什么样的节能s can I expect with 2″ of rigid foam?

I live in Zone 4A, the house was constructed in 1968. 2×4 walls with unbacked yellow fiberglass. Interior has paneling over drywall (it was built that way). Exterior is 3/4″ plywood with a foil backed paper and polystyrene filled aluminum siding.
I’m having the siding removed and replaced with 2″ of foamular and Certainteed vinyl siding. Can I expect anything dramatic in terms of energy savings?
I’ve already had 12″ of cellulose blown into the attic space over the 4″ of fiberglass, had the basement block walls and rim joist filled with CFI corefoam, and had all the windows replaced with low-e double paned argon glass.
Thanks for any comments or suggestions.
GBA Detail Library
A collection of one thousand construction details organized by climate and house part
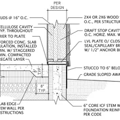
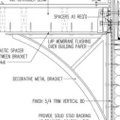
Replies
Pete,
There is no way we can answer your question without more information. If you want to know an answer based on calculations, you will have to hire an energy consultant to run an energy modeling program, or run the calculation yourself.
We don't know the type of heating system you use, whether you have a cooling system, or what your fuel costs are. We don't know the size and configuration of your house. We don't know anything about your windows. We don't know if your house is leaky or tight.
We also don't know your definition of the word "dramatic." But I'll hazard a wild guess: most Americans would probably say that your anticipated savings, while measurable, will not be dramatic.
But -- it depends.
Jin,
The house is 30'x40' with approx 980 sqft of exterior wall area, and the studs are 16" O.C. 47567
ok try and look into it when i have some free time tonight .. meanwhile if you could find your heating degree days and cooling, would speed up things nicely :)
Pete : what we can do ( i luv to do it! so i'll try it out ) is to measure your maximum potential energy savings on the heat loss of the walls themselves ..
this will not give you a usable result directly, but it is fun to know that it is the maximum potential savings , and sometimes it is low enough to dether from doing it ( but i doubt it will be here )
because you will never have higher savings than the potential heat loss difference on/or a resonnable ROI .
can you give us the total wall area and the approximate spacing of the 2X4 ??
will also need your city or your HDD / CDD
"" edited to try and fix my very deficient english somewhat ""
With the foam-loaded aluminum siding and R11 batts in the 2x4 framing the U-factor of the walls was about U0.75 to U-.80. Replacing that siding with 2" of XPS and vinyl siding cuts that to something around U0.40-0.50, depending on framing fraction, and how well the original fiberglass was installed, and how it has held up over time.
If it's not too late, it's far greener to use 1.5-2" of polyiso (eg Thermax) rather than XPS (Foamular), since the blowing agents used for Foamular have more than 100x the lifecycle greenhouse gas potential of those used for XPS. Most of the blowing agent escapes from XPS in the first ~50 years, reducing it's R-value to about R4.5/inch, and at full-depletion it runs R4.2/inch. Polyiso loses most of it's blowing agent in the first few months (mind you that's still a far lower global warming hit than from XPS over the same few months) and it's fully depleted R value is pretty close to it's labeled R-value. It's also much better stuff to have in the event of a fire, since it's kindling temp is higher than polystyrene, and it doesn't melt, dripping streams of flaming polymer, but chars-in-place. It'll sustain flame once you get it roaring, but a fire on the second floor won't drip burning goo down the side of the house (the vinyl siding may be performing that function. :-) )
At 1.5" standard grands of foil-faced polyiso has about the same R-value as 2" XPS, and in 50 years will have a higher R value than 2" of XPS. With the inherent air space behind the vinyl siding the exterior foil facer adds another ~R1-R2 of effective average performance too, from the radiant barrier effects.
当你有外墙值得开采的一个nd blowing cellulose from the outside, compressing the batts, which will fill in most of the gaps (it might not completely fill around batts improperly installed around wiring & plumbing), and will reduce the air leakage into the wall cavities dramatically, even if it's not dense-packed. (Dense-packing may be difficult or impossible with the batts still in place, but that's OK.) Retrofitting blown fiberglass instead of cellulose would be beneficial too, but unless you can dense-pack the fiberglass it won't be as air-retardent as cellulose.
Bottom line, with these upgrades you will have cut the heat losses/gains from walls by about half, a bit more than half if you retrofit the cavity insulation at the same time and go with 2" of polyiso instead of XPS. You've already cut the window, foundation and attic losses by more than half, but it's probably cost effective to go a bit more on the foundation, if there's room to put an inch or two of EPS or iso on the walls. In many or most homes at your current wall & window U-factors wall losses are about 1/4 to 1/3 the total heat load, so it should cut the heating bills by more than 10% but probably not more than 20%, unless those walls are also leaking copious amounts of air. The effect on cooling bills is impossible to even take a WAG at, since cooling loads are driven more by window and attic solar gains, with peak cooling loads often driven by west-facing windows.
