Keeping exisiting fiberglass insulation?

We are renovating an 1880 farmhouse in zone 5, the living room walls have newer sheetrock and fiberglass insulation in them, while the upstairs walls have lathe and plaster and old cellulose. We are currently gutting the upstairs walls and will be having close sell spray foam installed, but we are torn as to whether or not to gut the downstairs walls. wondering if the demo and cost is for the sake of the increased insulation is worth it?
Any thoughts would be much appreciated.
Thanks,
Dave
GBA Detail Library
A collection of one thousand construction details organized by climate and house part
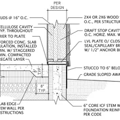
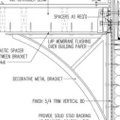
Replies
>"'We are currently gutting the upstairs walls and will be having close sell spray foam installed..."
You may want to do the math and reconsider:
https://www.finehomebuilding.com/2017/07/10/closed-cell-foam-studs-waste
>"...but we are torn as to whether or not to gut the downstairs walls. wondering if the demo and cost is for the sake of the increased insulation is worth it? "
The above analysis may answer the question. Bear in mind that closed cell foam is one of the least-green insulation products in common use, even when blown with comparatively benign HFO1234ze rather than the industry standard HFC245fa (now banned for this application under the Kigali Amendment to the Montreal protocol due to it's extremely high global warming potential.) An inch of closed cell foam uses as much polymer as 4" of half pound open cell foam providing only a paltry performance boost to a studwall assembly. But even open cell foam has a bigger environmental footprint than fiberglass or rockwool, and cellulose would have a negative carbon footprint.
If it's currently insulated with low density blown fiberglass it may be worth dense-packing what's there for increased air retardency, but it's not going to be worth gutting the walls for re-insulating unless it includes deeper cavity depth and a thermal break over the framing, such as Bonfiglioli strips, or simpler-thinner foam-only and long-nailing/screwing the gypsum board through the edge foam. Even 3/4" of foil faced polyiso over the framing edges cuts the framing losses of full-dimension 2x4s by half or more, and 1" would leave a 5" cavity depth suitable for compressing R21 fiberglass or R23 rock wool, either of which would still deliver ~R20 or better @ 5.0".
https://www.finehomebuilding.com/membership/pdf/9750/021250059.pdf
喷雾泡沫是浪费在这样的墙。和缺点ider that I’m one of the bigger spray foam proponents on this site telling you that. The thermal bridging of the studs pretty effectively kills the overall wall performance with spray foam, so you end up with the spray foam costing a lot more but adding very little performance compared to cheaper types of insulation.
Dana gave lots of other options above. I’d probably use mineral wool myself since I like working with that material. Whatever you choose, you’re likely to save money over spray foam. That extra savings can be put towards insulation in other areas, or other efficiency improvements elsewhere.
I would consider opening up the other walls. In older houses, there are often pretty big comfort and efficiency improvements to be had by air sealing things. I think you’re likely to find the air sealing to be of even more benefit than the extra insulation. If this was my house, I’d open all the walls, do a thorough job of air sealing everything, and then put in mineral wool batts. And I’d probably also install a smart vapor retarder on the inside.
If you do the air sealing work — and you really should — with a job this big you’ll find the “great stuff pro” gun and cans to be more cost effective and also MUCH easier to use than the regular cans with the straws. You’ll also want some urethane caulk too for the little spots that the expanding foam doesn’t get into well.
Bill