Insulating and Fireblocking in Basement

我装修地下室在芝加哥地区I thought I had it all sorted out. I was planning to put 2″ XPS and then a 2×4 stud wall with mineral wool, fill the rim joists with mineral wool (and maybe XPS) but leave them accessible for future needs, and leave the joists exposed but painted black. Then I started reading about fire blocking and condensation and after doing weeks of research I’m incredibly confused and no longer have any idea what to do. I’ve included pictures so you can see what I was planning to do and what I’m stuck dealing with.
Problem 1:Some areas of the basement have electrical conduit running along the sill plate which prevents me from insulating or fireblocking. Technically I can move these but it will require running new conduit and re-wiring most of the 1st floor of my house.
Problem 2:Some areas have plumbing, electrical conduit, or other pipes running along the bottom of the joists in close proximity to the foundation which prevents me from attaching the top plate to the joists like you’d normally do. I can’t move these myself so $$$.
Problem 3:On one wall I have the main waste lines running directly adjacent to the foundation before leaving the house. There is no way to put insulation between this and the wall. Again, moving these would be $$$.
So building and insulating walls the normal easy way won’t work. Moving all the utilities will probably be too expensive. I could leave everything uninsulated and run the furnace a little more like they did with the previous basement for 45 year but that also feels wrong so perhaps there is a middle ground?
Solution(?):Maybe I could simply build the walls shorter? Instead of going all the way up to the joists I can stop 3-4″ below that to clear the obstructions. I’m leaving the joists exposed and would like at least some access to the rim joists anyways. If it looks bad I could hide it with some crown molding or something. I’d still need to secure and fireblock the top of the wall though. Not load bearing of course, just needs to prevent the wall from tilting in or out. But how?
– 1×3 or 2×4 PT ledger against the foundation wall, run the XPS up to the bottom of it, then use braces or plywood to secure the wall to the ledger.
– Ledger (regular or PT?) against the XPS, sandwiching the XPS between the ledger and the foundation, and use some sort of braces or plywood to secure the wall to the ledger.
– Same as above but put the “ledger” on the back of the 2×4 wall, eliminating the need for bracing but needing longer bolts.
——胶合板条上的墙,spanning the distance to the foundation, and attached to the foundation with angle brackets.
In any case I could cap the top of my slightly-short wall and the gap behind it where the XPS is with some combination of plywood, drywall, and maybe even more XPS to provide fireblocking and thermal breaks. I’m really not sure on the details though. I’m afraid that I’ll do something in a way that causes condensation and mold or breaks the thermal barrier in a way that negates the point of the insulation to begin with. I also need to deal with the plumbing against the wall. Perhaps I only insulate below the waste pipes but not above them? It wouldn’t be as efficient of course but that would still be better than no insulation anywhere. Or would it?
GBA Detail Library
A collection of one thousand construction details organized by climate and house part
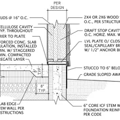
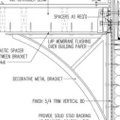
Replies
Hi no expert here but if you use furring strips then you don't need a top plate. These walls are not structural so if you really want a top plate you can start it underneath a box in for your sewage pipe. Also waste lines could probably be fine without insulation behind them if you can't get to it. They aren't constantly running water like water lines so I would think difficult for it to freeze immediately when draining water or sewage would be close to impossible. Maybe I'm wrong on that one. Can mineral wool be left exposed in rim joist?
Thanks for the reply!
Could you explain how you'd do the furring strips a little more? The foundation wall is a little wavy and out of square so in order to make straight and square walls I'll need to space them 0-2" away from the foundation. How would you manage that variable gap? 2-3 rows of horizontal furring strips then build a straight 2x4 stud wall in front and use some sort of blocking between the wall and the furring strips to manage the gap? I'm attaching a picture of how I was thinking to use a single furring strip/ledger at the top of the XPS to brace it and support the fireblocking at the top but I think you're suggesting an easier and simpler way that I'm not quite understanding.
For the pipes... I'm not worried about them freezing but rather condensation on the front of them. The 2" XPS should prevent warm humid air from condensing against the concrete but the pipe would be a big metal thermal bridge exposing a cold surface on the inside of the stud wall, bypassing the vapor barrier properties of the XPS. I figure I either need to do some sort of insulation and vapor barrier around the pipe to prevent this or I shouldn't insulate that area at all so that the warm room air keeps the pipe warm enough to prevent condensation or at least allows it to evaporate by being exposed.
