Cellulose insulation in raised/exposed floor system

Hello, I know this topic has been beaten to death already, and I have done a lot of reading and talked to some other local builders, but am still uncertain of the best way to proceed. Here’s my situation…
我建立一个12×20小屋在码头上。我在northern NY state. The cabin will be heated, and used intermittently throughout the year. I am aware of local building code and not trying to meet R-value requirements. The floor is framed. I will be using Advantech on top of the 2×8 joists. I have between about 18″ and 4′ of clearance under the cabin, enough to work, though I’d like to do the majority of the insulating form the top. I want to insulate the floor to a certain extent, but being that it will never be heated all winter long and is only used intermittently I am not concerned with getting the highest possible R-value. I am more concerned with managing moisture, rodents, and doing so economically. For now, it will remain open underneath with plenty of airflow. I may eventually add skirting but not likely any time soon.
I have some 2″ felt faced polyiso and can acquire more cheaply. Initially, this is what I was going to use, but I am concerned with having to take additional steps to rodent proof it. I’m also a little concerned about moisture from underneath, as the fabric facing isn’t really a vapor barrier. I recently talked to a friend who has a cellulose blower and can acquire cellulose at a good price, and I am leaning toward this. With this option, rodents and moisture are my main concerns.
Here is my question…
If I were to use some sort of sheathing attached to the underside of the joists, say 1/2″ plywood, or maybe 7/16″ OSB, or, possibly treated Plywood as one corner is about 18″ or less off the ground, fill the joist bays with blown in cellulose, and put down Advantech subfloor, will I encounter moisture issues due to condensation, and where would that condensation most likely form? And if I do this, should I take steps to make sure this floor box is air tight? i.e. tape/caulk seams of the sheathing under the joists etc. I had thought of using a 1″ layer of foil faced polyiso under the joists, but it adds cost and I’m not too concerned about the amount of thermal bridging I will have or the gain in R-value. It would also add a vapor barrier on the cold side, and I’m not sure if that’s a good thing. I will likely use some sort of hardwood flooring on the Advantech.
I have been very impressed with the wealth of knowledge on this form. Any opinions or suggestions would be appreciated!
Ben
GBA Detail Library
A collection of one thousand construction details organized by climate and house part
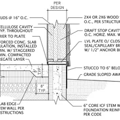
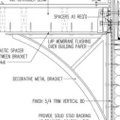
Replies
Ben,
Your plan will work fine from a moisture perspective. The Advantech will work as an effective air/vapour barrier as long as y0u seal any penetrations for services. I think you will find the floor cold in Northern NY, and if it were me I'd add a 1 1/2" of EPS under the joists and then cover it with plywood, but if you don't mind wearing thick socks in the colder months the assembly works fine as you have described it.
Malcolm,
Thanks for your thoughts. I think it's going to work out well. I am considering adding a layer of foam under the joists like you said. It will probably have to be interrupted where there are support beams, but will still help. I mostly wanted to confirm that it should not be a problem to have what is effectively an impermeable layer on both sides of the cellulose. Also still deciding on the plywood for under the joists/foam. I'm leaning towards regular 1/2" CDX as I think there is enough airflow under it to mitigate any issue with moisture from below. Any more input is welcomed. Thanks again.
Ben,
i've always used plywood on the underside of similar floors here in the wet PNW without problems.