Good but realistic wall assembly for Climate Zone 6?

I’m spinning in circles on wall assembly for a small rectangular new house in Maine (climate zone 6) – Considering double-stud vs. 2×6 with exterior insulation (or ZIP R?). Have read lots of articles and looked at diagrams of “layers” for each, and can’t quite come to terms with:
— For double-stud and for 2×6 with exterior insulation — What is thesimplestapproach? In terms of the number of layers and framing/installation complexity? (see diagrams linked below)
— Assuming air sealing won’t be perfect (let’s be realistic) and it won’t have triple-pane windows (though I’ll look for higher-performance double-pane incl fixed windows) — Are double-stud walls overkill如果env的其他部分elope aren’t quite as good?
— Is 2×6 framing with ZIP R-sheathing (insulation facing interior) a reasonable alternative?
I’d love feedback! Attaching diagrams with assumptions for each — Do I even have the “layers” right for simple construction?
https://drive.google.com/file/d/1W-_M4wVkvvKJRvxKkXV_m3Jh24itTMqd/view?usp=sharing
(As I get feedback I will update “layers” in this version)
Please note – At this point I’m just trying to make the first decision of the general strategy, and don’t need to figure out the exact materials…However I’d like to avoid spray foam and XPS (at least).
(Also there is no local building energy code – choose your own adventure!)
GBA Detail Library
A collection of one thousand construction details organized by climate and house part
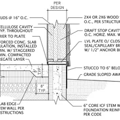
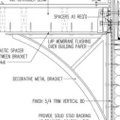
Replies
I like exterior rigid foam (using polyiso). It’s not that hard to do unless you go super thick, up over maybe 3” or so. You’d have a wall from the inside out something like drywall (use 5/8” here, much better than the usual 1/2” and very little difference in cost), studs and batts (I like mineral wool), plywood or OSB sheathing (I like plywood, either way detail it as an air barrier with a urethane sealant around the perimeter), exterior rigid foam ideally in two layers with seams staggered. I like the two layers to be different sizes. For 3” total thickness, I’d do a layer of 1/2” first and then a layer of 2-1/2” thick. The thicker foam is stiffer and helps to keep the inner foam and the overall foam layer flatter.
Install the interior drywall airtight as a belt and suspenders air barrier and also to limit moisture migration into the wall. Do all of this and you’ll have a pretty good wall assembly. There is nothing wrong with double stud walls, I just like to use exterior rigid foam, but I’ve only ever done retrofits and no new builds where double studs would have been an option. You’ll probably get some other replies with pros and cons of double stud walls too. The biggest downside with exterior rigid foam is probably the need for long screws to hit the studs through the foam layer, but that’s not really all that difficult in my experience.
Bill
Amanda
I am designing a similar home (simple rectangle but 2000sqft with bedrooms in the basement) that I will be building for myself in Wisconsin, Zone 6. I will be doing most of the work with a few specialty subs. After a lot of research on assemblies I decided to go with the double wall assembly as discussed in Dan Kolbert's recent FHB article on double walls. I too will be going with standard double pane windows (window to wall ratio of about 18%) and shooting for 1ACH @ 50 pa for air sealing.
I ran the energy modeling for my home with R45 walls and the above specs and my heating load comes in at 25000 BTU/hr. Running the model with triple pane windows brings the heat load down to 20000 BTU/hr. Running it again with Euro Passive House windows brings it down further to 18000 BTU/hr. Using my local energy rates the better windows translate to a savings of $500/year but the windows had a premium of $25k over the double panes. too long of a payback for me to justify.
Regarding the wall assembly R value, based on my modeling if I was to do the prescriptive code method of R13 wall cavity and R10 exterior insulation in lieu of the double wall my heat load jumps to 30000 BTU/hr and increases my heating cost by $300/ year. The code wall assembly is about $5/sqft material wise cheaper than the double wall which would be a 37 year payback for my house - BUT - by going with the double wall I will be able to heat my house with two mini split units saving me the cost of a full heating system which drops the payback to only a few years.
Andy Engel wrote an article on GBA a couple weeks ago discussing in detail the methodology and spreadsheets that I used to decide on the assemble.
Ian
Did you go with dense pack cellulose in your double stud wall or some kind of batt fill? I’ve heard dense pack cellulose can make for very economical double stud walls but I’ve never tried it myself.
Bill
Bill
I am going with dense pack cellulose. My walls will be 12" and I have received pricing from qualified installers in the $4-$4.50 per sqft range.
As you said in your comment the biggest downside to exterior foam is the long screws, which I agree with completely. Another downside for my mostly solo DIY build is having to install the exterior insulation after standing up the walls. With the 2x6 exterior wall I can tape sheathing seams and install the rain screen battens before standing up the walls.
Ian
Ian, this is often a question I have when seeing double walls discussed so frequently. Aside from the issues related to your DIY assembly you noted, for general cases wouldn't upgrading to 3" of exterior polyiso, or using 2x6's for the framing, have gotten you much closer to R45 a lot cheaper? I question if paying contractors to dense pack walls and build the framing twice is cheaper than paying framers to install exterior foam, though I guess it depends on your builder and insulation contractor.
Carson
I agree that the choice between assemblies is generally a case by case basis. For my build I considered the additional window flashing work, the install of 3-4” of EPS (I was planning to use EPS bc it doesn’t lose performance at low temps) and the added work to install the rain screen battens without compressing the EPS and making the siding wavy. All of these scopes would fall to me, by using the double wall I am shifting the labor burden of insulating to a sub and simplifying my window and siding installs. If I put little to no value on my own time involved in the build then yes a 2x6 wall plus EPS is cheaper but my approach in documenting the project is to consider myself as both the client and GC. I hope to use this experience to help me become a better lead carpenter, project manager and estimator.
