AC register condensation: Not enough ridge for adequate ridge ventilation?

I’m living in the Houston area (zone 2) and noticed water leaking from some AC registers yesterday. The home is 9 years old, 300 sq ft.
The flexible ductwork is insulated.
The register boots are insulated, and the insulation has a lot of mold. (pic attached)
有明显的水在阁楼上the blown in insulation around the duct boots: not damp, really wet.
I do not think the register boots are leaking, but I guess they could have small leaks.
Morning humidity is currently around 92%, according to NOAA. Attic humidity was 60% at 8AM today, when outdoor humidity was around 90. (I don’t have extremely accurate measurement tools, just a cheap $15 portable unit ).
My suspicion is the root problem is with inadequate attic ventilation. Attic in the original 3000 sq foot house is unconditioned, blown in fiberglass. There are continuous soffit vents (looks like pegboard, I think it is a Hardie product) around the permitter of the house, but due to the roof design (pic attached), there is one main 10′ ridge vent and secondary 8′ and 4′ ridge vents. I estimated about 400 sq in of roof ridge vent, and think I need probably 3 times that amount.
I would like your help to
(1) confirm that my problem is poor attic ventilation, and then
(2) find need a solution.
My understanding is I would need a dozen or more turbine vents to add 1000 sq inches of ventilation. Also I understand that mixing powered roof vents with ridge vents is problematic. I don’t really have room to put 10 turbine vents at the peak of the roof, which is only about 10′ wide, so…
maybe a couple solar powered roof vents would be practical in this particular situation.
Another note, we recently added 2000 sq feet to the main house. There is very little communication between the two unconditioned attics, basically just an 18″ * 72″ cutout in the old roof to allow walking between attics. The new addition has about 50-60′ of ridge vent.
GBA Detail Library
A collection of one thousand construction details organized by climate and house part
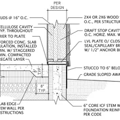
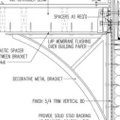
Replies
Mark,
Your problem has nothing to do with attic ventilation. If anything, increasing the rate of attic ventilation could make the problem worse, not better.
The source of the moisture is exterior air (which in Houston is hot and humid, especially at this time of year). The crux of the problem is that your attic air -- which like the outdoor air, is hot and humid -- is able to contact cold surfaces, leading to condensation.
The solution is to create an air barrier -- specifically, an air barrier with a decent R-value -- to separate the humid attic air from the cold components of your air conditioning system (the duct boot, register, and nearby drywall).
Locate the air leaks and cracks near these areas and seal the air leaks (as well as the entire exterior side of your duct boot) with closed-cell two-component spray polyurethane foam. That will solve your problem.
What he said- the duct boots are much colder than the dew point of the outdoor air. If the insulation at the duct boots is air and water-vapor permeable (any fiber insulation), water from the attic air will condense on it, just as a cool beverage bottle will collect moisture on it when exposed to humid air, but not in the dry air of the refrigerator.
Increasing the amount of ventilation to the attic won't make it better, but could make it worse.
As a general rule vented attics in the gulf coast region in air conditioned houses will have higher moisture content to the structural wood than sealed attics. But sealing off an attic with the ducts & air handler above the insulation results in somewhat higher peak attic temperatures and sometimes higher cooling loads, even though the humidity level goes down. There are lots of factors to consider here before making any big changes, but I'd be inclined to seal up the attic, (which also improves it's roof retention performance in a hurricane.)
更多背景发泄阁楼与未放气的in your climate see:
http://www.fsec.ucf.edu/en/publications/pdf/FSEC-CR-1496-05.pdf
Thank you Martin and Dana.
Since my ducts and boot's were insulated and there were no obvious leaks, I assumed the problem was the attic air, but your answer makes sense, it is still more humid outside (9x% this morning) than in my attic.
- Do you have any recommendations for DIY 2-part closed cell foam solution?
The stuff I found online was fairly expensive, like $700 for two tanks. There was a smaller solution for $54, two small cans that only deliver 1.25 cu foot expanded. I have about 15-20 registers to treat.
- How thick should the foam be around the register boots? 2"? 3"?
I am also a little concerned about expanding foam distorting the register boots. Some of the boots I've examined are wedged between ceiling joists with a very thin (almost nonexistent) gap, That gap I assume needs to be filled/sealed also.
- Perhaps I should caulk between the two boot sides and the ceiling joists with some suitable caulking, or low expanding foam sealer? And then foam the two exposed sides and top of the register boots?
My last dilemma is how to dry out the drywall and boots before sealing. I guess I need to remove the wet insulation and then maybe turn off the AC for a day, or turn it up to 85???. It might takes days for those little cracks between the register boots and the ceiling joist to dry out.
Thanks again for your great support.
Thanks Dana for the reference article. I read the first 8 pages, then my brain overloaded. Still, it was interesting to see some of the conventional code wisdom being challenged and tested.
When you said 'I'd be inclined to seal the attic', are you suggesting sealing my current unconditioned attic by closing up the soffit and ridge vents, and leaving the attic unconditioned? And I presume this suggestion is due to the high humidity in Houston?
Mark,
All of the damp insulation needs to be removed and thrown away. You need to expose the duct boots, the back of the drywall, and any unsealed duct seams.
