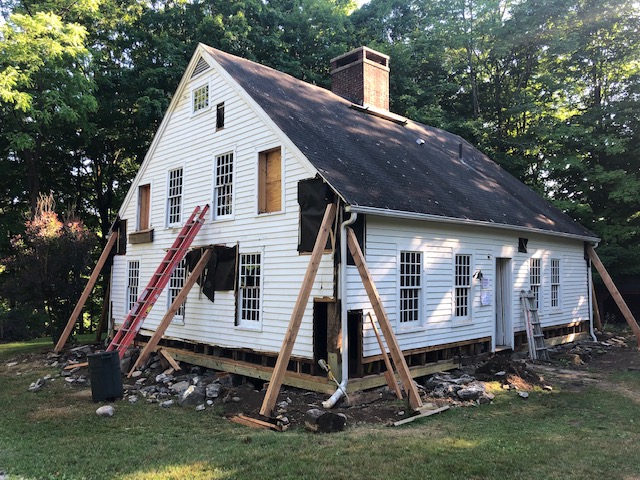
Built c. 1780, this timber-framed house sits on nearly 200 acres in Washington Depot, CT. The client purchased the property in November 2019, and it has been in the hands ofHudson Valley Preservation(HVP) ever since. The primary goal is to make it a net-zero-energy home. Because of its age and condition—not to mention six fireplaces—a deep-energy retrofit was the only way to get there.
The house was built using plank-frame construction methods. Originally, it had a timber frame with walls made of 1-1/4-in.-thick vertical oak planks running from sill to plate; the vertical planks were in lieu of studs. (This type of construction dates to the 17th century, and is most often seen in Massachusetts, Rhode Island, and New Hampshire.) Here, the planks were nailed to the exterior of the timber frame; wood clapboards were used for exterior siding; and interior lath and plaster were applied directly to the planks. There were no wall cavities, and there was no insulation.
A major renovation around the turn of the 20th century got rid of nearly all of the planking. The carpenters added studs and built some interior walls on the first floor. Today, those walls and doors are relatively plumb, whereas nothing else is. In 1972, a second remodel concentrated on the second floor, and resulted in all of the partition framing that is there now.
HVP Founder Mason Lord speculates there was some kind of event that made the house shift 4 in. to the north. To correct that, on the north and south elevations—the eave sides—HVP will add tapered studs to the exterior of the existing tongue-and-groove white pine−board sheathing. The idea is to shim the walls from 0 in. to 4 in. on one end, and vice versa on the other in order to plumb them…
This article is only available to GBA Prime Members
Sign up for a free trial and get instant access to this article as well as GBA’s complete library of premium articles and construction details.
Start Free TrialAlready a member?Log in
12 Comments
I’m sure there has to be a sequel for this project. To me, it’s really interesting to learn how other types of construction work, that I don’t have a clue about, are done, and more impressive at a NZE level remodel. I feel this piece is just a teaser, and I find myself wanting further information, from the Owner’s perspective, the reasons for this project. Why? Romanticism? Economic sense? Historical preservation? Never mind that the original house survived two previous remodels, neither historically nor building science accurate.
By the time the house is fully redone, it’ll be a semi-new house, with old bones, and a new coat of paint. If the house shifted 4” in any given direction, there has to be some structural issues, which unless addressed, there is a good chance it will happen again. Unfortunately, there may not be pictures of the original wall framing, and that would be a shame not to fully understand the total scope of the project. I also wonder about original floor plan vs. new remodel.
It appears that this project still under construction, somehow I feel wanting to know “the rest of the story”, as Paul Harvey gallantly used to say. Hopefully, we’ll get to read the sequel, with plenty of pictures… you owe us, Kiley! ;-))
For sure, Armando! It's close by, so I plan to follow this project. Feel free to email me directly with questions you'd like to see answered. I'm not sure if the homeowner wants to be involved in the coverage but I will find out for sure.
Hi Armando,
The owner is a very private person, so we won't get a direct response, but please read my answers to Hugh below which may shed some light on your quest for information on the project.
In addition:
-We have stabilized the structure by replacing rotten sill beams and reinforcing the roof structure taking load off the eave walls.
