Compacting Slab Substrate

I am building a shop on a slab in 4a.
Does the 4″ layer of 3/4″ base rock need to be compacted or is it self compacting and just needs to be raked level?
Since I am doing all the prep and will have a pro do the pour and finish, I don’t want to rent a plate compactor if it is superfluous. Do I just rake it all very level, or do I need to run a plate compactor?
Thank you.
-Mike
GBA Detail Library
A collection of one thousand construction details organized by climate and house part
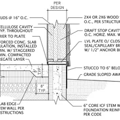
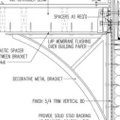
Replies
Hi Mike,
To my knowledge, the only gravel considered truly self-compacting is pea gravel. I think you'd be better off running a plate compactor if you don't want to run the risk of settlement and water accumulation at the foundation. When I was in landscape contracting, we compacted every substrate--even those they didn't have the potential problems associated with a slab. But I look forward to hearing what others have to say.
Thanks Kiley. If it will ad to the benefit, I will compact it then. Hoped to save the change, but it is pretty cheap to rent one for a day, so I can get everything level and in position and then run the compactor for a few hours to ensure it is a pretty good practice.
When compacting soils more is always better but it takes time and that costs money.
“Self compacting” turns out to be about 80% true.
Generally if you are spreading 4-12 inches ¾ inch clean crushed stone on undisturbed soil that is about as good as you are likely to get for residential construction.
https://ucononline.com/magazine/2016/february-2016-vol-71-no-2/features/self-compacting-soils
Walta
Thanks Walta. I read that article and that looks like a lot more void around a pipe vs the 4" level base. What you say makes sense.
Do you need a little additional bearing capacity? Do you care if the curing slab can't easily move sideways and this increases the chances of cracks?
Jon, Are you saying that running the4" layer of 3/4 washed under a plate compactor will provide these two benefits?
Some, yes. But how much and if you care are important.
When you "compact" #57 stone, you are not really compacting the stone, but rather driving the bottom of your stone layer into the substrate if it is not already so tight that it won't take the stone. One way this is sometimes done is if you can get a loaded dump truck to drive back and forth over it. It is called proof rolling. If the soil does not move under the tires, the subgrade is compacted. At that point you can put the #57 stone over your compacted subgrade.
If instead of #57 stone, you are using crusher run, which had many fines mixed with the larger stones, you can easily have voids and it needs to be compacted.
My subgrade is really well compacted from dump truck rolling over it a bunch and from dozer too, plus settling for 8 months.
For whatever it's worth, our 3/4 stone base was thoroughly compacted. On top was 4" of reclaimed foam. Slab was finish floor and we didn't want any cracks. Plenty of control joints. No cracks.
Hi Stephen, I was just reading about your slab with no radiant heat and ungrouted control joints. Planning to do a very similar floor soon. Are you still happy with all your decisions? Any lessons learned? thx, Ann
Mike,
Fill that can not be compacted and still be consolidated. An example of this is when you buy something like dried peas and pour a few too many into a jar to store. If you tap the jar on the counter, the peas consolidate and move downward. Run a compactor over the fill. There is certainly no harm.
Along the same lines, I've also heard the argument that consolidating the top means a tighter interface (less little pokey-upies) and less concrete creeps into the stone layer. The interface becomes, on average, more even and may help with the points Jon brings up.
Not sure if this is more theoretical though since any scuffing of the layer post-compaction with boots easily disturbs this consolidation. I assume poly helps with this issue.
Mike,
As have alluded, one of the reasons concrete cracks is that it is restrained as it cures, causing internal stresses that are relieved by cracking. Often the culprit is improper curing, where the crew finishes, and leaves the concrete to cure in open atmosphere. Another common culprit is a substrate or form that is a high friction surface that doesn't allow the concrete to move as it cures.
A single layer of 10 mil polyethylene over a flattened provides a smooth surface for the concrete to move over. Better yet is two layers, as the two layers of plastic can glide over each other quite easily, and can be done with 6 mil plastic if you're cautious about walking on it, while minimizing the costs. Check your building codes, some municipalities require a 15 mil vapor barrier if it matters.
A plate compactor costs $100 a day, its not worth the savings to skip this step compared to the cost of the project.