Heat loss through crawl space

I’m considering buying an older, brick exterior, home (about 20 years old) that currently has a vented crawl space. The location is Georgetown Ky. I like the layout and the location but it sure needs some “energy conservation” upgrades. Tentatively the first upgrade will be “sealing” the crawl space, with mult-ilayer reinforced poly, after adding r10 foam on the inside of the crawl space’s exterior walls. My initial question is; should I cover the dirt floor with insulation (I’m thinking of r10 mineral wool bats). The HVAC system is two heat pumps with air handlers in the crawl space so occasional access is needed for filter changes etc. There is no insulation in the floor above the crawl space. Is there any way of estimating the heat loss through a “conditioned” crawl space? How effective is insulation in reducing the heat loss?
Thanks
Jerry
GBA Detail Library
A collection of one thousand construction details organized by climate and house part
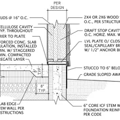
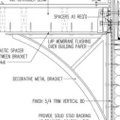
Replies
Well I did some more browsing of the internet and found NO advocates for insulating the dirt floor. But i did find many who said more "r: on the perimeter walls is better. All suggested EPS foam for the walls. Is there any reason mineral wool would not be suitable?
Thanks Jerry
Jerry,
Q. "Should I insulate the crawl space floor?"
A. In your climate zone, insulating the crawl space floor wouldn't be cost-effective. (In other words, the expected energy savings would be too low to justify the cost of the insulation.)
Q. "All internet articles suggested EPS foam for the walls. Is there any reason mineral wool would not be suitable?"
A. Mineral wool is a bad idea because mineral wool is air-permeable. Mineral wool insulation would allow moist interior air to contact the cold concrete walls, resulting in condensation.
For lots of information on the work that you are contemplating, read this article:Building an Unvented Crawl Space.
Martin,
Since the insulation is outside the multi-layer reinforced vapor barrier, yet inside the masonry walls, it should only see outside air dew point, doesn't this allow mineral wool?
Jerry,
At this point, I'm not sure whether you are thinking of using the mineral wool insulation on the crawl space floor or on the crawl space walls. But putting mineral wool in either location would be a mistake.
The dew point is a temperature, not a location. I'm not sure what you mean by "outside air dew point." What we are worried about is the concrete walls of your crawl space getting cold enough that the walls are below the dew point of the interior air.
Perhaps you are imagining that you can install an airtight air barrier (perhaps polyethylene) on the interior side of the mineral wool. People have tried that approach; it doesn't work. You can create a "good enough" air barrier with rigid foam (as long as the seams are taped), but you can't create a "good enough" air barrier with polyethylene.
First of all, the air between the fibers of the mineral wool are interior air -- humid air.
Second, the air between the fibers of the mineral wool get exchanged with the air in the crawl space on a regular basis, through a "pumping action" created by diurnal temperature cycles. When the temperature drops, the air contracts, and more crawl space air is pulled into the insulation interstices. When the temperature increases, the air expands, pushed some of the air between the insulation fibers into the crawl space. You can't install polyethylene in a tight enough manner to avoid this pumping action.
Jerry,
Isn't this an almost identical discussion to the one you had with Martin several years ago about using batts in a basement wall?
//m.etiketa4.com/community/forum/passivhaus/24201/air-sealing-and-insulating-poured-concrete-basement
Malcolm,
是的,从2012年我问答线程的讨论s similar to this discussion.
If I were organized, I would come up with a list of 40 answers to questions, and I would automate my responses -- so that I could punch *38 or *22 into my computer, and four paragraphs would appear. It would save a lot of typing.
Using 2" of fire-rated foil faced polyiso (Dow Thermax) would meet code min for R-value, and in most places it would not need an interior side thermal barrier against fire in this application. If the crawlspace were ever hot enough to light-off the foam the house is already a total write-off, but with polyiso it would char in place rather than melt into flaming puddles.
The uncovered polyethylene vapor barrier on the floor would be a bigger fire hazard than foil faced polyiso- use EPDM instead.
The summertime outdoor air's dew point is above the temperature of the foundation near the floor. Even with a perfect interior-side vapor barrier, putting the air & vapor permeable insulation against the foundation wall risks keeping the insulation fairly wet. It's even worse if you're actively air conditioning, which will bring the crawlspace temperature below the summertime outdoor air's dew point, and copious amounts of moisture will collect on the vapor barrier. The insulation is blocked from drying toward the interior by the vapor barrier, and it can't dry into soil, and will only slowly dry toward the exterior via the above-grade exposure as conditions allow, which isn't a large fraction of the year. The insulation will stay damp year round- count on it. While foundation can still perform it's function at any level of moisture content, the insulation not so much.
This is not a theoretical problem- it happens in the real world, with real consequences.
If you want to minimize the amount of plastic insulation, trapping an inch of vinyl or foil faced EPS (or 3/4" foil faced polyiso) against the foundation, with a non-structural studwall insulated with rock wool, (or 2" of continuous rigid rock wool) will have sufficient wintertime moisture dew point control at the foam/fiber boundary even without an interior side air barrer. (The rock wool also behaves as an ignition barrier for the foam, though it may or may not be tested and certified as such.) The facers on the foam have sufficiently low vapor retardency to limit ground water or exterior air moisture diffusion toward the interior, and the fiber stays dry. In colder climates than yours (Zone 4A) the foam-R may have to be increased to avoid wintertime moisture issues unless there is an interior side air barrier to the fiber insulation.