Ian
thanks for the input Ian,
As an owner/client, I understand that every situation can be a bit different, but I find the wild and wide variance in contractor pricing really frustrating and even on a site like GBA it's not clear at all what the most economical option "typically" is. I guess coming from a world where most purchases are globalized and prices can often be tracked and easily compared, construction is a whole other universe. Still, I find it hard to believe that a general rule for what something "should" cost can't be made based on measured amounts of labor and materials. Let's say 2x6 mineral wool batts + 3" of polyiso = 23+20 = R43. Based on prices from home depot for the mineral wool and insulation4us for the foam, that's about $1.30 sqft for the mineral wool and $1.60 for the rigid foam. In total that's $2.90 sqft. For cellulose, the material cost can be estimated from home depot pricing and using the coverage chart from FHB (https://www.finehomebuilding.com/membership/pdf/188241/Expanded_Bag_Coverage_Chart.pdf), which is a per bag coverage of 6.2 sqft for R43. Comes out to about $2.30 per sqft for materials. I suspect the lumber and labor cost for people to build out a second framed wall for the double walls would be well over that $0.60 difference, and to add to that I would think the labor cost to install dense pack 12" of cellulose would be greater than installing the exterior foam sheets and bucking windows.
All of those walls work and can be built for a reasonable cost. The important part is choosing an assembly your builder is comfortable with. There is no point in picking your magical assembly if nobody will build it for a reasonable price.
我建议看一面墙是2×824OC with R30 mineral wool batts. This is all standard construction so it can be built without any special knowledge.
Akos,
We finished structural design now I'm playing with cost effective walls and I agree. I'm in climate zone 6 as well. One thing I noticed is it's about $0.70 sq/ft cheaper to purchase two R15 rockwool batts instead of one R30 rockwool batt. Is the 1/4" gap okay since the batts equal 7" and the stud cavity is 7.25"? My plan was to cut the batts in half so they are 23.5" and stuff into my stud cavity which is 24" o.c.
Also as I search to prepare for my project I come across a lot of your posts. Are you open to consultation? If so I'll find a way to leave contact info
There is nothing wrong with using two layers of batts. A small gap on the interior side doesn't matter. You don't want a gap on the sheathing side as you can create convective loops and reduce the effective R value of the wall.
You can sometimes fluff the batts a bit to take up the space as well.
2x4 batts for 24" OC wood walls are stock item at my local box stores. Even if you have to order it, it is worth, way less work.
The forum is a good place if you have further questions, post them here.
Amanda,
You have got some excellent advice already. I'll just make some specific comments on the options you have shown.
- The rain-screen on all your options shows vertical furring, but if you are planning on vertical siding you need to either use a second layer of horizontal furring, or a proprietary rain-screen mesh.
- The area between the double walls is typically used as an insulated space, that can vary in thickness to achieve whatever R-value you want. if you would like a dedicated service space, the best place for it is the inner stud wall.
- The vapour retarder is best placed where you show it in the inner third of the double wall, but not on the very inside where it is susceptible to damage.
You can do vertical panels with vertical furring (it's preferable, actually). However, the furring needs to be on the studs, not in between studs as shown in the drawing (regardless of what kind of siding you put on.)
Our house in Maine has double stud walls, triple pane windows and is at Passive House level of air tightness. Our builder had never done double stud walls. He found it easy. He'd never really tried to do a very tight house, either. That was simple also.
Don't assume you can't get a very tight house. Nothing about air tightness is difficult. It just requires attention to detail. And lots of tape.
As for windows, shop around and don't rush into getting one of the nationally recognized brands until you look into other options. I'd check out Performance Building Supply in Portland. A small house doesn't need a lot of windows. Great windows provide a real comfort factor that may not translate to much financial savings.
Don't forget to use reclaimed foam under your slab.
Your biggest challenge is going to be finding a builder that has experience with energy efficient construction techniques...or finding one that is truly open to and committed to following through on new techniques. It's good to research/understand different wall assemblies, but as Akos mentioned above, I would make a final decision based on what the builder is most comfortable with.
As complete novices, we acted as GCs for our house build in New Hampshire (zone 6), it's about the same size as your plan. The company we hired to complete the foundation through shell used a 12" double stud wall and it seems to be a more straightforward approach vs exterior insulation.
I don't think shooting for a R40 wall is overkill, even if your windows are "standard" grade. Regarding windows, you don't have to get expensive imported models for good performance, take a look at Alpen and Logic from Pinnacle Window Solutions (Hallowell, ME):
https://pinnaclewindowsolutions.net
I'd also focus on the house as a whole vs fixating on the R value of your wall. You're better off with a well built house with R30 walls, good air sealing, proper HVAC, good windows, etc...than a house with R40 walls, cheap windows, and improper HVAC equipment.
Looking over your document, a few other recommendations:
-Plan for solar from the start. Make sure your roof setup is ideal for it. Make sure you have mechanical space for the inverter and conduit.
-Consider dropping the wood stove, you don't need two heating systems. The stove will take up a lot of space in a small house. This is a guess, but you'll probably be spending at least $5k+ on a nice stove, chimney material, wood sheds, and accessories. Put that money towards the shell/windows or solar.
-Strive for perfect air sealing, you don't want random air leakage. You're going to need consistent or almost constant ventilation in Maine in the winter. Open your windows spring through fall when you can, and shut off the HRV if you want.
Also, consider contacting and working with some of the Maine and New Hampshire based companies that offer fully built efficient homes or just plans:
https://thegohome.us
https://www.brightbuilthome.com
https://unityhomes.com