-The floorpan is the late 19th century layout on the first floor which would be close to the original 18th century with some modifications. The most significant change is the location of the stairway to the second floor. The second floor floorpan takes its shape from the 1972 remodel. Again, not far off from the original.
I've enjoyed your participation and input into BS & Beer on Thursday evenings.
I've a similar project on hand. Want to be sure I understand this wall assembly. Inside out ...
Interior wall finish
Vapor retarding membrane?
Interior dense pack cellulose
Sheathing
Siga 500 SA WRB
Exterior wood fiber insulation
Rain screen / vent
雪松木瓦。
Got it?
Yes, that was my understanding of the assembly as Mason described it, although I've asked him to hop on here and confirm that, when he has a moment. I'm curious to hear more about your project, if you'd like to share.
I also have a difficult time understanding this project. The house definitely has a lot of charm and historic significance, and presumably the cost involved in keeping the "bones" may well be more than building new. But other than the basic exterior proportions and scale of the building, it appears that they are covering up old structure...the picture of the old beams with metal connectors and new joists running parallel, I found especially appalling...What's the point of trying to restore an old house if you never see the old?
Wooba
Close:
Interior wall finish
没有蒸汽缓凝剂。我们想要的屁股embly to dry to the interior and since we have the exterior insulation condensation not a concern. Good question and possibly a hick-up with the building inspector.
Dense pack cellulose
late 19th century-remodel board-sheathing
Siga 500 SA WRB
On the eaves-Tapered studding and then plywood sheathing to plumb the walls for window and doors. (not on the gables). These cavities also get dense pack cellulose.
Exterior wood fiber sheets.
1x3 strapping for rain screen gapping.
Boral clapboards.
Thank you Mason. My main question was with the interior vapor retarder. I am facing the same issue in zone 5 MA. Will the building inspector require it.
I am curious re: the choice of Siga 500 SA versus Blueskin (VP160). My math had the former coming in at twice the cost of the later. I could not justify it. We went the Blueskin route.
Also curious what drove the selection of Boral clapboards versus Hardi Plank, LP Smart Side, Cedar, etc. TrueExterior is telling me they have discontinued clapboard siding.
Hugh,
It is always challenging in an old house to decide how far to go and where to make compromises. It is a rare client that invests this kind of effort and funds into a home like this.
Some reasoning:
-As you point out the house has charm and historic significance.
-The property is secluded and private.
-The original timber frame survived as well as six fireplaces and some original paneling in the two parlors. Original oak flooring also survived. Not much historic fabric besides this survived.
——地板托梁你指的是骇人听闻的will again be covered with plaster as they were originally. The structural upgrade will make for a solid floor system in the bedrooms and bathrooms as opposed to a woefully undersized structure with sags and a lot of bounce. The old timber frame will remain visible in the basement, attic and knee-wall eaves.
-With the improvements and upgrading to high performance, maybe this charming old timber frame with history, will survive another 240 years, adaptively "reused" as comfortable, healthy and joyful to inhabit.
I am impressed with the condition of this house after 240 years in a high moisture climate. The builder did some things right. It amazes me to see these old structures, barns especially, knowing it was all built with hand tools and no modern scaffold. What a source of pride these buildings must have been for the farm families.
Doug,
This house was the "dwelling house" -as described in the land records-was home to the owners of the mills on the river below. The first mill had a 200 foot dam, 8 feet tall. from the 1850's until 1951, a factory made Scythe Rifles. A scythe rifle was a small sharpening tool for field workers to carry in their pockets when in the field cutting hay. We found a 48 inch long scythe blade buried in the wall of the house
That's fascinating. I have a whetstone for my scythe, but hadn't heard of it being called a rifle. So I did a little reading and learned that a rifle was a sort of sanding block version made by cementing abrasive powder (sand or emery) to a curved wooden block.
Farming books circa 1850 were are passionate about the importance of proper sharpening as the comments on a Fine Woodworking YouTube video.
"More good scythes arespoiledandworn out,and rendereduselessby improper grinding and careless whetting, than by all the grass and grain which they cut."
--Young Farmer's Manual, by S. Edward Todd, 1860
Log in or become a member to post a comment.
Sign up Log in