Certainteed Membrain / basement build.
I am in the process of completing a previously uninsulated / incomplete basement.
My question is in regards to the use of Certainteed Membrain on the inner basement layer.
House is in Chicago Area, hence Zone 5.
House is vinyl sided above the poured foundation, extending down to the rim joist interface.
Basement is poured concrete, built in 2003.
No cracks and no water or vapor infiltration from the time we moved in (plastic sheet / tape test over 1 week – stayed dry).
Outside is waterproofed, and has a french drain that encircles the full perimeter, with compacted gravel bed below the slab itself.
Sealed sump pit (Radon sealed), with 2 sump pumps, 1 1in higher than the first.
To date, the wall structure has been built out such that now, 2in XPS 150 panels are glued (compatible foam glue) to the inner side of the concrete, and taped (compatible 3in foam tape).
The rim joist was emptied of the existing pink fiber + stapled plastic (builder grade), and replaced with 4in XPS 150, sealed in with sprayfoam.
All framing gaps where air infiltration could occur were sealed with acoustical sealant.
6mil plastic sheet on the floor (fully taped at seams), with the sheet being taped up to the wall XPS assembly (6in overlap from floor to wall intersection), then 1in 250 panels covering the full slab (with compatible 3in foam tape joining this assembly), and covered in Advantech floor sheeting.
Wall assembly built out with 2x4s, 16oc (pine). Cavities to be filled with Rockwool (R15).
This gives a full assembly R value of R25 for the full wall, and R35 to R40 at the rim joist, continuous thermal break owing to the foam encirclement.
Finally, the basement was previously unheated. It will now have forced air made live, and localized hydronic heat via an HTP air handler to an HTP Phoenix Light Duty, for basement only auxiliary heat. The house itself is also actively humidified via the forced air system.
My question, before drywall goes on. Should a product like Certainteed Membrain be applied to the inside of the outer facing foundation walls?
I am trying to avoid a double vapor barrier disaster.
However, unsure if the ‘breathability’ claims of the Mambrain product negate this concern.
The moisture sealing claims are interesting, in that i’d like to prevent moist inner air from getting near any cold / condensing surfaces.
GBA Detail Library
A collection of one thousand construction details organized by climate and house part
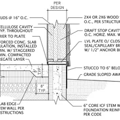
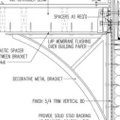
Replies
In your climate zone, with a labeled R10 (R8.4 at full depletion of it's climate damaging HFC blowing agents) you have plenty of dew point margin on R15 fiber insulation to be able to skip the MemBrain or any vapor retarder tighter than standard interior latex paint.
In secion R702.7.1 the IRC calls out R5 minimum in zone 5 for fully above-grade 2x4/R13 fiber insulated studwall to be able to use Class-III vapor retarders.:
https://up.codes/viewer/connecticut/irc-2015/chapter/7/wall-covering#R702.7.1
In a basement only the above-grade portions of the wall would need that much, foam-R, but it's fine for it to extend fully down to the slab. You have R8.4 (fully derated), which is proportionally high enough to satisfy dew point issues with R15 rather than R13 in the cavities with margin to spare. (R5 x R15/R13= R5.8)
For the band joist area, same thing only more so. With R16.8 (fully derated) foam it's WAY over the minimum amount necessary.
It's unfortunate that you have already sprung for the more expensive (environmentally & financially) XPS solution. XPS is is by far the LEAST GREEN insulating material in common use in the US due to the HFC blowing agents used. It does nearly 10x the damage that EPS or 1lbs density foil faced polyiso delivers, either of which would have been a cheaper & greener choice:
https://materialspalette.org/wp-content/uploads/2018/08/CSMP-Insulation_090919-01.png
The labeled R5/inch is only temporary. At 20 years XPS is only warranteed to R4.5/inch as the HFCs slowly diffuse out. At full depletion it's performance is only R4.2/inch, the same as EPS of similar density. EPS is blown with low impact hydrocarbons, not HFCs (as is polyiso), most of which escapes the foam at the factory where it is recovered, not vented to the atmosphere.
>"The house itself is also actively humidified via the forced air system."
Active humidification is a generally BAD idea, unless you have extremely high ventilation or infiltration rates. The dew point of reasonably human-healthy and comfortable 30-35%RH/70F air is 37F-41F. While R5 on the exterior of the fiber insulation is adequate to keep the average temp at the foam/fiber boundary high enough to use latex paint as the interior side vapor retarder, keeping it in that range during the coldest months is important.
While some people would love it to be 50%RH in the dead of winter, the dew point of 50%RH/70F air is 50F, which would require a LOT more foam or a much tighter vapor retarder than latex on wallboard. If you intend to keep it 50% RH @ 70F all winter you'd need something as tight as Intello Plus, not MemBrain.
Many thanks for verifying that I could skip the Membrain product with my current configuration.
Regarding the XPS, the decision of this product over EPS, or even PolyIso, really was driven by the products rated permeability, and behavior with respect to moisture. Being a below grade basement with a water laden cast concrete, my fear was once the foam encapsulation occurred, I wanted to be certain that moisture transmission loop created, anything towards the inside be kept to a minimum, if not eliminated wholly.
Having been in too many basements where the dank / musty odor of misdirected moisture was always present, this really was a selling point on the XPS, vs. the other 2 available products. Hopefully once all is completed, the final net saving in dramatically lessened heating cost (Nat Gas) will eventually offset the HFC blowing agent sublimation impact.
Humidification stays between 32 to 40%RH, so minimal but still a variable that I had to take into account.