Concrete-Free Slab for Garage

With the greener building practices turning up around concrete-free slabs, I have not found anything around using the same practice for a detached garage.
To be clear (and if you’re not familiar), I’m referring to a general floor assembly of crushed/compacted rock, then foam, then poly, then staggered sheets of plywood subfloor.
The immediate concerns that come to mind are:
– the finish layer: what would you lay on top of the plywood to protect it from the elements? tile? epoxy?
– the compressive strength of the foam and plywood: would it hold up with a vehicle driving and parking on it?
– garage door transition: would you use the same one you’d use for any other door opening?
What do you think?
GBA Detail Library
A collection of one thousand construction details organized by climate and house part
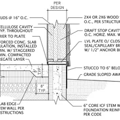
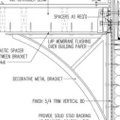
Replies
I don't think you can as wood won't meet non-combustible requirement unless you get expensive wood. At that point, might as well pay for the concrete.
You also have a pretty large point load you have to deal with, works out to around 100PSI, which is well above the capacity of most rigid insulation.
具体蝉联年代也有助于此preads the point load out a fair bit. You can do the same thing with wood by adding more layers, but now you are adding even more of the expensive fire rated wood.
I think concrete free detail is best left for houses.
Excellent points. I hadn't thought of non-combustible requirements.
obenwalkenobi,
Not a particularly good alternative, but maybe consider pavers instead - much as you would use on a driveway? However I have no idea how their embodied carbon compares to a slab.
As the alternatives represent such compromises, for the small amount of concrete used in a garage, perhaps the best strategy is to offset the carbon footprint in other ways.
Pavers at least are reusable and can be taken up and put back for repairs. Concrete is single use. So it's not quite a fair comparison.
I wanted to try pavers for a garage, the issue I ran into was they were quite expensive.
Pavers are definitely one alternative. And as pointed out, reusability/repair is one benefit.
But due to higher cost, questionable embodied carbon savings (if any), and loss of a smooth, easily sealable surface, this alternative is less attractive than just sticking with concrete.
You also need to consider the impact of both flammable and non-flammable liquids. Garage slabs are pitched to the door for this reason. Consider what would happen if gasoline spilled and soaked your floor sandwich. Or pesticides. Or just the constant dripping of meltwater from the vehicles. Go with concrete here and save carbon elsewhere.
I guess I think of concrete as porous - so it would need to be sealed to prevent gasoline and other liquids from soaking into it as well, right? If I can seal concrete, why not other surfaces?
If we're not sealing the concrete, then we're in the same categorical design as the gravel / paver routes in my mind.
There is many a garage out there with no finished floor, just compacted gravel/stone.
Many basements in this area from the 1800's are floored with pavers.
It's a bad idea for a multitude of reasons.
What is, pavers or no floor?