Flat roof on doubled 2×4 rafters — Venting and insulation
We just had rebuilt (repaired) the roof of a flat roofed addition to our house, due to a roof leak and resulting breakdown and mold problems. The original roof/ceiling was framed with doubled up 2×4 joists for extra strength. So at 16″OC, each joist is 2-2x4s together. The rebuild was done the same way. It’s already a low ceiling (78″ ceiling on the low side and 87″ ceiling on the high side), so 2×6 or larger would make it too difficult to live in the space. Its a 22ft front to back x 12ft low side to high side space, with 3 exterior walls attached to the main building.
Our builder chose to enclose the edge of the walls at the soffit level to eliminate rodent risk, but didn’t inform us of issues to address such as ventilation. His theory was to create a hot box/fully sealed off cavity. Right now, it is sitting as a shell, with new wiring, sheathing, roofing and exterior Tyvek; but as yet no insulation or venting or barrier or drywall on any surface. There is also now a new roof (torch on) that has been finished. So, no work can be undone at this point because of expense and the fact that the rainy season is now officially upon us. We live in Zone 4C, I believe; about 120 miles north of Seattle Washington.
Last week, we learned online about the need for the roof sheathing to be raised about an inch or two,above the joists for ventilation purposes, or else we could be looking at doing the same mold/rot rebuild just a few years from now. Because the old insulation was actually 3.5″ of rigid foam only, and there was a leak, we have no real reason to believe that condensation was the issue. Still, we have to explore any possibility of that now when we are rebuilding.
We have learned of many opposing professional opinions as to whether to vent the cavity or not. Most pros tell us we have two choices:
1) to McGyver in some holes at the soffit level and across each joist, and use foam vent baffles for air, plus use less insulation below that (we already are sacrificing R value with the small space only being able to take 3.5 inch Roxul at a rating of R14)…this would cost us more labor and money. plus lower the already low ceiling, OR
2) use a layer of rigid foam attached directly to the underside of the roof sheathing, and stuff in the 3.5″ Roxul, along with a barrier called MemBrain by Certainteed, which we are using anyway. Ceiling height will also be lowered, unfortunately, if we can’t stuff in the Roxul and need to build/lower the joists by adding to their depth.
We will be treating every single wood surface beforehand with a spray of Seal-Once Marine Waterproofing by New Image Coatings, plus Concrobium mold prevention spray. The Seal-Once changes the structure of the wood to wick away any moisture, while allowing the wood to still breath.
But, even with these precautions, if there is a chance that condensation can form somewhere among all of these “waterproof” materials, where will it go? In an airtight space, can that even happen? Will we be looking at weeping walls and ceiling drywall because of all the moisture resistant materials and coatings inside?
We can’t get thinner Roxul, and we don’t want anything that has any VOCs in it for insulation. We are helping what VOCs may be unavoidable by using 1/2″ AirRenew by Certainteed – VOC absorbing sheet rock. on the walls, and another type of resistant 5/8″ for the ceiling.
我们一直疯狂地辗转反侧,不敢做伴奏lete this job because we are afraid of having another mistake made that will just add the costs and ultimately still end up in a rotting, moisture-laden roof cavity in a couple of years.
With regards to the MemBrain product, it says it is both a vapour and a moisture barrier in that it remains moisture-tight when humidity in the cavity is low, and increases permeability to let moisture escape when humidity is high. The escaped moisture is designed to go back into the interior of the room. It is a new type of technology in barrier materials. We are using it instead of 6 mil poly barrier, which is causing all kinds of moisture/mold issues in our climate. This is rain country, so moisture and humidity is always an issue.
Sorry to ramble on, but I am hoping to be as descriptive of the whole picture as I can, with my limited technical knowledge. We really need some help with a definitive answer or solution that will not make us feel like we have spent pointless money on what we are now dealing with. Short of litigation, we don’t know what we can do to solve this problem. It’s now October, and we are living in boxes in one half of the house, with expensive storage lockers to pay for on top of everything else. We would like to resolve things before the end of the month, if possible.
Vent or no-vent? I am strongly leaning towards no-vent, but need an answer that can be backed by solid building experience in our type of climate.
Are we using the right type/types of insulation? What is absolute best for slimline and energy efficiency and moisture resistance, with no VOCs? Tall order, I know!
Thanks for your help and advice. I will try to comprehend whatever can be offered.
GBA Detail Library
A collection of one thousand construction details organized by climate and house part
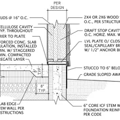
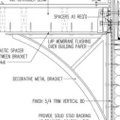
Replies
User-6940206,
First of all, can you tell us your name?
