2×8或I-joists TJIs for my floor framing
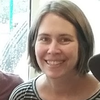
My floor joists don’t need to hold insulation (unless I add some later for sound insulation) because my crawlspace has insulation outside the stemwall.
I could use 2x8s at 16 o.c. and spend $612 on lumber. Or I-joists 9.5 inches deep, 24 o.c., and spend $894.
-Are I joists kinder to the planet? In terms of trees used it seems like yes, but what about processing footprint?
-Are I joists a lot easier to use? I know they’d be lighter and more uniform than 2x8s. 2x8s can vary a bit in depth, but it seems relatively easy to modify the depth at the joist hanger if necessary so that all match. More annoying to deal with: twist, bow, cupping, etc. Might it come down to the quality of lumber I can get? I can get kiln dried 2x8s. I know to put all joists crown up.
-cost of hangers seems comparable. I’m hanging the joists from the sill plate using top flanged hangers, which apparently has the advantage of eliminating a rim joist, which is apparently expensive for I-joists.
-2x8s give me a little more headroom in the crawl space. but I’d still have about 30 inches even with the I-joists.
-the joists will be ~18 feet long, with a beam to support in the middle. Plans don’t seem to make clear but I assume the beam is under the joists, not at the same height (so not requiring joists to be cut).
-since crawlspace is conditioned, I think plumbing and electrical won’t have to be punching through the joists. (I believe I joists are easier to poke holes in than 2x material.)
Are there other things I should consider? I look forward to getting some more perspectives.
Thanks everyone!
Paula
GBA Detail Library
A collection of one thousand construction details organized by climate and house part
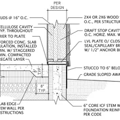
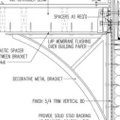
Replies
I Joists require far more work. There are a lot of extra web stiffeners that may be required depending on who designs the floor assembly. I will say, save yourself the trouble and do not hang the joists with a top mount hanger off the sill plate. The floor will be weak along those edges. Eliminating the top mount hangers and the associated labor and add back in the rim board and it will be a wash. Also keep in mind if you have any fuel fired appliances in the crawl space the underside of the TJIs or 2x8s will need to be fire protected per code. Make sure the center support beam is a dropped girder and not flush. Any chance to avoid hangers you want to do so.
Definitely was thinking the center beam would be a dropped girder. And no fuel fired appliances in the crawl space (maybe a dehumidifier).
I decided to suspend the joists in order to bring the floor of the house down 7 to 9 inches, which seems valuable in terms of not having more steps up from outdoors. However, the concerns you raise about strength do seem valid.
When I decided to go with the suspended joists, one approach that was suggested was to have an extra ledger mounted on the top inside of the stem wall, so that the joist hangers can be mounted on that. It's a whole another 148 feet of pressure treated 2x8, so I'd hesitate to do that unless there is strong support for that here.
I don't recall my building inspector being emphatic about either approach. Can any one else weigh in? Just read this thread.//m.etiketa4.com/question/hanging-floor-joists-hanging-or-on-top-of-foundation-wallMy situation is similar: the site slopes so I'm 6 inches above grade on the uphill side, and about 4 feet up on the downhill side.
I am about to frame this exact same floor design myself, 9 1/2" I-joists, drop beam, joists hung off a ledger on the interior wall. The ledger (LVL) was a requirement specified by my engineers and they also specified blocking at 4ft OC for the first three rows. I'm near Vancouver, BC for reference. I went with this (plus Advantech for the sub-flooring, despite the cost premium here) for the peace of mind of having a flat squeak free floor that could tolerate some moisture during construction. I've found with my limited experience, the additional cost in using some widely recommended materials (ie Advantech) is worth the peace of mind and fewer things to concern my already full brain with.
Just looked at some of your other posts and we are building very similar houses (size, climate zone, grade conditions) and considering many of the same questions. Let me know if you would like to see any of my plans and swap ideas.
Also, not sure what your plans are for mechanicals/heating but I found the Minotair Pentacare unit to be cheaper than a higher performing HRV and ductless minisplit, plus it dehumidifies and will provide more even heat distribution than a central minisplit. I'll run an exhaust from the crawlspace to mitigate the unlikely event of moisture.
Blocking the first three rows in a TJI floor system is completely unnecessary and a waste of money. That is part of the advantage of TJIs over dimensional is they don't need blocking. Chances are the engineer is not familiar enough with this type of system or they are not running the floor system through the manufacturers software.
It's a very experienced engineering firm and the blocking is not at all uncommon in this area. Even if they are wrong, it's what they've specified and the lumber is sat next to my foundation.
I-joists are kind of scary for floors in the case of fire, because the OSB web can burn much quicker than a solid joist would, and without the web the i-joist drops to almost nothing strength-wise. I think open web joists are the best option. Much less material than solid wood, stronger, and you won't have to drill any holes to route pipes, ducts, drains or wires. We were able to do a clear span of 27' with no support using 16" open web joists. Unfortunately, I just looked this up, it doesn't appear you can get them in anything smaller than 11 7/8" deep.
