Details of cathedral roof with rigid exterior foam
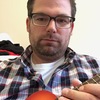
Okay, I was thinking to go with a roof insulation make-up as shown in the first attached image. But I am realizing that it is going to be super expensive for all that spray foam. So I am reconsidering the potential of going with exterior rigid foam. But I want to make sure I get the details correct. I also want to be able to get a pretty good idea of which type of assembly would be cheaper.
This is for climate zone 6b.
1. In the county where this house will be built, code is enforced to 2003 IBC. Can I still go by the requirements in the 2015 IRC?
2. The 2015 IRC R806.5 confuses me a bit as far as whether the required exterior insulation is R-25 (as per the table) or whether it must be calculated using the temperature method in order to keep the underside of the sheathing at least 45 degrees F. Which calculation method do I use?
3. If the required exterior rigid foam R-value is 25, is that based on an R-49 roof? What if I want an R-60 roof? Does the exterior insulation then need to be increased proportionately?
4. With R-25 exterior insulation, I would be left with an 11 7/8″ rafter bay cavity to fill. My understanding is that the interior insulation needs to be in contact with the underside of the sheathing. Am I correct on that? If I fill that whole bay with cellulose or batt insulation, I am going to end up with approximately R-40 of interior insulation, making the roof insulation R-65 (or much higher if the rigid foam R-value has to be proportional to the interior insulation). Any suggestions for how to deal with this? I would think that going beyond R-60 would probably be a quickly diminishing value vs. the cost.
GBA Detail Library
A collection of one thousand construction details organized by climate and house part
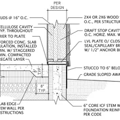
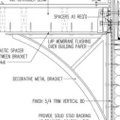
Replies
Hi Brent.
Your first question is one for your local building official. I'll go out on a limb and say that the 2015 IRC has greater energy efficiency requirements than the 2003 IBC, which would then satisfy the local inspector, but I'm not sure if that is true.
The IRC table 806.5 is a prescriptive code, which means that an inspector using the IRC will likely accept the listed R-values without further computation. But remember codes offer minimums (in most cases safe minimums), but high performance builders tend to build beyond code, particularly when it comes to building envelope details like thermal layers, condensation control, air tightness, etc.
In assemblies with an air-impermeable layer like rigid foam or spray foam combined with a fibrous layer of insulation like fiberglass and cellulose, you can typically increase the R-value of the rigid or spray foam layer without increasing the R-value of the fibrous layer, but not visa versa. If you increase the R-value of the fibrous insulation layer, you will need to calculate the necessary layer of rigid or spray foam. See this article:Calculating the Minimum Thickness of Rigid Foam Sheathing
I would think that before you think too hard on your last question, you should get cost estimates, to determine if it is actually an issue worth putting much time into.
Exterior insulation (or SPF) gets pretty expensive as you go up on R value. There is generally very little cost benefit going above code min on U factor basis. For example with exterior rigid insulation you need around R38 roof.
Say 0F design temperature, roof on a 3200sqft house (so around 4000sqft of roof depending on slope).
With an R38 roof you loose ~8000btu through the roof
With an R50 roof that is 5600btu.
You would be very hard pressed to recover the cost of extra rigid insulation to get to R50 in energy savings.
High R value only makes financial sense if your insulation material and install cost is low, pretty much blown in insulation or maybe batts.
Is the 11-7/8 required structurally? If not, downsizing would seem the obvious solution. Assuming it is, I too am curious how to make sense of that stack-up.
It is my understanding that it's best for your air barrier to be rather tight to your insulation, i.e. if the insulation doesn't fill the rafter bay, you'd want to tuck an air-barrier up in against it.
I honestly don't know why this is and would be curious to hear someones explanation on the matter. I've yet to find a succinct hygrothermal explanation for the issues surrounding insulation and air-barrier coupling / decoupling in this regard.
As far as the percentage of exterior rigid: yes R-25 is based on R-49 total. The minimum percentage of exterior R to total R for climate zone 6 is 51%.//m.etiketa4.com/article/combining-exterior-rigid-foam-with-fluffy-insulation
So if if you had R-40, below, you'd need somewhere around R-42 above deck.
Is there a good way to insulate the rafter bays with fluffy insulation, have it in contact with the underside of the sheathing, but not full the whole rafter bay with it? Like with 11 7/8” I-joist rafters - I wouldn’t need (or want) the full R-40 of fluffy insulation. How could I just do R-28 or R-30, but have it held up in contact with the underside of the sheathing (assuming that is necessary)?
You do want the insulation against the sheathing, definitely no gap there. There is no problems with a gap on the warm side.
You can get craft faced insulation for either metal stud or for cathedral ceiling that is 24" wide. Staple the facer against the side of TJI to hold insulation in place. The craft facer in this assembly is not an issue as it acts a smart vapor barrier.
The other option is the spring wires but I'm not sure if they make ones for TJI width, most are for 2x lumber.
You can also go with the correct width mineral wool batts (actual 24" wide), those are self supporting and will stay put on their own. You would have to do a bit of trimming though beside the TJI flanges to get it to sit flush with the roof deck.