The experts could help you better here but if you need to build a 2x4 wall and you are worried about straightness take a 2x4 and attach it to the joists past the sewage pipe. Then box in your sewage pipe like an L ending under the pipe and in front of your insulation. Then you can build a wall and attach your top plate to the box out. Just don't use long nails and nail right into your sewage pipe. Just find where the wall sticks out the most and line up your 2x4 wall to that. Leave the gap, you already have your continuous insulation and wall will be straight.
For me I wouldn't care too much about waviness of wall because it is a basement but then again in my century old home a lot is already out of square so for me it isn't necessarily an eye sore.
I also think you should just insulate as much as you can behind your pipe. Putting insulation in front will just make the pipe colder than rest of wall and create a bigger problem
I was thinking about a soffit but it would be at about shoulder height so not super safe. I think what I will do is position this entire wall an extra 2" from the foundation and use some spray foam around the pipe to prevent condensation. It will be 8" of wall instead of 6" but the pipe would be entirely enclosed (except cleanouts etc of course, small closet for that) and insulated enough to hopefully prevent condensation.
I'm planning to put up the foam first and then I can use a laser to find and mark the tightest straight line for the stud wall. At the same time I can use the same laser line to mark the piece of plywood I would use to brace the top of the wall and ensure everything is plumb.
Only thing I'm not sure of anymore is the mineral wool in the stud wall itself. The basement really isn't cold so 90% coverage of R-10 XPS might be enough for our needs.
我将使用polyiso,不是XPS在这里。你可以把它around the waste lines, waste lines aren't usually freeze risks the way supply lines are -- the "waste" makes it's own heat. A small two part spray foam kit is probably your best option to tie in the oddball rim joist areas where you have no other way to get a good seal around all the obstructions. It's OK for the conduit to be in the spray foam. I'd tidy up that windy BX cable run a bit though, but that's just me :-)
You can leave mineral wool exposed in a rim joist area, but you need rigid foam behind it (against the rim joist) to avoid moisture issues since mineral wool isn't an air barrier, and is completely vapor open. The mineral wool can act as your fire protection for the rigid foam too if needed.
Bill
I previously ruled out polyiso due to the loss of R value at lower temperatures, that it's 50-100% more expensive than XPS, and the fact that I can get the more environmentally friendly XPS here. I'm not opposed to reconsidering though if there is enough justification.
As mentioned to Hammer I'm not worried about freezing but creating a thermal bridge that causes condensation in the well. You are right though, these pipes are going to be warmer than the surroundings so maybe it's ok? I looked into the two part foam kits. I could do that. Is there a big difference between those and something like Touch n Foam MaxFill in a can? I could put an inch of either foam on the pipe and that would probably be good enough. Or not?
I should be able to put XPS in the rim joists yes. The scraps from cutting the 4x8 wall sheets short are very conveniently rim joist height and with a length to go around the entire perimeter. I was worried about moisture here, but I just ordered a moisture meter so I can check the areas before doing anything and also pull out a panel every few months for the next year or two in order to make sure I'm not causing any moisture problems on accident.
The polyiso R loss in low temperatures is overrated, it's not really a big problem. Even derated, polyiso is still about R5 per inch -- the same as the initial rated R value for XPS. On the interior of a basement wall though, you're not going to ever see the really cold temperatures where the reduced R value is an issue though, so this is a good place to use polyiso. Polyiso lets you get more R per inch, so you can keep your wall more compact.
Unless you have access to XPS that is using more benign blown agents than the common stuff out there, polyiso is actually more environmentally friendly than XPS.
Two part spray foam is NOT the same as one part "canned foam". There are different products. The two part spray foam kits are usually a sort of DIY version of the closed cell spray foam that a contractor would normally install. The kits are very expensive for the amount of spray foam you get, but for small jobs they can be worth it since they can still be cheaper than having a contractor come out for a very small project. You could try encapsulating the pipes with spray foam. I'd not fill the entire cavity though, I'd just put a condensation control layer on the pipes. The reason is that with the pipes fully encased in spray foam, any future maintenance will be a nightmare -- you'd have to chip the pipes out before you could do anything.
Check what is on the other side of your rim joist prior to insulating. If the other side is something vapor open, XPS would be fine on the interior. If the exterior side is covered by something that is a vapor barrier (in my home, I have exterior foil-faced polyiso), then using EPS on the interior of the rim joist will provide some drying ability and is a little safer than something more vapor closed like XPS.
Bill