Sifu Dana : i thought you are supposed to let your apprentice work it out so he can learn a bit!!
On a more serious note, don't forget to talk about the R value VS temperature of the different material.
If i remember correclty, we discussed about XPS being a poor performer during cold weather because of the trapped blowing agent liquifying ...
Also i've been quoted at lower prices here ( quebec ) for iso than even EPS type2 on a compared R value unit.
XPS increases in R with falling temp, polyiso drops a bit but at the average winter temps in an zone 4a climate those differences are "in the statistical noise" of construction errors.
At an average temp through the foam of 25F iso rated at R6.5/inch might have fallen to R6/inch, and R5/inch XPS may have risen to R5.5/inch.
But the average wintertime OUTDOOR temps in zone 4 locations is above 30F, and the wintertime average temp through the foam layer would be over 45F, at which either are performing much closer to their labeled ATSM C518 R values, tested at 75F average temp. I don't consider foam-derating for temperature very useful except in places with average January temps lower than 15F or so, which would be climate zones 6 & higher.
In Quebec I'd definitely be derating iso for mid-winter temperature averages, depending on how thick the foam is. When it's over half the total rated-R derating for temp is less important than when it's a quarter of the total R or less, since the average temp of the foam is lower when it's just the outer skin. In a US zone 4 layer with ~43% of the rated-R as exterior foam as in this case, derating is a meaningless exercise- there are bigger inherent errors to chase down, and from a dew point control point of view the assembly already has huge margins.
If HVAC cost is cut by 20%, probably best case as Dana noted, and HVAC runs 50% of total bills, that works out to just 10% of total energy bill...yawn...not much drama there.
Sorry to hijack ur thread here .. but Dana, weren't we discussing about the american used blowing agent for XPS being trapped long time in it, and liquifying at minus something celcius and altering the insulation value of XPS badly , a few week ago ??
How does polyiso perform worse in cold temp when most of its blowing gaz ran off after only a few months ... ???
someone can point the thread ???
XPS has to be VERY cold before it passes the center hump and starts losing R. Polyiso not so much. The theoretical basis isn't very intuitive (for me, anyway), but as a measured empirical fact, that's the way it works at temperatures we're likely to see for outdoor temperatures in places humans inhabit.
For what happens to XPS, see figure 3 (the HFC 134a curve.)
http://www2.dupont.com/Formacel/en_US/assets/downloads/h54876_temperature_effect_on_R_value.pdf
Most foams are blown with a mixture of gas & liquid blowing agents to avoid the condensation curves seen in figure 2.
The pentane used for blowing EPS & polyiso condenses at about +35C, so it's already on the down-slope at normal heating-dominated climate outdoor temps.
Curt: That 10-20% heating energy savings less of a yawn if you're heating with $4 heating oil or $3 propane in a 7000 HDD+ climate than it might be in a warmer climate with cheaper heating options. We're not sure what Pete Strohs' heating fuels are, but in a zone 4A climate there are more heat-pump options than in zone 6 locations.
In zone 4A taking it all the way to R-20-25 whole wall is probably going to be cost effective only in a longer term financial analysis, but there can be a rational basis for those values, using table 2, p10 of this document as the rough guide:
http://www.buildingscience.com/documents/reports/rr-1005-building-america-high-r-value-high-performance-residential-buildings-all-climate-zones
Pete,
I like that last response from UBX, written in secret code--there may be some really good advice in there.
Anyway, a lot of people who come to this website need to find out how easy it is to answer questions like yours for yourself. It is really easy and FREE to download the energy software BeOpt, and it's easy to try all sorts of options to see how they affect energy usage. It will take you just a little time to enter some information and download a weather file for your area, but after that trying options is really quick.
Check outhttp://beopt.nrel.gov/。什么比实际得到佛r your federal tax dollars. You're paying for BeOpt, anyway, so why not use it?
You could have spent less time getting answers for yourself using BeOpt than it takes you to read all these responses, sort out what's good and what isn't, just to end up with an incomplete analysis.
You don't get dramatic energy efficiency in buildings from just throwing more insulation into walls. It comes from attention to many details--there's many small pieces working together. Software like BeOpt makes it easy to handle all those details.
I