任何问题使用2英寸XPS发泡to insulate basement rim joists if I also have polyiso foam on the outside under my siding?

Gre Finn| Posted inEnergy Efficiency and Durabilityon
I am in climate zone 5, southern ontario.
GBA Detail Library
A collection of one thousand construction details organized by climate and house part
Search and download construction details
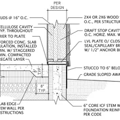
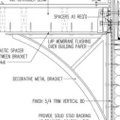
Replies
Gre,
The brief answer is, "Probably not."
The longer answer depends in part on your providing a few more details.
How thick is the exterior polyiso? If it is at least 3 inches thick, you can insulate the interior side of the rim joist with fluffy air-permeable insulation if you want (fiberglass or mineral wool), increasing the chance that the rim joist will be able to dry to the interior.
Is there a capillary break (for example, closed-cell sill seal) between the top of your foundation and the mudsill or rim joist? If there is, that would be good, because it would reduce the chance that the rim joist will get damp due to capillary rise from the foundation wall.
If you have a good capillary break, the rim joist should stay pretty dry, and I wouldn't worry too much. The thicker the exterior poly, the better -- and the more options you have on the type of interior insulation you can choose.
the product on the exterior under my siding is Atlas EnergyShield and it's only 1 inch thick. R6.5. It's used a lot around the neighborhood under siding. My house was built in the 70s, I see no sill gasket under the sill plate. Currently the rim joists and sill plate look very clean and dry. My issue would be a double vapour barrier between the exterior foam and the interior xps causing moisture to get trapped.
The renovator and the company selling the product tell me there is no issues but not quite sure
The mid-winter performance of R6.5 polyiso with R10 XPS on the interior side will be well below it's labeled R. In climate zone 5 it'll be between R4.5-R5 in January but that it still sufficient dew point control for R10 of insulation on the interior side of the band joist.
At 2" most XPS will meet Canadian code definitions of "vapour barrier", but in fact would run at worst about 0.5 perms, an order of magnitude or more higher drying rate than the foil-faced polyiso on the exterior.
As long as the foundation itself has sufficient drying and good drainage it will be fine to insulate the band joist & sill with XPS. But if you used unfaced EPS you'd have at least twice the drying rate. If & when you insulate the foundation, insulate the exterior side with foam down to a half meter or more below grade. Use only rock wool on the interior side down to the same level, and NO interior side polyethylene, to ensure that any moisture wicking up the foundation dries to the interior. Exterior foam on the above-grade foundation protects it from direct rain-wetting and dew, but inhibits drying toward the exterior, which is fine for the foundation sill as long as the foundation can still dry toward the interior. With 1.5" of exterior EPS or XPS there is sufficient dew point control for up to R15 of interior-side rock wool before the foundation would be taking on moisture from the interior room air. Finishing the exterior foam with a cementicious EIFS such as QuiKrete Foam Coating preserves at least a bit of exterior drying capacity. If a code inspector insists on seeing interior side plastic sheeting, use 2-mil nylon (Certainteed MemBrain), which meets the Canadian code definition of vapour retarder when the air is dry (as it will be in winter), but becomes vapor open when the moisture levels are high enough to support mold growth. You don't really need it as long as you have 1.5" of foam on the above-grade exterior, but it is a FAR safer solution to the code-official problem than 4 or 6 mil polyethylene.
I guess my other concern is the polyiso under my siding with the interior poly vapour barrier. Not sure why they are using polyiso for residing when homes in our area all have interior vapour barriers. Any tips on lessening the risks. Should I cut into the wall cavity to examine.
Gre,
To lessen the risks that occur when rigid foam is added on the exterior side of the wall sheathing on an older house with interior polyethylene, make sure that the rigid foam is thick enough to keep the wall sheathing above the dew point during the winter.
For more information, seeCalculating the Minimum Thickness of Rigid Foam Sheathing.
In your case, though, I wouldn't worry unless you have symptoms of problems.
In zone 5 an inch of polyiso is sufficient dew point control for a 2x4 wall, but it is indeed a moisture trap if there is polyethylene sheeting on the interior side. It would be better to insulate those homes with 1.5"/R6.3 of unfaced 1.5lb density "Type-II" EPS, which has better wintertime thermal performance than R6.5 polyiso in that stackup & climate, and a vapor retardency more than 1-perm. Better still would be 1.5"/R6 of rigid rock wool, which is over 25 perms.
The biggest risks with moisture traps in walls are from bulk water incursions at windows & doors or at roof to wall transitions which then take forever to dry. If the window flashing is in good shape (and there are decent depth to the roof overhangs), and roof ice damming issues are well managed the risks are pretty low. It's not worth tearing into the wall to investigate unless there's reason to suspect there's an actual problem.
If there are issues would installing a smart vapour barrier under the drywall help, if I am by code allowed in Ontario...
Gre,
Stop worrying. If it helps comfort you, read this recent article by Joe Lstiburek:Doubling Down—How Come Double Vapor Barriers Work?
In that article, Lstiburek writes a sentence that is a little confusing, because you have to wait for the verb at the end of the sentence (as in German) to understand what Lstiburek is saying. Anyway, here is the sentence: "Houses with foam sheathing in cold climates with interior vapor barriers with good interior air sealing that are not humidified and pressurized to hospital and art gallery performance metrics work. ... For the record I do not have heartburn with interior vapor barriers in cold climates. Nor should all of you. But I do have heartburn with interior vapor barriers in hot climates and mixed climates and pretty much any place with lots of air conditioning."
In new construction or a gut rehab a smart vapor retarder would still be preferable to 6 mil polyethylene, but not necessary if there's an inch of foam on the exterior.
一般建2 x6墙与Fi R5泡沫gure 4 of Lstiburek's article has a vapor permeance of about 1 or a bit higher more than an order of magnitude higher than foil faced polyiso. The arrows in Figure 6 implies that the reason it works is the air leakage to the exterior as the drying mechanism. I'm skeptical that it's in fact the drying path to the exterior is in fact air leakage rather than vapor diffusion through the 1-perm+ foam being high enough to tolerate at least some interior side leakage. A 2x6 + R5 wall would be a code violation in climate zone 6 or higher without the interior vapor retarder, but 1-perm foam is "good enough" drying capacity toward the exterior, unless there is bulk water leakage into the wall cavity.
Either way, a smart vapor retarder is more resilient than a poly vapor barrier. As Lstiburek notes in the paragraph below figure 9:
"With this approach we only have a “double vapor barrier” during the winter – we don’t have one during the summer."
In the grand scheme of things the upcharge for MemBrain vs. 6 mil polyethylene is cheap insurance.