Here are links to two sources for spray foam kits:
http://www.betterenergystore.com/productpage.asp?p=4
http://www.jrproductsinc.com/shop/pc/16lb-Polyurethane-Foam-Kit-With-Accessories-15p48.htm
If you don't want to spend $600, you can start with a $104 investment for a smaller kit, and then graduate to a larger kit (or another small kit) after you gain experience and assess the size of your job.
If all of this is daunting, you can try to find a weatherization contractor or a spray foam contractor to perform the work.
Two inches of spray foam should be enough to solve the problems you describe.
Once the spray foam has cured, you can go ahead and install R-49 of new blown-in insulation on top of the sealed register boots. Green builders usually install cellulose insulation on attic floors, but blown-in fiberglass will also work.
Dana's reference to "sealing the attic" referred to the possibility that you might want to convert your vented unconditioned attic into an unvented conditioned attic. For more information on this work, seeCreating a Conditioned Attic.
Even without moving the insulation to the roof deck, sealing an attic can have a beneficial effect on moisture levels in a location as humid as Houston. (The opposite is true in places as cool in Chicago or Boston, but there are MANY existence proofs of unvented attics with the insulation at the attic floor surviving the test of time in those cooler locations.) With an attic air-tigtht to the exterior the dew point of the attic air will eventually fall to that of the conditioned space below.
When making such a change it's important to monitor the humidity of the attic air for awhile. It takes time for materials in the attic to dry toward the fully air-conditioned rooms below through the ceiling paint, and a room dehumidifier in the attic might be needed to help it out after the cooling season has ebbed.
Thank you again Martin and Dana. I now have a plan to execute.
A last question if you have time: The mold/mildew seems to be confined to the interior of the register boots, and along the perimeter of the boot/drywall junction in the conditioned space. I will reconfirm this today with better attic lighting.
Assuming there is no mold/mildew on the attic side of the boots, can the closed cell foam be applied to damp boots/drywall, or do we need to thoroughly dry the attic side before applying the foam? Drying the attic would probably require shutting down the AC, probably for a few days, in this 95F heat. Thoroughly drying the drywall might require a hair dryer...
Martin, the second product you referenced (jrproductsinc.com/shop/pc/16lb-Polyurethane-Foam-Kit-With-Acc...) appears to be 1-component polyurethane foam.
My understanding was that these 1-component poly kits were designed more for sealing (beads) rather than area coverage. Granted the register boots are a smaller area.
Is 1-component poly a suitable long-term solution for insulating the attic side of register boots?
If so, there are many DIY products in this space, and the requirements for PPE seem to make it safer.
Mark,
In your original post, you wrote, "There is significant water in the attic on the blown-in insulation around the duct boots: not damp, really wet."
That sounds like water accumulating on the attic side of the register boot.
Then, in one of your more recent comments, you wrote, "The mold/mildew seems to be confined to the interior of the register boots, and along the perimeter of the boot/drywall junction in the conditioned space."
So which is it?
Mark,
For your application, one-component foam will work, although two-component is probably better (because it may be less vapor-permeable).
Note that one-component foam cures by combining with atmospheric moisture -- meaning that it's fine to install one-component foam on damp surfaces. The moisture will actually contribute to the curing of the foam.
With two-component foam, a dry surface is preferable -- so turn off the AC before working on the register boots, and dry everything down with paper towels.
Check out foam kits at your local lumberyard or Home Depot -- you may be able to buy a two-component spray foam kit in a size that is smaller than the $600 to $700 kits.
Thanks again Martin.
I bagged the wet insulation around 4 register boots, at varying distances from the central AC unit. On the attic side, around the boots closest to the AC unit there is considerable condensation around the boots, on the drywall surface, and particularly the last inch of the insulated flex ducts were saturated with water (think like a sponge pulled out of a bucket of water). Registers farther from the main AC unit are damp, but not as wet as those closer, which I guess could be explained by a reduction in the cold air temp as it travels further in the unconditioned attic.
flex导管连接到靴子和领带s (no tape or mastic), so I suspect there is significant air leakage around these connections, perhaps explaining why the duct insulation is saturated at this junction.
However, there was no visible evidence of mold/mildew on the attic side of the register boots.
Removing the registers inside the house, there is mold or mildew on the registers, on the drywall, and on the insulation inside the register boots. I don't have the skills to distinguish between mold and mildew.
There is also condensation accumulated at the four plenums in the ductwork system. Again, the ducts are connected to the plenums with ties, no tape or mastic. The same connection type used at the register boots.
I guess I'll eventually need to open up all the plenum and inspect for mold/mildew.
I presume the best solution for my problem is to put the attic inside the conditioned space, but that will require replacing the gas heat and gas hot water heater, vacuuming out the blown in fiberglass,... Seems like an expensive proposition, maybe $20-$30K,...
I've attached some additional pics showing the register boots and plenum.
Re #6, given the cost advantage and reduced area of attic floor cellulose, it would be interesting to see more analysis of hot climate attics where the floor is the thermal boundary, the roof is the humidity boundary and, I assume, both are air boundaries.
Mark,
It sounds like the moisture formed on the attic side of the register boots, and that the water dripped down to soak the drywall at the edge of the boot. The moisture also wicked into the insulation near the register boot.
Whether or not mold is visible depends on food supply for the mold. The paper facing of the drywall is an excellent food for mold.
Thanks everyone.