In my opinion the, I joists will go in faster give you a flatter floor that is less likely to have squeaks and gowns.
我最大的缺点是负载washi前面ng machine will shake the floor a lot. I suspect that the weight and mass of solid joists would absorb that energy. If I had to do it over I would put 6 solid under the washer.
The fire thing is true but for me with a rural volunteer fire response and I joist I am guessing any fire I can’t deal with will total the house. In a lot of was starting over is more appealing than a restoration.
Walta
You didn't specify it but a third option which I really like would be floor trusses. Super quick to install compare to Ijoists although a bit more expensive.
Paula,
I'm not sure those are the most comparable alternatives. Why not compare similar depth materials, or those the both allow the joist spacing you want? Do 2"x8"s and the I-joist have the same deflection at your spans?
Going to 24" spacing means you will have to use a lot thicker subfloor to get comparable stiffness.
我被告知,我托梁不进来我7.5nch depth, that 9.5 was the smallest depth available (at least from my lumber yard). I agree that I'm probably comparing apples to oranges. As a relatively inexperienced builder, perhaps using 2x8s or 2x10s is more straightforward? I don't want surprises and I've already built with 2x joists before, but never I joists.
Is the strength at the edge of the floor a concern? I used 2x8s at 24 inches for a 12 foot span, supported in the middle, and it feels fine. I think I used 1 inch thick plywood for subfloor. This floor could be 2x10s at 24 spacing, or 2x8s at 16 inch spacing, with an effect span of 9 feet. plans called for a minimum of 7/8 plywood subfloor. I can see that while the lumber price of 2x8 and 2x10 were both similar, the 16 inch spaced 2x8 floor would effectively save money in the floor decking.
It sounds to me like none of these options is terrible. I do want the whole assembly to be strong, as on the west coast we have the "big one" earthquake to worry about.
I-joist all the way. It will be way stiffer and flatter than the 2x8 floor. TJIs also have no radial shrinkage, which is important if you are going to drop the joists. Provided the installer is careful and you do a bit of shimming the floor will be just fine.
You also want to continuous span the full width of the house (install 18' TJIs). This makes the floor significantly stiffer.
Washing machines are always a challenge. It is best to place it near a load bearing wall. If not possible, drop a small post down or double up the floor joist underneath it. I also always install 1" rubber pucks under the washer's feet.
Kiln dried 2x8 or 2x10 wouldn't have radial shrinkage, though, right? Or will that still be happening a little? (The installer is me, and I am careful.) Continuous span definitely.
Washing machine is a good thing to think about. I have it close to the center beam, which should help.
My designer approved 2x8s at 16 inch spacing. I looked at the FORTEWEB software and don't have the bandwidth right now to learn how to navigate it. I was told either 2x10s at 24 inch spacing (with 7/8 plywood min), or else 2x8 at 16 inch spacing (with 3/4 plywood). I am assuming that for a 9 foot span (8.5 foot really) that these are adequate numbers, and that I will pay in some fussing for the inconvenience of dimensional lumber as opposed to the I joists which would be more reliable dimensionally. I will definitely glue & screw down the decking.
The 2x8 and 2x10 joist pricing is virtually identical but the price of plywood for both is where there's a big difference.
One reason there's a price difference is that I wanted to avoid using OSB. There is no 7/8 plywood (at least at the stores where I'm getting prices) and 1 1/8 plywood is $47/sheet, where 3/4 plywood is $30/sheet. That's almost a $500 savings in cost for floor decking if I go with 16 inch spacing. I could certainly overbuild this house, but how green is overbuilding? I have overbuilt a lot of things already. At some point it's wasteful. At the same time I would like my floors to be solid. If I wanted to go nuts I could do 2x8s at 12 inch spacing and 3/4 plywood. That would only cost about $250 more than 2x8s at 16" with 3/4.
Like I said above with my generous conditioned crawlspace, there is no need to drill through joists. Plumbing and wiring can just go around them.
What I'm learning is that there's a ripple effect in terms of how choices made create more cost in other components that you weren't thinking about at the time you made a choice.
I don't want OSB in the building since I'll be building slowly and don't need to be stressing about moisture damage in the partially built home.
I generally go for OSB for floors. It is flatter and cheaper than plywood. Unlike walls where you have to worry about moisture and nail holding, there is no real benefit for plywood for floors.
KD is better but will still shrink a bit over time, TJI will not.
For your span, you are near the limit for 2x6 16OC, so your 2x8 floor will be plenty stiff.
It does feel that the 9.5" a bit of an overkill for 9' span, for me they are easier to work with, for a couple of extra bucks you get a better floor. Also much easier to run wiring/ducting/pluming through it.
P.S. Your cheapest/simplest would be clear spanning the 18' with 11 7/8 I-joist without a center beam. This would save the cost of the center beam plus supports. This would definitely be bouncier though.
