Has anyone ever kept sheathing warm and saved labor costs this way?

There are a handful of manufactures who make rigid insulation with OSB bonded to the surface (like a SIP with OSB on one face only. But SIPs are not the topic in this post). This assembly is commonly used for roofing but I was contemplating using it backwards as exterior wall sheathing. By backwards I mean fastening it onto the studs so the OSB is touching the studs and the foam is on the outside. By doing this, the osb is kept warm and that desirable thermal break is incorporated as well (after all thats generally the reason to put rigid on the outer face).
我thought of this because the labor associated with applying an independent layer of rigid insulation after the sheathing has been installed can almost equal the cost of the insulation in this region (suburban boston).
Has anyone done this?
What are the complications I am failing to see?
我f you did this would you tape the joints and skip house wrap or include house wrap?
As always, I look forward to your thoughts and observations.
GBA Detail Library
A collection of one thousand construction details organized by climate and house part
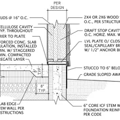
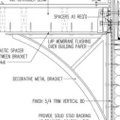
Replies
肖恩- There is a company that makes this product. They have Neopor outboard of the OSB and there are special fasteners they use so the product can still be used as structural sheathing. I have a sample in my house that I will try find so I can get you the name.
我think you are describing the Zip-R product, that is made up of a coated 7/16" OSB that acts as a water and air barrier, which is bonded to a layer of continuous foam (either 1/2" R3.6 or 1" R6.6). However, with the ZipR you install the OSB to the outside.
肖恩, can you please specify which particular similar products you are referring to that are commonly used for roofing? The ZipR system product literature specifically states it is not approved for roof deck use.
我'm interested in this because it seems there is far more benefit to the continuous foam to prevent thermal bridging on the roof than there is on the wall, if you are in a budget situation where it is either/or.
肖恩is talking about nailbase, which is usually installed on roofs but which can be installed on walls.
Thanks Martin.
Some quick googling indicates that Nailbase must be installed over a structural roof deck. Is that the case with all such products?
我f so, they are a layer in addition to the "standard" method, where the cost of materials & labor is 100% add over standard, instead of a product to use "instead' of, where the cost is just the premium over the standard method. Any ideas what the furnished and installed sf cost of such nailbase is?
Here is the brochure for the ThermalStar exterior sheathing that has EPS attached outboard of the OSB. Note that they say their specialized fastening system goes through the EPS and sits against the OSB to maintain the shear strength.
http://atlaseps.com/wordpressfiles/wp-content/uploads/2015/09/LIT-1039-LCi-SS-Sell-Sheet-092915.pdf
Jonathan, Thanks for the link. That is an interesting product that seems to do exactly what I am describing. According to Martin's article "Calculating the Minimum Thickness of Rigid Foam Sheathing" a 2x6 wall needs 1.5" of rigid. The product comes in that thickness (though they suggest that thickness for zone 6 while I'm in zone 5).
我also like the fastening system as it draws tight to the sheathing thereby providing proper bracing (unlike the Zip R which I think requires additional bracing) and does not leave room for sag.
On the surface this looks like a great example of value engineering as it is intended to be - bringing value without reducing quality. If anyone has had good or bad experiences with this product please share.
Thanks.
Just wondering. For zone 6, a 2x6 wall needs R 11.5. An inch and a half of EPS would be on the order of R 6 to maybe R 7, depending on the specific product. Is that all that is needed for zone 5? If it is polyiso it would probably be stated to have an R value of more like R 9, but don't forget the reduction in performance at cold temperatures.
Howard, I am just going by the table and a few lessons from way back in the stone age when I was in school. Table N1102.1 calls for R 20 or 13 + 5. Unless the insulation is really poor that's based on a 2x4 wall. By old school rules of thumb that arrangements is consistent with is 30 - 33% of the R value should be outside the sheathing to keep it warm. If we apply that thinking to a 2x6 wall with FG insulation yielding about R 19 an 1.5" of XPS at R7.2. That value is only slightly below the rule of thumb value so although more insulation would be better I would imagine 1.5" will serve the general purpose. It is also a nice dimension because it allows windows to be built out to align with the face of insulation easily and that kind of practicality offers a lot of value and peace of mind.
Your numbers are different than mine so I think you must approach the matter with different resources, logic, and rules. I do not consider myself an expert or that my logic is the only way so I would be very pleased if you'd educate me further on the topic and how you arrived at your conclusion (I am not being sarcastic). This site has been a terrific learning resource for me. Thanks
肖恩,
Here is a link to an article that discusses the topic:Calculating the Minimum Thickness of Rigid Foam Sheathing.
Thanks Martin. I have read the article and referred to it above. It is an excellent article. Thanks
BTW Martin, you should consider taking Sunday nights off!
No rest for the wicked ;)
肖恩:
My bad. I was doing a quick "just wondering", and working from my memory of my zone 6 numbers, which come from the sources Martin uses (I think originally from BSC research). I just looked at that again from his link above, and while my memory was correct me, it looks like R 7.5 is what you need for zone 5. I should have checked before I spoke (wrote). Sorry.
No sweat Howard. Martin's article is a good source and a well stated explanation. I never memorize any of this stuff (my brain doesn't work that way anymore) so I think I have referred back to that article a dozed times since it was posted. Good luck.
作为一名建设者,这听起来像是个糟糕的主意。我don't know who is framing the house (you or a contractor) but it will slow the framing to a crawl. Sheathing is typically installed while the walls are still flat on the ground, and involves a lot of cutting and moving sheets around.
我f you use this technique, you'll have a much harder and slower time, and you won't know if you hit the studs until later. The chances of missing are pretty good if you're going thru several inches first.
And I seriously doubt there's anything special about this product. The issue is getting shear strength from the sheathing, but if you're setting the fasteners hard to the OSB, there's nothing more required than what you'd get from standard nail base and a wood screw rated for the strength you need (which I'd guess would be pretty much anything stronger than a drywall screw).
把泡沫后的房子是再保险asonably quick process. Still a pain in the ass, and I am a much bigger proponent of double-stud walls with dense pack. I am unconvinced that cold sheathing is a serious issue. I call it the Yeti of building science - much discussed, rarely seen.
Foaming the wall, taping the seams and furring out is not as big and bad a thing as so many think. It takes time, but it is a good et toed on 1x4 fur strips which are actually 3/4"x3 1/2" and I used 2.5" eps foam with 6" HeadLok screws directly into framing. I am doing it now and it is before the insulation is in so we know what is on the other side of that wall. I am also using some timber brackets that are attached by HeadLok screws as well so we have solid blocking up where needed and have the ability to add blocking if needed in spots, even to catch the screws that hold the furring strips. It really isn't rocket science, but it does take some time. I believe in the system. I alSo believe that in twenty years if my walls are opened up, it will be dry as a bone in there.
A drawback of nailbase not mentioned yet is that the EPS always shrinks. When it shrinks, the panels warp really badly.
Two layers of exterior foam are also much easier to air seal and weather seal than one layer of nailbase.
Thank you all for the great responses. It is a lot of food for thought. I especially enjoy the mix of sources who respond to these posts - constructors, designers, environmentalists, etc. the well rounded responses inspire truly critical thinking.
Thanks