HELP – Lost thermal break at the slab meeting code

We are building a house in upstate NY on a floating insulated slab using ICF’s on top of footers. We presented the attached original plan to the town and the building inspector came back with a requirement that we put 12 inches of concrete under our double wall with no part of the wall bearing on foam (see revised wall section). He was able to cite a section of the code that says a foundation wall must have a minimum width equal to the wall size (with two exceptions that don’t apply to us). This is one argument that we will not win.
Given that the forms are ready to pour, should I be concerned about the lack of a thermal break at the foundation. My builder has said he can put in a 1/2 of polyiso. Will that be sufficient? If not, does anyone have a quick fix to address this issue. We are already behind schedule.
Thank you
GBA Detail Library
A collection of one thousand construction details organized by climate and house part
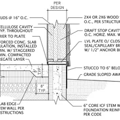
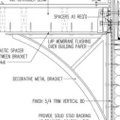
Replies
You have this set up with the interior wall as the load bearing wall. You will need to get a locally licensed engineer to sign off on the drawings that the exterior wall is not carrying any building loads from the floor or roof above. This will relieve the inspector from liability related to settling of the structure.
However you will need to satisfy the engineer that the building will carry the load and as drawn your original design interior load bearing wall is resting almost entirely on the edges of your slab insulation. If you are hoping to avoid having foam open to the room on the interior you will probably still need to either move the load bearing wall to the exterior wall and have the interior wall non-load bearing or chamfer the foam where it is exposed to the interior and have something of a cold edge there and put insulation on the exterior of the stem wall and deal with the hassle of protecting it out there.
I've attached a couple of drawings to illustrate better what I am recommending. Hope this helps.
Hi Michael,
A local engineer did sign the original plans but the building inspector cited the code language and would not approve the plans without the change to wider footings (we lost almost 3 weeks trying to convince the inspector).
Do you think adding a band of 1/2" foam on the inside (instead of sheetrock) behind the baseboard will help? My builder thinks the energy penalty will not be significant with the revised design.
Quick fix
当你说我assumi表单已经起来ng you mean your forms for your 8x16 footings, not your ICF's your original plan was to use 8" core ICFs for your forms with the inner and outer walls both partially bearing on concrete and mostly on foam.
If you cut the interior of the ICF down about two inches and form it back up by screwing 1x6's to the interior face of the ICFs extending up to the original level you can pour them with an 8" core so that the interior wall is bearing on a 2" cast concrete ledger aligned with the top of the foam and cast integral with the ICF core. You still need an engineers stamp but the way it is drawn you have pretty good bearing on the exterior wall and this would give you one and a half inches of bearing on the interior wall directly over the ICF core and 2" bearing on the 2" x 2" concrete ledger for 3 1/2" total bearing on the load bearing wall and the exterior wall is just a frame to hold the windows and siding out beyond the bearing wall and seems to have 2 1/2" of bearing on the core due to your water table detail as well as plywood gussets. I think your engineer would be very comfortable signing off on that and you still have the full 2" of foam on the exterior of the ICF plus you can add 1" more foam under your drywall and baseboard when you pour your interior slab so you come out pretty whole.
Quick fix that. What you wanted I hope.
Thanks Michael,
I will pass it by my builder. The building inspector may not sign off if any part of the wall bears on foam. He says he is responsible even if an engineer stamps the drawings. This is New York, the land of regulations and lawyers.
Michael-
Thanks for your advice. I am the builder involved in this project. Your suggestion is really good, but I think the concern Liz has is the cold edge you mention in your first post- specifically the thermal bridge from under/inside the poured footing, through the ICF core, and then through the inner wall's bottom plate (in the second design she posted).
Before going to the second design, I proposed using taper top ICF forms for the inner side (similar to your suggestion) but the building inspector wants the full thickness of concrete the whole height (ie no cantilever). It took those 3 weeks to get him to ok the shallow frost protected foundation design even though it is in the NY code even with the engineer's stamp so we really need a solution that is not structural in any way (or looks conventional).
In terms of fixing it, the two things I have been able to come up with is 1) a 3" rip of foam over the bottom plates that would be in-plane with the drywall (and under the baseboard) or 2) set the wall down into the ICF by 3" (probably to by cutting down one of both sides, pouring the ICF, building the wall, then scabbing foam back on and pouring the slab).
It is my feeling that this thermal bridge, while unfortunate, is not a show stopper under the circumstances (ie not a passive house). I guess I would appreciate any thoughts on my proposed fixes, other ideas, and thoughts on the significance of the problem.
What I noticed in your first wall design is that the exterior wall is bearing to the roof trusses and the interior wall is bearing the floor trusses; therefore the whole double wall must be bearing on concrete, not on any insulation. One fix could be to make the roof and wall trusses bearing at the interior wall only, thus allowing the exterior wall to “float” on the exterior foam of the ICF. I used this approach a while back with flat roof trusses.
Elizabeth, I'm not surprised that the building inspector is now reticent to accept your engineer's stamp over his interpretation of the code requirements. Your original section had all the second floor loads bearing on a wall that sat on foam. How was this ever going to work?