The only logical way to insulate a roof like the one you describe is with closed-cell spray polyurethane foam. This will create an unvented roof assembly. With this approach, a vent channel is not necessary. You won't get condensation on the roof sheathing with this approach.
Needless to say, you will still have a poorly insulated roof -- because a 3.5-inch-high cavity isn't deep enough for enough insulation to meet minimum code requirements. (Three inches of closed-cell spray foam will give you a roof assembly with a nominal R-value of about R-19.5. In your climate zone -- Zone 4 -- you really want to aim for a minimum R-value of R-49.)
For more information on this type of roof, see this article:How to Build an Insulated Cathedral Ceiling.
And by the way -- I know that it's too late now for this advice -- the time to plan your insulation details is before the roofing is installed. If you had planned ahead, you might have been able to install a layer of rigid foam above the roof sheathing. Now it's too late. For more information on this issue, seePlan Ahead For Insulation.
I'm not sure how to respond in this format, as I am not used to online convos like this and couldn't find any help for users, so forgive me using this space if it's incorrect...
My name is Mollie.
Thank you for your reply and advice. I'd like to ask your patience while I lament?
In our situation, it was a case of a medical/building emergency, where we were suffering from (what we found out) was mold sickness. It was a project that was grandfathered in because there was no time alloted us for prep. But, we are almost 65, with little opportunity or savings to undo and pay for this all over again.
Once we found anyone at all who would do exploration, remediation and rebuilding (it took 5 months of horrible tradespeople not showing up, not responding back etc.); we had just 24 hours to move out and one week left before the rains to get it all done.
没有时间让我们得到教育,因为we weren't even aware of the extent of the damage and mold problem. And, we couldn't finance, so we had to pay most of our savings for winter living to get this done in a hurry. Our insurance wouldn't cover it.
Our construction guy sent us to buy our own materials from his list, so we could choose safer, greener options than what he knew about; as well as to save a bit of money if we could. He supposedly knew what he was doing and we had to trust it to him.
. I hoped he would know all the questions. I didn't know what questions to ask, except for how quickly, how affordably and how green they can fix the problem. The technical stuff is what a person hires someone else to know, don't they?
It was rather like going to the emergency ward, and you don't have the time or the luxury of investigating your attending physician's knowledge or credentials. You just want to not be sick anymore. For me, personally, the whole 10 days of moving, remediation, rebuilding, and loss of all our money was so traumatic that I couldn't think straight or function normally at all. It was simply too overwhelming.
I forgot to mention, this is a double-wide mobile home, where the addition was originally a deck and shed combo. It was enclosed in 1994, I think. At least, that's what I found out in this process. There was previously only 3.5 inches of rigid foam insulation snugged between roof sheathing and drywall, with no openings except for the eaves end, where it was left wide open.
I really would like a low or zero off-gassing type of insulation because of sensitivities. That's paramount.
So, you can see...planning in the usual sense, was something I had no time for. We just put our faith in the people we hired, hoping that they knew all the questions and answers. We specifically hired someone who had 30 years of building experience. I researched the dickens out of all the issues best I could. But, I am the only one in this couple who has internet knowledge, and it has been a very life-changing and traumatic experience for me. Actually, I feel like I have been robbed, and both of us are feeling distrustful and unsafe. How can we "little people" know EVERYTHING there is to find out? My due diligence (anal as I am) was still not enough. Lack of time had me scrambling, pulling long hours to get as much info as I could before the next irreversible step was completed. Extreme stress!
If it was such an impossible assembly, I had hoped that at least a couple of the several tradespeople I had opinion it before the roofing was put on; would have brought it to my attention. But everyone said it was a solid build. Seems when you don't have any experience in these things, no one will be your advocate.
So, your advice is just to use the polyurethane foam, which is dangerous to our health?
But, in another post on here, I felt a glimmer of hope when you advised the person that a flat roof should "never be vented. Period." Did I take that out of context?
Thanks for your help. Wish I felt better...feeling hand-tied instead; afraid to do the wrong thing again, so sitting with a cold empty space. And broke....but no mold at least! Can't leave it like this.
Mollie,
The vast majority of installations involving closed-cell spray foam result in success, without any lingering odors or health issues. That said, if you choose this option, you should vacate the premises for at least three days while the work is done, and have the room ventilated with fans after the spray foam is installed.
If you suffer from multiple chemical sensitivity, all bets are off. I can't really advise you; you'll need to experiment by testing your reaction to different insulation materials to understand what your body is sensitive to.
Most low-slope roofs are insulated with rigid foam insulation above the roof sheathing. These are unvented assemblies. If you prefer that approach, it may still be possible, although you'll have to pay for new roofing.