Dew point of a dense-packed wall

我是一个低成本住宅设计师工作single-family home in Climate Zone 5/4 Marine (South County, Rhode Island).
2013 ECC dictates an R-Value of 20 or 13+5. My proposed design for the wall is 2×6 framing with blown-in cellulose, and 1.5″ Zip System as sheathing and vapor barrier. While this meets the code requirements, does this pose potential moisture problems?
Thanks,
Devon
GBA Detail Library
A collection of one thousand construction details organized by climate and house part
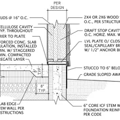
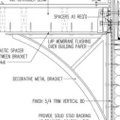
Replies
Devon,
Rhode Island is in Climate Zone 5, not Zone 4.
Read this article for the answer to your question:"Calculating the Minimum Thickness of Rigid Foam Sheathing."
For a 2x6 wall in Zone 5 with exterior rigid foam, you need the foam layer to have a minimum R-value of R-7.5. Since 1 1/2-inch Zip R sheathing has an R-value of only R-6.6, your wall won't work. You need thicker rigid foam.
RI is the warm edge of zone 5, and R6.6 will almost certainly work (especially with cellulose, which redistributes the moisture) even though it would be a code violation. If you can get pre-approval from the code inspectors it's not very risky at all.
Rhode Island code is currently based on IRC 2012. The relevant section of code did not change in later versions. From IRC 2015:
https://up.codes/viewer/wyoming/irc-2015/chapter/7/wall-covering#R702.7
-----------------------------------
"R702.7 Vapor Retarders
I或II类蒸汽情况下是必需的interior side of frame walls in Climate Zones 5, 6, 7, 8 and Marine 4.
Exceptions: 1. Basement walls. 2. Below-grade portion of any wall. 3. Construction where moisture or its freezing will not damage the materials."
------------------------------------------
To comply with that portion of the code with only a Class-III vapor retarder (standard latex paint) requires R7.5 exterior foam, as noted by Martin:
https://up.codes/viewer/wyoming/irc-2015/chapter/7/wall-covering#R702.7.1
But with a Class-II vapor retarder it would still comply. The cheapest way meet code without increasing the foam thickness would be to use "vapor barrier latex" primer on air-tight wallboard. The vapor permeance of vapor barrier latex is about 0.5 perms, a class-II vapor retarder. It reduces the amount of wintertime moisture uptake into the cellulose to acceptable levels, while still allowing adequate drying capacity toward the interior.
I second Dana's suggestion of airtight drywall + class II latex paint. Done well that assembly should be pretty safe.
Of course, Zip does have a 2" version if I recall. It might be simpler to use that if you can get your hands on it, and it will give you a better performing wall.
2" ZIP is considerably more expensive than the 1.5" flavor, and probably doesn't meet the structural requirements for sheathing in stormy-windy coastal RI.
It's also right on the edge in terms of thickness. Half the common framing nailers can't shoot a nail long enough to secure it to Huber's requirements.
Martin and Dana, to your points...
If I were to design a 2x4 wall w/ dense packed cellulose (~R-12.6), 1.5" Zip (~R-6.6), and foam over the sheathing with 2" EPS (~ R-7.2), would this sufficiently put the dew point outside the envelope? Also would the ZIP qualify as a sufficient vapor retarder?
Thanks for sharing your time and expertise!
Re original question: no matter what you do with external foam, it's wise to either keep exterior perms > 1 or use a smart vapor retarder. Either should satisfy conflicting recommendations for Class II (eg, Lstiburek) and Class III (eg, IBC) in zone 5. If for some reason you can't do either, then go with Class II/Lstiburek.
Vented cladding would allow Class III, but your question isn't about just meeting code.
You can also build a good, code compliant wall by putting foam on the inside.
Dana,
You are right, of course. I had neglected the coastal aspect.
Malcolm,
That is also correct. But if I recall, there was a poster on here a few months ago that had trouble finding such nails in his area, and got approval from Huber/local officials to use screws instead. The wind issue precludes this solution regardless though.
Devon,
Technically, that assembly should work. It might be prudent to leave a small drainage gap between the EPS and the Zip sheathing, though EPS drains well enough on its own it likely won't be an issue.
However, if you are going to be using foam anyway, there is not much point in using insulated Zip sheathing. It would almost certainly be cheaper to skip the Zip and use OSB and a layer or two of 2" foam instead, taping the seams. You could then do a layer of cheap housewrap, or use the foam itself as the WRB (depending on the type of foam you use).
>"If I were to design a 2x4 wall w/ dense packed cellulose (~R-12.6), 1.5" Zip (~R-6.6), and foam over the sheathing with 2" EPS (~ R-7.2), would this sufficiently put the dew point outside the envelope? Also would the ZIP qualify as a sufficient vapor retarder?"
Even without the exterior side EPS 1.5" ZIP-R has adequate dew point control to be able to use Class-III vapor retarders on a 2x4/R13 cellulose wall.
The foil facer on ZIP-R is a true vapor barrier, but it's not on the interior side of the assembly/
The ZIP-R IS the first condensing surface, not the vapor retarder keeping interior side moisture from REACHING the first condensing surface.
Aedi has it right- if you're going to be installing 2" of EPS one could go with 2x6 cellulose and standard ZIP. R7.5 is all that's needed for dew point control on a 2x6 wall in zone 5A. I'm not sure where the R7.2 presumption comes from(?).
Low density Type-I EPS would deliver R7.8 @ 2"
Type-VIII would be, R8.3 @ 2"
Type-II or denser would be R8.4 @ 2"
> The foil facer on ZIP-R is a true vapor barrier,
Huber says:
"R-sheathing is a multi layered product. The combined system permeance is 0.8-1.1 perms. The permeance of each layer when measured by ASTM E 96 Procedure B (Wet Cup) is as follows: • WRB Overlay 12-16 perms • 7/16” OSB 2-3 perms • Coated Glass Facer 45-50 perms • 1” Polyisocyanurate 1.5-2 perms • Coated Glass Facer 45-50 perms"
@ Jon R #7 and Dana #9
Based on the sources provided I'm thinking of abandoning the Zip system. I am a relative novice when it comes to perms and vapor retarder classes, but I believe I'm getting a better handle on it thanks to all of the replies.
The current design I have in mind would be:
2x6 framing w/ dense pack cellulose
osb
housewrap
2" EPS
drainage layer
siding
As Aedi suggests, change "osb" to "taped osb" and use StuccoWrap to drain away any water that makes it past the EPS. With that, you have addressed all the above concerns.
If budget were less of a concern, I'd consider plywood.
Thanks to all for the assistance! Your time and council are greatly appreciated.
A missing part of this discussion is what the wintertime interior relative humidity will be in the home. Maintaining that interior RH below 35% can make a big difference in reducing the risk of condensation on the first condensing surface in the assembly.
To economically and accurately measure RH and temperature, see this blog://m.etiketa4.com/article/measuring-and-understanding-humidity
Peter