Air barrier for compact, low pitch, unvented roof

Hi GBA community!
I am renovating a 1965 ranch where the existing roof assembly (1.5:12 pitch) is:
– exposed 2×6 car decking that extends to the exterior to create generous overhangs
– tar paper
– 2.5” fiberglas faced polyiso
– 20-year old hot mop built up roofing
My tentative plan for the new roof assembly is:
– leave 2×6 car decking as is
– hybrid roofing underlayment for air/vapor barrier (mechanically attached, but nail sealing)
– 4” of new fiberglas faced polyiso
– salvaged 2.5” fiberglas faced polyiso
– 1/4” DensDeck Prime for fire rating
– 60 mil fully adhered black EPDM
Will the new underlayment improve the air sealing of the assembly? It will be quite a bit of work to pull up the original polyiso, so I want to be sure it is worth the effort. I know that tar paper is the original “smart vapor barrier” but I haven’t been able to determine if it is an effective air barrier.
Also, does it make a difference to the thermal performance whether the old or new polyiso is closest to the interior of the home?
Thanks in advance for your feedback!
Les
GBA Detail Library
A collection of one thousand construction details organized by climate and house part
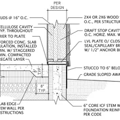
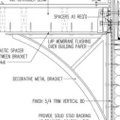
Replies
Les,
The big problem with your roof assembly is the roof sheathing. When a ceiling made of 2x6 boards extends from the interior to the exterior to create roof overhangs, you end up with hundreds of little air leaks. Between each board is a crack, and these cracks allow exterior air to enter your building.
The only good solution to this problem is to install a drywall ceiling on the interior side of the board ceiling, making sure that the drywall ceiling is sealed to the drywall on the walls with paper tape and drywall compound. Even when this is done, you still end up with air movement through your roof assembly, which is far from ideal.
I suppose if you like the look of a board ceiling, you could re-create it with applied 1x6 boards installed on the interior side of your new drywall ceiling. But that's expensive.
In your old assembly, the "tar paper" (asphalt felt) had nothing to do with the air barrier. The air barrier was the roofing. Hop-mop built-up roofing is an excellent air barrier. The problem was that this excellent air barrier was installed on top of a leaky ceiling.
In your new assembly, you also have an excellent air barrier (the EPDM roofing). But your new excellent air barrier won't do you any good unless you solve the leaky ceiling problem.
Q. "Also, does it make a difference to the thermal performance whether the old or new polyiso is closest to the interior of the home?"
A. No.
Martin,
谢谢你的快速反应。这就解释了为什么it is so hard to keep the house warm in the winter! The interior car decking is still natural so it would be a shame to cover it up.
Would it be possible to minimize the air leakage from the car decking by caulking the grooves on the underside of the gable overhangs (which are already painted)? If I removed the fascia boards, I could also caulk the cut ends. With the EPDM on top, would that effectively close off the air leakage pathway? Or would I have to caulk the top side as well up to the point where the decking crosses into the interior space?
我当然希望我的投资在另一个4” of polyiso isn’t negated by this leaky ceiling problem....
Thanks for your thoughts on this,
Les
Les,
Caulking as you describe will reduce but not eliminate the air leakage. This is really a tough problem to solve, unless you are willing to install a new interior ceiling (and, ideally, interior insulation -- although that's rarely done).
Les, I'm designing a renovation right now with a very similar roof detail. I had the same concerns as Martin, so I've spec'd a self-adhered membrane over the existing 2x roof decking, wrapping down over the rakes and eaves, and adhered to the wall sheathing to seal the ends of the 2x decking. I've spec'd Henry Blueskin VP100 as the air barrier but other products would also work. If you have rake overhangs you would need to either cut them off, or wrap the self-adhered membrane fully around the overhang to seal the decking against air infiltration. (My project has no rake overhangs but we'll be adding them with the new roof overlay.)
What climate zone are you in? Your roof assembly is about R-38, including the wood decking, which meets code for new construction in zones 1, 2 and 3, but not in colder zones.
Michael,
Good solution! It's obviously easier to restore the overhangs (soffits) to look good than it is to rebuild the entire ceiling.
Thanks, Martin. There is still potentially a thermal bypass at the ends of the grooves in the ceiling boards, but strips of foam on the exterior will solve that.
In this type of construction, there is often a beam that aligns with the top of the exterior walls. I've never done this but....How about cutting a groove through all of the car decking, about 1/4"-1/2" wide and centered on the beam, so you've still got adequate bearing on both sides of the beam. You should probably make sure the decking is nailed off on both sides of the new groove. Then fill the groove with either spray foam or a good structural sealant. Acoustic sealant if you must. This would serve to cut off the air channels and create your air barrier without removing anything significant. Then run your self-adhesive air barrier underlayment right out and over the groove and sealant to the eave edge. Maybe not perfect, but it should be better than what you've got, and it should be pretty durable.
Martin: given the age/construction of this home, I have come to the realization that it will never win any PassivHaus awards (without crazy additional investment). So if caulking is a 80% or even 50% solution, I’ll be happy with that. When it comes time to Sheetrock the interior, I will definitely consider covering the car decking.
Michael: your approach sounds fantastic, but unfortunately I can’t follow in your footsteps since I made the mistake of upgrading the walls/windows/siding first. At the time, the roof still had plenty of life in it so I focused on replacing the single pane, aluminum framed windows and adding exterior insulation to the 2”x4” walls. Now I know better...!
I’m in climate zone 5 which calls for R-49 in new construction, but the building inspector will accept R-38 of continuous insulation for a renovation. Rather than add even more insulation topside, I plan to invest in a ductless mini-split since currently the only heat source is a wood stove and there is no air conditioning (other than sitting in the basement!).
Coming back to the air barrier for a moment...if I’m understanding correctly, the air loss is occurring horizontally along the plank grooves rather than vertically through the roof assembly. If so, then is there any benefit to pulling up the existing layer of polyiso in order to replace the tar paper with a fancy air/vapor barrier?
While I have the roof “unbuttoned”, I want to improve what I can, but if it won’t make a difference to controlling air flow, then not having to do this step will eliminate a lot of additional work.
Thanks again for your feedback/suggestions/encouragement!
Les,
Q. "Is there any benefit to pulling up the existing layer of polyiso in order to replace the tar paper with a fancy air/vapor barrier?"
A. No. Your planned roof assembly already has several air barriers, including the impenetrable EPDM roofing.
You are correct that the air leakage you need to worry about is horizontal leakage through the tongue-and-groove joints of your board ceiling.
The caulking work you propose will be fussy, time-consuming, and expensive, and will (I fear) have disappointing results. But I understand that with an old house, sometimes you have to throw in the towel and admit defeat.