Exterior foundation foam

Hi All,
My original crawl space insulation plan called me for me insulating the interior of the foundation. Well it turns out after reroutingng the downspouts and correcting grade issues I still had water problems. So I dug an exploratory hole and discovered the foundation has no water proofing on it. So since I have to dig the entire foundation out any way to water proof it I might as well install the insulation on the exterior.
I want to put 2-4″ of foam on the exterior foundation but this insulation will then be sticking out from the siding by 3″ at max. Is it ok to leave the insulation with a hump from regular wood wall to foundation wall until I have the ability to add foam to the regular exterior walls? For protection I do have 36″ overhangs.
If I can safely do the above bump out I will have protected block but outside air will still be able to penetrate into the crawl from the sill plate is that allowable until the rest of the wall is sealed up?
I am in Ocean County NJ, Zone 4A
Thanks,
Chris
GBA Detail Library
A collection of one thousand construction details organized by climate and house part
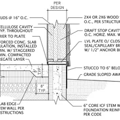
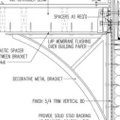
Replies
Chris,
Q。“我想把2 - 4”的泡沫表面傻人ndation but this insulation will then be sticking out from the siding by 3" at max. Is it ok to leave the insulation with a hump from regular wood wall to foundation wall until I have the ability to add foam to the regular exterior walls?"
A. At a minimum, you need to (a) install Z-flashing at the transition between the bottom course of siding and the top of the rigid foam, and (b) install some type of material to protect the exterior of the above-grade portion of the rigid foam. For more information on all of the options for protecting the foam, seeHow to Insulate a Basement Wall.
Q。"Outside air will still be able to penetrate into the crawl from the sill plate. Is that allowable until the rest of the wall is sealed up?"
A. If you know that there is a crack that is leaking air, you need to seal the crack with caulk or canned spray foam.
To hit code min for new construction you would only need R10 if insulation primarily on the exterior, which is 2.5" of EPS. If you wanted to drop back to 1.5" for aesthetic reasons you can still get there by adding another inch or more on the interior side. On the interior side, using 3/4" or more of fire rated polyiso (Dow Thermax) would likely avoid the expense of a thermal barrier against fire that might otherwise be required for interior side foam.
Make sure the top of the Z flashing is tilted to drain away from the siding, with enough pitch to be sure it will continue to drain in that direction even if there is some movement. We had a problem with that after frost heaving in wet clay backfill against the foam slid the foam up. The real solution to that is not to backfill with wet clay (we did get our backfill replaced), but it did make me think about the benefits of having a little room for error on the pitch of that Z flashing.
The Z flashing is good to keep there even after you (eventually, perhaps) put foam over the siding, to keep carpenter ants and termites from having an easy, hidden path to get from the lower foam to the rest of the house.
Thanks Martin, Dana and Charlie.
That is good advice to tilt the flashing slightly and leave it there for good to help prevent migration of termites and ants. In regards to the foam I plan on using the following item from my local Home Depot as it's the only peel and stick membrane I can find. Do you think foam compatible adhesive will stick to the outside of the product to hold the foam against the plastic? So from outside in: Foam, Plastic membranes, block foundation.
Bituthene System 4000 200 sq. ft. Waterproof Membrane and Conditioner
http://thd.co/1jGu7ab
Mr. King, I realize your dealing with an existing foundation and need to seal that surface against water but applying the foam over the Bituthene will probably mean having to anchor through it, as the film on the Bituthene will be tricky to stick to with foam compatible adhesives. This may well negate the barrier you are trying to establish. If you are sure you can establish good footing drainage and downspout controls it might not be to much of a risk to leave the foam exposed to the ground moisture, but I think others will support me in observing the risk of water building up in the foam over time if unprotectedwhich will degrade the R value. That said, a few things about my installation on a full height newly cast foundation.
As part of my overall insulation package on a new build I elected to use recycled 3" XPS (may the climate gods forgive me) on the exterior of my foundation. Initially attached the foam with powerset anchors, we then sealed the entire wall down to footer with Bituthene 4000. Application is a bit tricky even with two people, alone would be risky. Working temperature of about 60-70 is nice although direct sunlight will make it get hot fast. It becomes very gooey to almost runny the hotter it gets. We also applied the Grace bonding agent to the foam to ensure the best adhesion.
One of our details involved making two 90 degree bends cleanly for a flashing strip. Using something akin to a wallpaper tool would have been a good idea I didn't have while doing it. I did find that if you are desperate to release a misplaced or crooked piece, Naptha will help you peel it back without pulling the bituthene layer off the plastic carrier sheet. The naptha will interfere with the sticky-ness so let it evaporate for a bit before resetting the membrane. Mostly, don't peel off any more backing than you can handle and be careful to line up the drops.
My spring/summer project will to be complete the final protection of the above grade exposure, but even with nearly 12 months of exposure it appears to be fairing very well. When back filling against it I would suggest something to protect it from sharp rocks or debris poking holes through it. The native soil we had is very full of sharp rocks so I opted to place clean soil from the wash ponds at the gravel yard as a buffer from the native soil. A quicker and probably cheaper solution presented itself too late; plastic sheeting that is 35 -50 mil. It is extremely tough and resists even direct attack with a phillips screwdriver tip. It would have saved a lot of trucking and skid steer work as we could have just unrolled the plastic like a ultra duty house wrap and lived with the rocks.
A year and change after the install I remain optimistic that the foam is being safely protected by the Bituthene and providing full insulation value. The few penetrations I made, I sealed with Bituthene strips.They have not wept any water. Plus I now have the dry warm basement I have always wanted. Hope this helps you decide how to proceed.
Chris,
I don't know whether foam compatible adhesive will stick well to that membrane, but the foam will be held in place by the backfill so I wouldn't worry about it too much.