout. It's a vestigial fireplace, but as you've found it's also a nexus of envelope failure. That is to say, there is vulnerability to airsealing problems from the interior, continuity problems with the outside WRB, and insufficient insulation. The brick veneer also needs an effective air gap and durable flashing details. Without meticulous repair of ALL these, by contractors who understand modern energy codes, your mold will be back.
Hi Andy thankyou for responding, removing wont be an option. However we did have a metal cap installed with a water/ice shield, a much better option than before. We just have to concentrate on the inner side insulation now.
Hi James.
I agree with Andy. Bump outs and other twists and turns in the building footprint create opportunities for failure because they complicate control layer details. If builders are inexperienced with getting these things right, they become high risk areas.
And the same is true for cavities and flashing details for features like a fireplace, which often aren't insulated nor air sealed well.
That said, people want these details and are often unwilling to sacrifice them, which you may be.
One thing I can't tell for sure from the photo and we'll need to know to offer advice, is whether there is an adequate air space between the sheathing and the brick (and inch is good; more is better).
Hi Brian, reading the above comment we wouldnt be able to remove the gas fireplace and bump out . I did however check the air space between the sheathing and the brick and it is an inch. Any advice on how to insulate this space correctly to avoid any air leakages would be so helpful. Also just to show you we replaced the brick 45 degree angle with a Grace water /ice sheild on top of the 3 quarter inch plywood and then capped it with the metal roof with drip edges. The pic has uploaded the wrong way but you can see this the area we are most concerned about around the brick e.t.c
Hi James.
That's good news that you have a 1 inch air space and great that you are taking care of the water management issues. If the wall is not getting wet from rain or snow melt, the next most likely culprit is air movement through the assembly. So, you can fill the cavities completely with any type of insulation you choose, but more important even than the insulation is that you do a great job air sealing.
Before insulating, seal the bottom and top plates, all penetrations, etc. and make a plan to have an interior air barrier over the insulated stud bays. That could be a sheet good like OSB with taped seams, rigid foam, drywall, or a membrane (maybe dependent on the fireplace and clearances).
Unless you use a vapor-closed insulation like closed-cell spray foam, you will probably want a class II or variable perm vapor retarder in your cold climate (maybe your code calls for something specific). Depending on the product, this may be able to be your air barrier as well.
Once you have controlled water, air, and vapor properly in the bump-out walls, it's probably a good idea to make sure the cavity between the back of the fireplace and the bumpout walls is not creating a thermal bypass allowing air from whatever area is below (if it is an unconditioned space) to get into conditioned space; or allowing conditioned air from that space a path to unconditioned space above (if that's the case). Basically, try to seal up that area too.
Brian, thankyou very much for all your great advice. I will make sure this is carefully and properly done.
Brian, sorry just one more thing.. any suggestions how I should seal these big holes on the interior side of the osb that the builder did? Thought maybe they need to be sealed before I insulate that wall cavity. Thanks again.
James,
There is no benefit to sealing the holes. You can put some of that red tuck-tape over them if you want, but would be entirely cosmetic.
Even if the hole is letting in air?
James,
You need to decide where your air-barrier is going to be and make it continuous. That is really important to stop your problem coming back again.
If it is the exterior sheathing you would need to seal every stud-bay and seam on the OSB, not just the holes.
If like most houses in Canada, it is poly on the inside of the wall, that needs to be detailed so it is continuous with the existing walls and sealed at the perimeter.
Thankyou Malcolm.