Best way to insulate a rowhouse flatroof one room at a time

你好,马丁,谢谢你所有的好information everyone has made available as I have found much f it to be quite informative, and possibly saved my roof from the idiot mistake of almost dense packing cellulose in the 14″ cavity between my plaster and lathe ceiling and my roof.
My question is, as a new first time homeowner, I am trying to rehab each room in the house, room by room in the interest of being able to live here while doing so, which in turn means as I near the end of the room I am currently working on (the first one) I will only have sprayed CCSF on the underside of the roof sheathing in a 9’x 13′ area of a roof that is 18’x40′. The room I am finishing, is right next to the bathroom that has no exhaust vent (yet), and is at the low point of the roof. Further complicating matters, there is a chimney remaining from an old wood burning stove (true for all three bedrooms on the 2nd floor) that needs to be, and will be removed when I can afford to re-roof the house (the current roof is in moderate, at best condition and almost 30 years old).
The plan:
I have framed the closet to surround the chimney on the two exposed sides in the room, the 3rd side is to the exterior wall, and the 4the side will be accessible by removing the plaster from outside of the room in the hallway in order to remove the remainder of the chimney and turn that void into another closet. It is clear that at some point there was rainwater entry here from a failed seal around the chimney.
The cavity between plaster and lathe and the roof sheathing in the rest of the house will remain untouched for the next few months, and the only other thing I will do shortly is install the bathroom exhaust, as there is no exhaust system in the house, and the cavity b/w the ceiling and roof is un-vented. The balance of the ceiling is FAR from air tight as it consists of collapsed plaster (from what appears to be a leak about 15-20 yrs ago) covered by drop tiles (first timer lessons, thank my inspector.)
Currently it is a hot roof (likely multiple ones layered) onto what appears to be galvanized sheets (I can only observe what is visible between the planks) onto planking secured to joists on 26″ centers.
I intend to apply 2″ of CCSF to the sheathing in this room only (for now), apply drywall, and then dense pack with about 12″ of cellulose, with the exception of the void surrounding the chimney which is surrounded with 1.5″ rigid board, sealed with OCSF, with a plastic sheeting vapor barrier on the inside of the studwall (b/w the wall and the chimney), and dry wall between the studwall and the rooms “conditioned space”
I’m sure many are cringing already, but the house was built in 1890 and is my problem to solve for likely the next 30 years so I’m going to do the best I can with it.
I do intend to put on a new roof in the next year or so when I get back on my feet, and will likely do an additional 2″ of rigid foam in between the roof sheathing and a rubber membrane. I hope to address the ceilings/ underside of roof sheathing with the exception of chimney voids to be dealt with post roof) about one room every 2-3 months ( so should be able to complete the ceiling/ inside insulation by June 2014.
我想与你确认significantly more experienced and knowledgeable then I that I am on the right track, and not about to do something that is going to cause a structural failure in the roof 5 years down the road. I wish I could hire a pro, but honestly my resources are in a manner that I can either do nothing and continue to heat and cool (or be incredibly uncomfortable) the city of Philadelphia, or roll up my sleeves and do the work myself. While I have experience as a carpenter, I certainly am in foreign territory when it comes to energy efficiency, dew points and the like.
Hope to add a plan view dwg and center section dwg along with some pictures to this post, but just cant do so right now.
Hope everyone has a good holiday.
GBA Detail Library
A collection of one thousand construction details organized by climate and house part
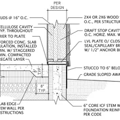
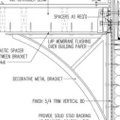
Replies
Even though your 2" cc foam + 12" cellulose will work, it doesn't meet the letter of IRC code without an interior side vapor retarder, unless you also add the exterior rigid. Philly is in climate zone 4A, where code prescribes R15 for the foam between the fiber and the roof deck:
http://publicecodes.cyberregs.com/icod/irc/2012/icod_irc_2012_8_sec006.htm
But the code prescription for under-deck foam-R is demonstrably wrong on this one- it doesn't really need it- even 1" of closed cell would be sufficient protection in your climate. See Table 3:http://www.buildingscience.com/documents/bareports/ba-1001-moisture-safe-unvented-wood-roof-systems
Closed cell foam in small installations is quite expensive, but can be a reasonable DIY using the kits (Tiger-Foam/Fomo-Foam, etc.) But at better than buck a square foot per inch of thickness, going with more than the minimum necessary gets expensive. A couple of 600 board-foot kits would be enough to handle the whole 18 x 40' at 2" thickness, at a material cost of about $1500. Since you're doing it a room at a time starting with a single kit keeps the cash flow bounded. (It is more expensive to go with kits smaller than 600 board feet, and you would need at least that much at 1".) To do a single ~120' room at 2" a pro would have to about a charge a grand just to show up to cover the road time and tying up the rig for that time, just to squirt a couple hundred board feet. That much foam would be about $250 if incorporated into a bigger job, but the set up and break down time and road time is the same whether they are installing 10 board feet of foam or 10,000 board feet. Time is money, and since you have more time than money, the DIY approach is recommended. (Read the installation literature carefully- you don't want to screw it up. There is no rocket science, but you need to pay attention to both the roof deck temperature and the temp of the foam tanks to get consistent results.)
Similarly, dense packing it a room at a time with a pro can get expensive, but with an inch or two of closed cell on the roof deck, even 2.5-3lbs density is going to be fine in your climate, and with practice you can get there with a single-stage rental blower. Most box stores will throw in a day's worth of rental when you buy at least $100 worth of cellulose, and at 2.5lbs density you're looking at more than $125 in cellulose that just for your 9x13 room.
You don't need the plastic vapor retarder on your flue chase and it may even cause moisture problems. If it isn't too late, take it out.
You need a minimum of 2" of free-air clearance between the flue and combustibles, but you are allowed to put sheet-metal air barriers in where it penetrates floors (recommended). You can air-seal those air barriers with furnace cement.
Frank,
You're on the right track. Aim for 2 inches of spray foam below the roof deck, and at least 2 inches of rigid foam above the roof deck soon, and everything will probably work out for you. Demolishing the chimney is an excellent idea.