High relative humidity in below-grade slab and flooring
I live in the Denver area and am remodeling the below-grade area of the house. It’s slab on dirt, without capillary break (1958), about 4′ below grade, and with soil that is 60% Sand, 20% Silt, 20% Clay.
我有一个使用无聊孔方法的木质干混凝土水分表,并测试了许多位置。
I’m consistently getting readings 80-93% RH, and I had the RH probe calibrated to confirm it is not off.
Significant drainage work has occurred around the house, with no evidence of bulk moisture, though a seasonal irrigation ditch/stream runs in the front yard, about 100′ away, and this soil drains very well. It is also an atypical year with high precipitation.
如果我要密封或蒸气屏障,则裸露的平板会导致构架的腐烂或干燥的板块,而框架上置于平板和茎壁上?新的框架用下面的浓密胶水处理,但谁知道1958年的框架。
谢谢。
GBA Detail Library
A collection of one thousand construction details organized by climate and house part
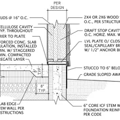
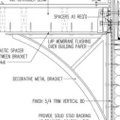
Replies
罗斯,
解决这种类型问题的通常方法是在平板上方安装一层聚乙烯,然后是一层刚性泡沫,然后是胶合板或OSB亚底线。有关更多信息,请参阅本文:"Installing Rigid Foam Above a Concrete Slab."
我不会太担心现在碰到混凝土的墙壁的底板。理想情况下,这些底板应受到压力处理,但是您是正确的,因为使用较旧的房屋,使用经过处理过的木材的可能性较低。就是说,我不必担心尚未发生的腐烂 - 问题的机会相对较低。
> If I was to seal or vapor barrier the exposed slab, would this potentially lead to rot
当然,较少的混凝土干燥将导致混凝土湿润。这增加了与木材接触的风险。足够引起问题?在猜测这一点时,我会对当前的木材水分含量更感兴趣。即,如果它远低于危险水平,那么更多的水分就不会受伤。
Martin and Jon, thanks for your feedback. Yes, I was considering a similar assembly, but using MgO board instead of Plywood, which is mold resistant and not affected by water/moisture. I've had water pipes break previously, as well as sewage backup and would only consider a water tolerant assembly. With this (using 5/8" high PSI EPS), I can get to an R3 at 1-1/4" thick, which helps a lot at stairs, etc. This is similar to Basement System's assembly, though they use thicker graphite EPS and very thin MGO.
My primary concern was not being with the current level of moisture, rather if I would drive up the moisture to a dangerous level by covering the slab where framing doesn't exist. I spoke with many flooring persons, and was eventually directed to a mfg sales rep who does large mitigations and is very familiar with this situation, and sees these types of RH values somewhat regularly here in CO (oddly, the flooring guys all were surprised by my numbers and he was not). He was not concerned about a dry rot situation, even with very high slab humidity. The below product would create a tiny gap and vapor barrier between the subfloor and flooring material and allow for air exchange and breathing at the wall. So, I would not have to worry about driving up slab moisture levels as much as a traditional vapor barrier:
http://www.uzin.us/uploads/tx_dddownloadmatrix/rr_185_pds.pdf
In the event of a bulk water issue, my thought is to remove the Vinyl Plank, pull up this material, hole-saw through the MgO and insulation and vacuum out some moisture in each room, then run a lot of flooring fans and dehumidifiers until dry. After that I could replace the vapor barrier and waterproof flooring. Not that it would be easy, but I wouldn't have to replace the subfloor or buy new flooring.
My only concern is that many of the manufactured subfloor manufacturers create channels on the concrete side of their foam for air exchange and I would not have those. That said, the EPS and MGO would have pretty decent permeability (60 psi foam would have 2.5 perms and absorb only 0.03% H2O).