Thank you Akos! I had a leak in some plumbing in another building, and had water sitting undetected for a week (I don't live there yet). That experience is what made me not want to have OSB in my floors. Am I wrong to think that OSB would be more vulnerable in a situation like that?
I appreciate your response!
Generally, when it comes to big leaks, the material of your sub floor is the least of your concerns. Plywood is more robust, but chances are you are pulling the flooring out anyways.
OSB is left uncovered for pretty long time at job sites before the the building is dried in and it holds up reasonably well. I have an OSB platform in my utility room which has seen water leaks over the years, still holding up quite well.
Plywood is worth it you need to carry it by hand up a bunch of flight of stairs (or hanging sheets off a ladder). There, the weight savings is worth the extra cost.
Not all OSB products are the same. I feel the Advantech subfloor is very different than the generic OSB.
I used my Advantech scraps as stepping stones in direct ground contact in the rain for 7 months, I could see no change in the product.
Walta
The OSB web of TJIs is like a fuse in a fire — it fails with little if any warning. This is from my local fire marshal while we were talking about some things. He said regular 2x joists make a lot of noise before they fail, which gives warning you need to get out.
You need to be VERY CAREFUL how and where you cut holes in the web of engineered joists. Everything is more critical. The upside is that they are straight and true, and stiffer. OSB makes efficient use of wood too, so it’s a green product in that regard.
Regular joists are less critical in terms of where you drill holes for wiring, and they’re easier to fasten too since you can attach anywhere instead of just on the chords of an engineered I joist. The downside is regular framing lumber has all of the usual defects you see in wood boards, and it’s not as stiff.
I would try to make a stiffer floor. Don’t go on the minimum end of the span tables, be a little kore conservative to give yourself some extra strength. This is something that is difficult to change later (I’m in the process now of sistering a bunch of 14 foot 2x10s to get the floor stiff enough for tiling). I like solid blocking over X braces too. 2x8s sound pretty small to me for the spans you’re considering, even with that center beam. If I was building this, I’d probably step up to 2x10s and use conventional lumber. I’d probably use. doubled up LVL for that beam, but a steel girder or built up beam of MSR 2x10s or 2x12s might be cheaper. I’ve found that LVL is a great product for beams and headers, but is not always the most economical option.
Bill
Paula,
Great discussion!
I like both...
I-joists are flat and stiff and can span longer distances. You can cut larger holes in I-Joists so this can be helpful with ductwork.
The downside is that they are more expensive. Remember, you will also need engineered rim boards which will cost extra. Fire is another issue as already discussed. To give you an idea, you would need TWO layers of Type C (!) drywall with perpendicular seams (taped and mudded) just achieve a one hour fire rating. I believe a mere 5/8 type X drywall will give you a one hour fire rating for 2x8 joists.
Framers dislike cutting I joists but they prefer attaching subfloor to them over 2x given the wider surface area.
Given your shorter spans, I'd probably just go with 2x8 joists. Make sure to use the Huber glue and a 3/4" or 1 1/8 subfloor. This well help with stiffness.
I'm not sure the fire resistant characteristics of I-joists vs dimensional lumber makes much difference. If the fire has made it's way into the floor structure it is very likely fully involved, and no one will fight the fire from inside the house anyway. The chances of saving a house based on one or the other floor system isn't really much of a factor.
Since I’m one of the ones who brought this up, I’ll say I agree with Malcolm. By the time the joists are burning enough that they’re going to fail, your house is doomed. The fire marshall was telling me the TJI joists are an issue if the firefighters are inside your home while it’s burning, which is pretty rare. If you ask a fire Marshall their favorite type of construction, they’ll probably tell you they like commercial concrete and steel buildings best since they’re most fire resistant. I wouldn’t make your decision about what type of joist to use based on fire resistance here.
Bill
As far as deflection and floor quality, run the assembly in ForteWeb and do a calculation. Never go by span charts as they are worst case that barely passes code minimum. A good quality floor you want around 3/8" of Total Load Deflection. Anything more than that you are going to feel the bounce. Using a quality subfloor such as Advantech, a good adhesive, and screwing the floor down versus nailing all make a huge difference as well. 9.5" is the smallest TJI that is available from Weyerhaeuser, not sure on other manufacturers. Floor trusses are not cost comparable to TJIs until you get into the 16" depth range. You could do a top chord bearing floor truss which would put 3" of top chord on top of your sill plate, but top chord trusses are far more expensive that bottom chord bearing trusses.
I don't know the code regarding crawl spaces, but for basement areas, code requires TJI's to be fireproofed in one of a variety or ways: sheetrock ceiling, insulation on webs, intumescent paint on webs, etc. Typically, dimensional lumber need not be fireproofed. Biggest advantage of TJI's is that they created straighter and more level floors....also lighter and easier to install, capable of longer spans at similar depths.